Abstract
AlMg alloys have a wide range of advantageous characteristics which means they can be used in many different applications, with many being in extreme temperatures or other aggressive environments.
A prime example of such materials can be seen in the 5xxx series of alloys which display excellent corrosion resistance in combination with very good mechanical properties to cope in the harshest conditions such as marine environments.
Al-Mg alloys of the 5xxx series are strain hardenable, and have moderately high strength, excellent corrosion resistance even in salt water, and very high toughness even at cryogenic temperatures to near absolute zero. They are readily welded by a variety of techniques, even at thicknesses up to 20 cm. As a result, 5xxx alloys find wide application in building and construction, highways structures including bridges, storage tanks and pressure vessels, cryogenic tankage and systems for temperatures as low as -270°C (near absolute zero), and marine applications.
Al-Mg alloys are used in non-heat treatable, sand, permanent mold and die castings. These alloys show good corrosion resistance in most natural fresh waters and in chemical media.
Magnesium has significant solubility in aluminum and imparts substantial solid solution strengthening (which can also contribute to enhanced work hardening characteristics). The 5xxx series alloys (containing <~6% Mg) do not age harden. Whilst it is possible for β-phase (Mg2Al3) to precipitate in systems with above ~3%Mg, the β-phase is not a strengthening precipitate and actually weakens the alloy (by depleting the solute of Mg).
Nominally, the corrosion resistance of 5xxx series alloys is good and their mechanical properties make them ideally suited for structural use in aggressive conditions (such as marine vessels). Fully work-hardened AA5456 (Al-4.7Mg-0.7Mn-0.12Cr) has a tensile strength of >380MPa. One corrosion issue with fully work-hardened 5xxx series alloys is that the heavy dislocation density (and supersaturation of the solid solution with Mg) can permit the sensitization of the microstructure by precipitation of deleterious β-phase (Mg2Al3) during sustained high temperature exposure (i.e. in service).
Al-Mg alloys have various applications in transport, packaging and general engineering industries. As mentioned above, they belong to the group of non-heat treatable Al alloys which derive their strength mainly from solution strengthening and work hardening during deformation. Cold deformation is particularly effective in strengthening since restoration processes are thermally activated.
The strength of Al-Mg alloys strongly increases with the addition of Mg. Mg has a high solubility in solid solutions and therefore it provides the most effective enhancement of strength among all alloying additions in the aluminum solid solution. Mg, like other solute elements, has a strong influence on recrystallization and grain growth. It also serves to reduce both the rate of growth and the final grain size.
Work-hardening wrought Al-Mg alloys which are also known commercially as the 5xxx series aluminum-based alloys are currently being used as automotive BIW materials. Magnesium is the principal alloying element and is added for solid solution strengthening. Generally Al-Mg alloys used in BIW applications have very good formability; relatively low yield stress and work harden during cold working. Alloy grades that have been used extensively as automotive BIW materials are listed in Table 2.3. Nominal values of their mechanical properties are shown in Table 2.4. The alloys are supplied to the BIW press shop in an annealed temper, designated as - O temper.
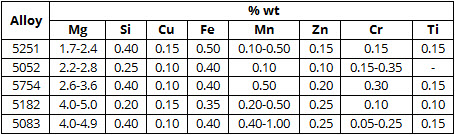
Table 2.3.: Composition of commonly used Al-Mg alloys used for automotive BIW components in weight percent with Al as remainder
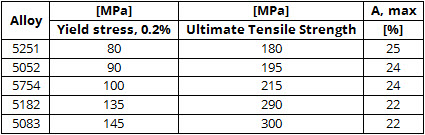
Table 2.4.: Mechanical properties of commonly used Al-Mg alloys used for automotive BIW components
5xxx - Al-Mg Alloys Information
- Strain hardenable
- Excellent corrosion resistance, toughness, weldability; moderate strength
- Building & construction, automotive, cryogenic, marine applications
- Representative alloys: 5052, 5083, 5754, etc.
- Typical ultimate tensile strength range: 124-350 MPa (18-51 ksi)