Abstract
Aluminum strip casting is a key contributor to weight saving possibilities, particularly in the automotive industry and although strip casting has been established for over 50 years, it continues to increase in popularity.
Casting speeds can be limited by several factors including the type of alloy being cast and the desired sheet thickness required.
In the automotive industry, decreasing weight is one of the most important challenges which needs to be solved and using aluminum alloys instead of the more traditional steels enables a great opportunity to decrease weight substantially of the overall vehicle.
However, sheets of aluminum alloy used for automobile body work are very expensive. Therefore, in order to make use of aluminum alloys cost effective it is necessary to develop a low cost aluminum alloy sheet which can handle the intended application requirements.
The development of continuous casters for aluminum products has been well documented over the past 50 years. Processes are classified according to the thickness that can be produced using either thin slab or strip casting. Thin slab and thin strip casting bypasses the semi-finished product stage, reducing reheating and eliminating a number of rolling steps, thus providing for considerable energy savings and significant improvements in productivity.
Strip casting was commercialized in the early 1950s. Aluminum alloy sheets are mainly produced in a twin roll caster. In this process, the molten metal is introduced between a pair of counter rotating horizontal casting rolls wherein solidification is initiated when the molten metal contacts the rolls. The solid metal shell formed on the roll surface advances toward the point of minimum clearance between the rolls, referred to as the nip. When the metal passes through the nip, solidification is fully completed and the material undergoes deformation as it exits the rolls. Low alloyed aluminum alloys have successfully been strip cast at a thicknesses of ¼ inch at rolling speeds of 4 to 6 feet/min (50 to 70 lbs/hr/in).
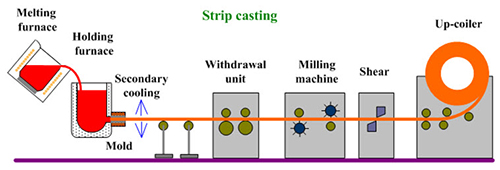
Figure 1: Aluminum Strip casting The casting speed is restricted by the fact that an increase in casting speed will increase centerline segregation in the sheet. In particular, the central zone of the sheet will become enriched with eutectic forming elements (Fe, Si, Ni, Zn) and depleted in peritectic forming elements (Ti, Cr, V, Zr).
Therefore, more highly alloyed materials (e.g. AA5XXX and 6XXX) are more difficult to produce by the strip casting process. Another aspect of the process is that the high separation force required to achieve the desired sheet thickness further limits the casting speed. This is because the aluminum strip is solid when it enters the nip, resulting in a required force of several tons per inch width. Difficulty in achieving uniform heat transfer as rolling speed increases also represents another impediment to increasing process speed. Commercial strip casters can produce strips with thicknesses ranging from 1 to 15 mm.
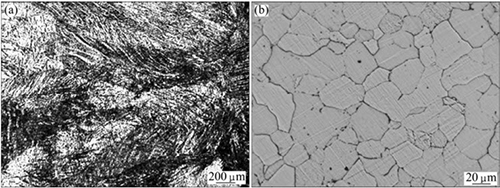
Figure 2: Microstructures of twin-roll continuous cast aluminum thin strip: (a) Solidified organization on cross section of aluminum strip; (b) Local magnification of (a)