Abstract
Direct-Chill (DC) casting, developed in the 1930s, represents the primary semi-continuous casting method for producing non-ferrous billets and ingots. This process employs a sophisticated cooling system comprising primary mold cooling, secondary water cooling, and bottom block cooling. Its key advantage lies in the controlled solidification process, where defects are effectively contained within a narrow surface layer of the billet. This article explores the fundamental principles, operational procedures, and industrial applications of DC casting, highlighting its significance in modern metallurgical practices.
Introduction to Direct-Chill Casting
Direct-chill casting has revolutionized non-ferrous metallurgy since its commercial introduction in the 1930s. The process employs a unique combination of water-cooled molds and direct water impingement to achieve controlled solidification of metal billets and ingots.
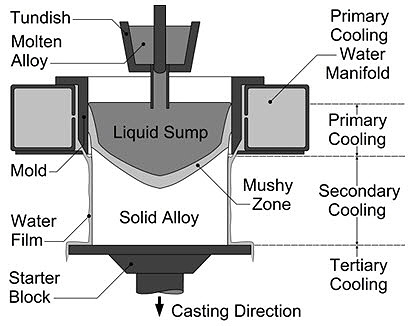
Figure 1: DC caster components and cooling regions during steady-state casting
Process Mechanics and Cooling Zones
The DC casting process utilizes three distinct cooling zones:
- Primary mold cooling
- Secondary water cooling
- Bottom block cooling
During operation, molten metal flows through a water-cooled bottomless mold, where initial solidification occurs at the outer surface. This solidification provides sufficient mechanical strength to maintain the molten core while the ingot takes the mold's shape.
Operational Procedure and Secondary Processing
The process begins with a starter block positioned slightly above the mold's lower lip. After filling the water-cooled copper or aluminum mold with molten metal, the starter block gradually descends into a casting pit, carrying the solidifying ingot. Heat transfer occurs from the liquid metal to the mold through the water manifold circulation system.
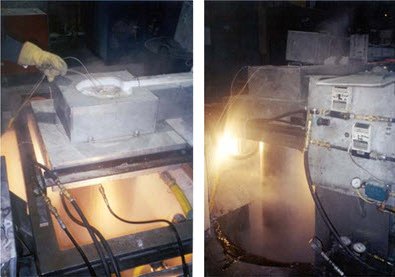
Figure 2: Direct Chill Casting: mold and ingot
Post-casting, DC cast products undergo various secondary manufacturing processes:
- Round billets are typically extruded into diverse aluminum products
- Rectangular castings undergo homogenization and scalping before rolling into plate, sheet, or foil
- Some applications involve creating bimetallic sheets by rolling together ingots of different compositions
Quality Control and Defect Management
The primary advantage of DC casting lies in its controlled solidification process. Understanding the complex interactions of melt flow, thermo-solutal convection, grain nucleation and growth, solidification shrinkage, thermal contraction, and feeding restrictions is crucial for defect prevention and quality control.