Abstract
Bainite hardening (austempering) represents an advanced heat treatment technique that has gained significant traction in industrial applications, particularly in the bearings industry. This article explores the metallurgical fundamentals of bainite formation, contrasting it with other microstructures like martensite and pearlite. It examines the distinct characteristics of upper and lower bainite structures and their respective hardness properties. Various cooling strategies are analyzed, including continuous and isothermal approaches, alongside innovative multi-stage processes designed to optimize processing time while achieving desired mechanical properties in steel components.
Introduction to Bainite Transformation
Austenite transformation in steel produces different microstructures depending on cooling rate and alloy composition. Martensite, formed at rapid cooling rates, delivers high hardness but exhibits brittleness until tempered to reduce residual stresses and dislocation density. Pearlite, which develops at slower cooling rates and higher temperatures, consists of a lamellar structure where ferrite and cementite grow side by side through edge growth, resulting in a softer, more ductile structure unsuitable for high-pressure applications.
Bainite forms at intermediate temperatures (550°C down to the martensite start temperature Ms), where carbon diffusion becomes sluggish. This results in a non-lamellar, fine, and complex structure where ferrite acts as the leading growth phase, while cementite precipitates when sufficient carbon concentration accumulates in the surrounding austenite or ferrite. The growth mechanisms of bainite remain a subject of scientific debate, with two primary theories: diffusionless transformation and diffusional transformation, each explaining distinct aspects of this complex microstructural development.
Metallurgical Fundamentals of Bainite
The microstructure of bainite varies significantly based on the isothermal transformation temperature. Two distinct structures can be achieved: "upper bainite" and "lower bainite" (Figure 1).
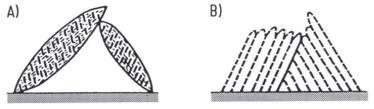
Figure 1: Structure of bainite needles showing A) lower bainite and B) upper bainite structure
The hardness of bainite ranges from approximately 40 HRC for upper bainite to 60 HRC for lower bainite. This hardness increase mirrors what occurs in pearlite formation, reflecting the decrease in size and spacing of carbide platelets as transformation temperature decreases. The finer microstructure at lower temperatures contributes to enhanced mechanical properties.
Cooling Strategies for Bainite Hardening
The achievable cooling rates during bainite hardening depend on multiple parameters, including:
- Quenching speed of the salt bath
- Salt bath temperature
- Agitation level of the quenching media
- Dimensions and weight of the components
- Loading density
Figure 2 illustrates different cooling approaches through both continuous (A) and isothermal TTT-diagrams (B) for SAE 52100 (100Cr6) bearing steel.
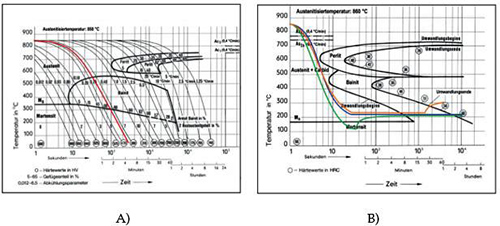
Figure 2: Diagram showing possible cooling strategies for bainite hardening: continuous cooling (red), isothermal cooling with dwell time for desired hardness and structure (blue), and multi-stage process (green, orange)
For larger components or those with greater wall thickness, continuous quenching often fails to prevent bainite formation, resulting in inhomogeneous microstructures with varying bainite types. Achieving a homogeneous structure requires careful matching of material grade and quenching bath capabilities to ensure cooling curves bypass both the pearlite and bainite "noses" during isothermal quenching.
The time required to complete bainitic transformation can be extensive, increasing with higher alloy content (especially nickel or molybdenum) and lower salt bath temperatures. To reduce dwell time, two effective strategies have emerged:
- Increasing the dwell temperature toward the end of bainitization
- Quenching components slightly below martensite start temperature to create martensite "seeds," followed by holding at bainitization temperature
Optimizing Process Time in Bainite Hardening
Table 1 demonstrates how varying austempering temperature can significantly reduce dwell time for bainite hardening of bearing steels austenized at 845-860°C. Strategic temperature adjustments can shorten the required dwell time by 60-70%.
Table 1. Cooling strategies for bainite hardening of bearing steel showing how different approaches affect processing time
Steel type |
Temperature [°C] |
Duration [h] |
Hardness [HRC] |
100Cr6 |
225 |
7.5 |
60.1 |
100Cr6 |
210 |
2 |
— |
100Cr6 |
250 |
1 |
60.0 |
100CrMo 7 3 |
210 |
33 |
60.1 |
100CrMo 7 3 |
210 |
9 |
— |
100CrMo 7 3 |
250 |
1 |
59.9 |
Historical Development and Modern Applications
Bainite hardening traditionally relied on salt bath technology. Approximately 25 years ago, interest in bainite hardening declined as salt bath methods faced challenges related to cleanliness, safety, and environmental concerns. Modern advances have addressed these issues through fully encapsulated, safe salt bath installations with environmentally compliant salt compositions and established recycling protocols for used salts, renewing interest in this valuable heat treatment approach.