Abstract
Although after the transient startup phase the process of cold extrusion is classed as steady-state, in reality, due to changing contact conditions and in process temperature variation this is not accurate.
There are however a wide range of useful benefits from cold extrusion including elimination of welding connections, flexibility of branch positioning, seamless metallurgical integrity and extended service life of the materials to name but a few.
Extrusion is a discontinuous process in which the second billet is not loaded until the first billet is extruded. During the start-up of extrusion, the extrusion load increases as the material is forced to fill the container and flow out of the die. After the transient start-up phase the process is often considered to be in steady-state. In reality the process is never in a steady-state phase since the contact conditions are constantly changing and the temperature varies during the process. Steady-state may however be a good approximation if the friction is negligible and the temperature changes are small. The material flow however, is steady-state during the greater part of the extrusion process and when the billet has been extruded to a small discard there is high resistance to radial flow towards the center and the load increases heavily. Extrusion is then interrupted.
Benefits of cold extrusion
Cold extrusion is used extensively in the engineering sector and provides significant benefits compared to welding and hot extrusion including:
- Elimination of the most critical welded connections in piping systems
- Total flexibility of branch positioning
- Closer spacing than using forged tees
- Metallurgical integrity (seamless)
- Smooth profile
- Reduced stress concentrations
- Improved flow characteristics
- Increased fatigue resistance
- Extended service life and reduced maintenance
- Cold forming is allowed for Austenitic stainless and nickel Alloys
- high dimensional stability
- excellent surface finish
- continuous fiber flow line thanks to forming
- efficient process for mass production.
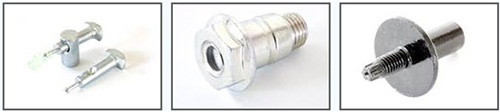
Figure 1: Cold extrusion products
Cold extrusion processes are known to give a high output capacity and to permit near-net shape production e.g. of automobile parts. During cold extrusion, large plastic deformations develop due to the large reduction of the work piece cross section. These large plastic deformations result in a grain elongation as well as in a change of grain orientation. The plastic deformation is inhomogeneous throughout the work piece cross section, thus texture gradients as well as residual stresses arise.
The sign, the magnitude and the distribution of the residual stresses severely influence the fatigue limit and the stress corrosion resistance of the work piece. Here, in order to study the texture and the residual stress distribution of cold forward extruded steel samples a recently developed new method using white high energy synchrotron radiation has been employed in addition to X-ray and neutron diffraction.
The samples analyzed in the work of Puzzala A. et al was a German steel grade C15 which were full forward extruded to rods of 15 mm diameter at the Institut für Umformtechnik, Universität Stuttgart, Germany, varying process parameters, e.g. the conversion ratio φ (φ=0.9; 1.2; 1.6) and the ejection mode.
The material flow during the extrusion is visible in the microstructure of the samples. While in the rod kernel a homogeneous elongation of the grains exists (Figure 2) the material flow is obstructed due to friction at the surface of the samples, thus the microstructure near the surface is less homogeneous and the grains are less elongated. Transmission electron microscopy reveals that at high conversion rates the dislocations build cell structures (Figure 3).
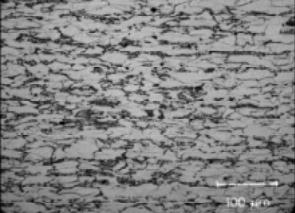
Figure 2: Microstructure in the centre
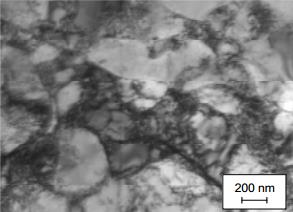
Figure 3: Dislocation cells