Abstract
Titanium and its alloys are widely used for various structural applications due to their high melting point, specific strength and excellent corrosion resistance particularly in seawater. Though titanium is relatively expensive compared to other structural metals (such as iron, nickel, and aluminum), it is still used for certain critical applications, such as parts in the lower temperature regimes of aircraft gas turbine engines as well as many marine applications.
Titanium and its alloys are widely used for various structural applications due to their high melting point, specific strength and excellent corrosion resistance particularly in seawater. Though titanium is relatively expensive compared to other structural metals (such as iron, nickel, and aluminum), it is still used for certain critical applications, such as parts in the lower temperature regimes of aircraft gas turbine engines as well as many marine applications. As the applications of titanium and its alloys become increasingly wide spread, there is a demand to develop more productive welding methods to meet the varied needs of different applications. But, titanium is extremely reactive with interstitial elements (O, N, H, C) when exposed to temperatures above 650°C.
The basic difficulties in welding titanium and its alloys economically are due to two primary factors:
1) shielding the weld metal and heat affected base metal from the harmful atmosphere and
2) overcoming titanium's extreme resistivity (compared to other common metals) which precludes welding by highly productive processes such as submerged-arc, flux-cored arc and gas-metal arc welding. Therefore, welding must always be performed under vacuum or in a controlled inert gas environment by processes that do not electrically heat (i.e. by ohmic heating) up the titanium filler metal. As a result, the only commercial methods of welding titanium alloys today include: gas-tungsten arc, laser and electron beam welding.
Compared to other processes, ESW has many advantages including: one pass operation, high welding speed, no preheating necessity, less welder skill requirement, non-machined joint preparation, and less angular distortion. It also produces very high quality welds, since the slag pool protects the weld metal from the atmosphere.
Electroslag welding (ESW) is a process that melts and joins metals by heating them with a pool of molten slag held between the metals and continuously feeding a filler wire electrode into it, as shown in Figure 1. The weld pool is covered with molten slag and moves upward as welding progresses. A pair of water-cooled copper shoes, one in the front of the workpiece and one behind it, keeps the weld pool and the molten slag from breaking out. Similar to SAW, the molten slag in ESW protects the weld metal from air and refines it. Strictly speaking, however, ESW is not an arc welding process, because the arc exists only during the initiation period of the process, that is, when the arc heats up the flux and melts it. The arc is then extinguished, and the resistance heating generated by the electric current passing through the slag keeps it molten. In order to make heating more uniform, the electrode is often oscillated, especially when welding thicker sections.
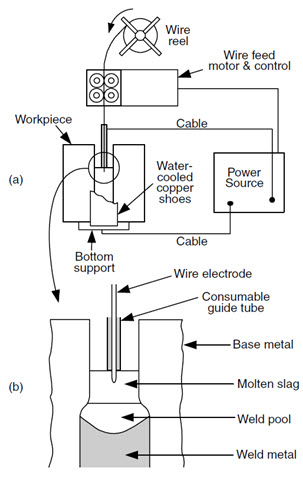
Figure 1: Electroslag welding: (a) overall process; (b) welding area enlarged
Figure 2 shows the main types of joints that can be welded by ESW process include butt, fillet, corner, transition, T-joint and the cross weld.
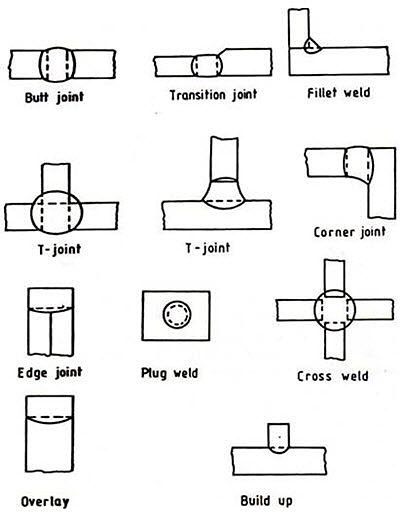
Figure 2: Joint designs for ESW