Abstract
Electro-slag welding is a primary method for cast weld assemblies of heavy sections since one of the key characteristics is its suitably high deposition rate.
Some key advantages include a single pass process, weld symmetry, high welding speed, simple joint preparation and low flux composition.
The Electro-slag welding (ESW) process has some characteristics of submerged-arc welding in that it is used for welding in the vertical position and the method utilizes bare electrode wires which are fed continuously into a molten slag pool contained between water-cooled dams.
The ESW process begins with an arc to melt the flux and create a pool of molten slag. The arc is then extinguished and a molten pool of weld metal and base metal is maintained by the heat generated from the resistance of the flux to the passage of current from the electrode to the base metal. The metal solidifies as the water-cooled dams are moved upward. The ESW process is shown schematically in Figure 1.
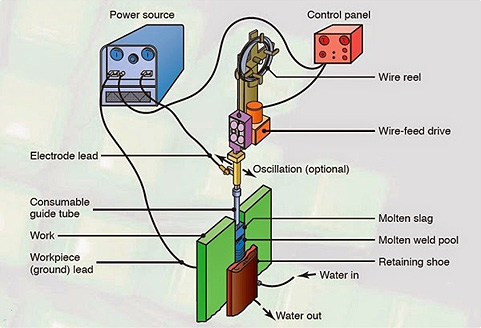
Figure 1:Schematic of the ESW-e1ectros1ag welding process
The ESW process was first developed in the USA in the late 1930s, and the process is described in a series of patents (Hopkins 1940). It was further developed at the E.O Paton Institute in Kiev, in the Ukraine, and has proved very capable of joining thick section steels and other materials.
The ESW process is primarily useful for cast weld assemblies of heavy sections because of the very high deposition rates. Because of this high deposition rate and minimal joint preparation, the process could have limited applicability to very large weld repairs in carbon and low alloy steel. The process is limited to use in the vertical position.
Applications:
• ESW is often used in structural box columns and wide flanges.
• Manufacture of large presses and machine tools.
• Other machinery applications include kilns, gear blanks, motor frames, press frames, turbine rings, shrink rings, crusher bodies, rebuilding metal mill rolls and rims for road rollers.
• Pressure vessels for the chemical, petroleum, marine, and power generating industries.
Advantages:
• Electro slag welding can have extremely high deposition rates, but only one single pass is required no matter how thick the work-piece is.
• Unlike SAW or other arc welding processes, there is no angular distortion in ESW because the weld is symmetrical with respect to its axis.
• High Welding Speed and good stress distribution across the weld.
• Joint preparation is often much simpler than other arc welding processes.
• Residual stresses and distortion produced are at a low level.
• Flux composition as compared to submerged arc welding (SAW) is very low.
Disadvantages:
• When the heat input is very high, the weld quality can be rather poor, including low toughness caused by the coarse grains in the fusion zone and the heat-affected zone.
• In ESW, there is some tendency toward hot cracking and notch sensitivity in the heat affected zone.
• Logistically, ESW is restricted to vertical position welding, because of the large molten metal pools and slag.
• It is difficult to close cylindrical welds.
• Electro slag welding tends to produce large grain sizes.
• SAW is more economical than ESW for joints below 60 mm.
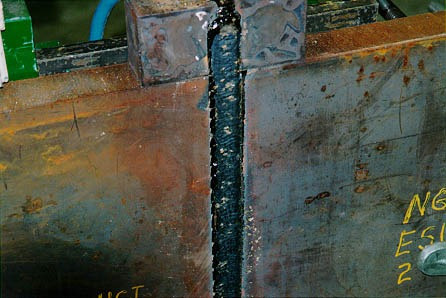
Figure 2:ESW welds