Abstract
Continuous Reduced Iron Steelmaking Process (CRISP) is a creative steelmaking technology which uses stationary electric arc furnace to continuously melt and decarburize DRI and other metallic materials to produce steel.
The main benefits of CRISP include cost savings through improved yield, increased furnace refractory life and a greatly reduced total specific energy requirement, to name but a few.
Numerous advancements have been made in the DRI-based steelmaking processes in the last decade. Charging hot DRI to the electric arc furnace (EAF), directly from a DR module is arguably the most important improvement in this area. The energy saving associated with the hot charge practice is estimated around 20 to 30% compared to the current cold-fed EAFs. Nevertheless, continuous discharge of hot DRI to EAF is complicated by the batch operation nature of the EAFs.
Continuous Reduced Iron Steelmaking Process (CRISP) is a novel steelmaking technology, being developed by Hatch that utilizes a stationary electric arc furnace to continuously melt and decarburize DRI and other metallic materials to produce steel. The key feature of CRISP technology is significant modification of the conventional EAF process parameters to extend the refectory life beyond one year.
The flowsheet of CRISP is shown in Figure 1. As depicted, DRI is produced in the DR or reduction furnace and fed to the furnace, along with scrap and iron oxide. The charge materials are fed continuously into the CRISP furnace that is essentially a six in-line electrode stationary EAF. Continuously operated CRISP EAF close links two processes: DRI production in the reduction furnace and continuous casting.
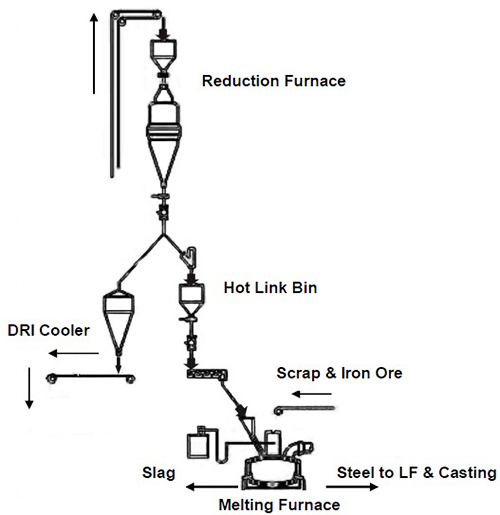
Figure 1: Flow diagram of a CRISP plant The decarburization of DRI is accomplished with zero gaseous oxygen and through the oxidation by slag; that is supplied with iron oxide as ore lump, pellet or mill scale. Since the charge is introduced into the furnace continuously, it is critical to adjust the specific rate of material feeding in order to meet the requirements for sufficient decarburization inside the furnace. Steel and slag are periodically tapped out through slag and metal top-holes in a similar approach to BF. After steel is tapped out, the remainder of the process is similar to the conventional steelmaking including ladle refining and casting.
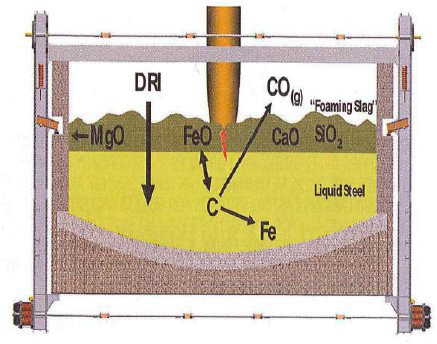
Figure 2: Schematic diagram of CRISP furnace The essence of the unique features of the CRISP technology is:
- Continuous melting without downtime for charging, tapping or fettling;
- Large liquid heel with the attendant long residence of metal in the furnace;
- Power density in the range of 300 to 500 kW/m2 of hearth, a fraction of the level on a conventional EAF, typically 2,500 kW/m2 to 3,000 kW/m2;
- The ability to decarburize to low levels of carbon (> 0.04 wt% C) without the use of gaseous oxygen.
These differences lead to significant operational benefits, the most important being:
- Decarburization is accomplished at slag FeO levels closer to equilibrium;
- The related improved yield provides meaningful savings in the cost of metallics;
- Furnace refractory life is measured in years rather than weeks or months;
- The high furnace availability, approaching 8,000 hours/year, leads to improved plant logistics (matching) with upstream and downstream facilities;
- The shielding of the arcs is accomplished by utilizing the foaming slag inherent to the continuous melting of DRI;
- The low gas velocity in the furnace freeboard significantly reduces the amount of dust carried over from the furnace. This not only reduces the dust disposal costs but also allows the charging of fine materials to the furnace, a cost-effective measure;
- The total specific energy requirement – power, oxygen, natural gas and carbon – is lower than on a conventional EAF; in the comparison case: 610 kWh/tonne liquid steel versus 756 kWh/tonne liquid steel;
- The continuous nature of the CRISP operation together with the furnace design allows the furnace off gas to be captured and utilized as a fuel gas;
- The steady even furnace power load of the continuous CRISP operation reduces the demands on the electrical utility grid, it also enhances the feasibility of connecting to a captive power plant;
- The GHG (Green House Gas) footprint and especially the NOx emissions are significantly lower.