Abstract
Five alloy families are described, with a table of seventeen bearing bronzes, with their UNS alloy designation and standard specifications covering each. Members of each family have similar properties, with differences among family members allowing selection based on economic considerations or on the need to tailor alloys for particular applications.
Leaded Bronze
The tin content of 4 to 10% in leaded bronze increases strength, maximum load capacity, fatigue resistance, and hardness above what is available with simple copper leads. Zinc is sometimes used as a replacement for tin, and nickel is often added to improve corrosion resistance and toughness.
Leaded bronzes have better compatibility than tin bronze because the spheroids of lead smear over the bearing surface under conditions of inadequate lubrication. These alloys are generally a first choice for intermediate loads and speeds. They are used in machine tools, home appliances, farm machinery, and pumps.
Tin Bronze
These alloys have high hardness, thus require reliable lubrication, good alignment, and a minimum Brinell shaft hardness of 300 to 400. They are used in high-load, low-speed applications such as trunnion bearings, gear bushings for off-road vehicles, rolling-mill bearings, and in internal combustion engines for connecting-rod bearings, valve guides, and starters.
Cast-bronze bearings offer good compatibility, casting, easy machining characteristics, low cost, good structural properties and high load capacity. They do not require a separate overlay or a steel backing.
Aluminum Bronze
Bronzes of high strength are obtained by using aluminum, iron, manganese, silicon, and nickel as alloying elements. Such bearings have excellent shock and wear resistance. They retain high strength at high temperatures and are used in equipment operating above 250°C. A major use is in high-impact sliding surfaces in aircraft landing gear. Because aluminum bronze has poor compatibility, embeddability, and conformability, it is best suited for heavy-duty, low-speed applications with plentiful lubrication. Aluminum bronzes require harder shafts than softer bearing materials. Proper alignment is more critical because of low conformability.
Beryllium Copper
Adding about 1.8% by weight of beryllium and about 0.2% cobalt to copper provides an alloy with strength comparable to many steels. The high strength, hardness, and thermal conductivity of the alloy promote its use in high load bearings, especially where reliability is required under occasional overload, impact, high temperature, or marginal lubrication conditions. These alloys are used in electrically conducting applications and are frequently specified for aircraft landing gear and other airframe sliding surfaces.
Bearing Bronzes Grades
The bearing bronzes are listed in Table 1 by their UNS alloy designation with standard specifications covering each. The seventeen bearing bronzes listed fall into above mentioned five alloy families with similar compositions and properties. Members of each family have similar properties, with differences among family members allowing selection based on economic considerations or on the need to tailor alloys for particular applications.
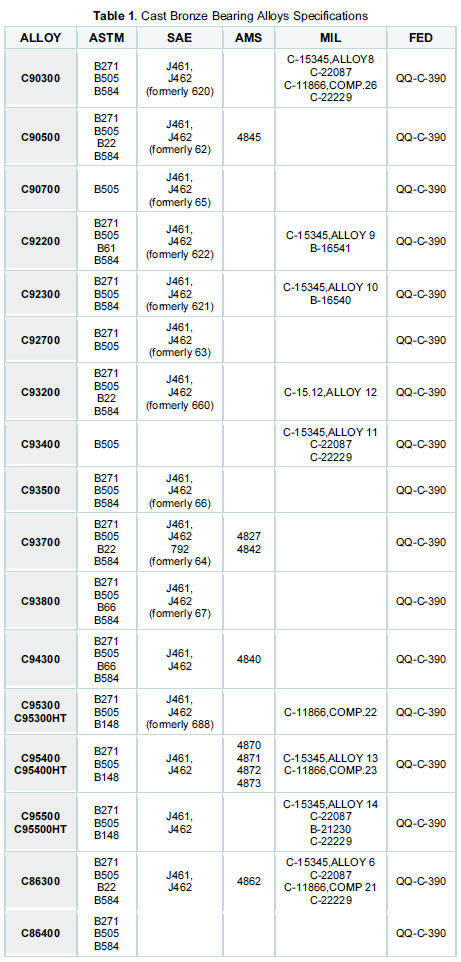