Abstract
Most commonly known for their excellent strength, corrosion resistance and low density, titanium alloys are a key material for important applications in the aerospace and medical industries.
Duplex heat treatments of Ti alloys helps in stress relieving, optimizing ductility and machinability properties and increases strength further.
High strength, low density, and excellent corrosion resistance are the main properties that make titanium attractive for variety of applications including aircraft parts, biomedical devices or components in chemical processes. Commercial titanium alloys are classified conventionally in three different categories as α, α+β, and β alloys according to their equilibrium constitution, which varies with the types and concentrations of alloy elements.
Commercially pure titanium has an all-alpha structure and demonstrates superior resistance to corrosion but inferior mechanical properties as compared to titanium alloys. Compared with beta titanium alloys, alpha titanium alloys are superior in heat resistance and weldability but inferior in strength and workability. Beta titanium alloys are alloys which are solution strengthened by adding beta structure stabilizers. An all-beta structure at room temperature can be obtained by rapidly cooling the specimen through solution treatment. Alpha phase precipitates in an all-beta structure by aging treatment. Alloys having a beta structure with precipitated alpha phase exhibit excellent strength. Two phase α+β alloys with a dispersion of the beta form in the alpha phase exhibit properties of each phase.
II. Heat Treatment of Ti and Ti alloys
Titanium and titanium alloys are heat treated in order to:
- Reduce residual stresses developed during fabrication (stress relieving)
- Produce an optimum combination of ductility, machinability, and dimensional and structural stability (annealing)
- Increase strength (solution treating and aging)
- Optimize special properties such as fracture toughness, fatigue strength, and high-temperature creep strength.
Within the family of titanium alloys, the α+β alloys are the most widely used because of the great variety of microstructures and mechanical properties that can be obtained by varying their composition and thermomechanical treatments. One of these α+β alloys has the greatest commercial importance namely Ti6Al4V, making up more than half of the sales of titanium alloys.
In order to control the microstructure of titanium alloys, most of the studies in α+β field are focused in the evolution of the primary α phase. In addition, is important to understand the effect of processing parameters on the precipitation mechanism of secondary α phase so as to control the microstructure by processing parameters in the high temperature deformation of titanium alloys.
For α+β alloys as well as for β alloys, the mechanical properties which are relevant for particular applications are optimized for microstructural control. A prerequisite for property optimization is a profound knowledge of the microstructure-property relationships on one hand, and of the microstructure’s evolution as a result of processing on the other hand.
Annealing heat treatments below β transus temperature followed by different cooling rates are carried to hot deformed samples in α+β field. The experimental results show the influence of deformation temperature in the final microstructure after the annealing. A posterior effect of an ageing treatment is also studied after annealing presenting a strong interdependence of the resulting cooling rate on the final microstructure. In addition, a combination of isothermal heat treatments below β transus followed by controlled cooling rates were carried out to samples deformed in the α+β field with the intention to obtain recrystallized structures.
The effect of short-time duplex heat treatment on the microstructure and mechanical properties of Ti–6Al–4V alloy was investigated in the study of T. Morita et al.. This heat treatment consisted of solution treatment at 1203K for 60 s and subsequent water-quenching plus aging at 753 K, 853 K and 953K for 40 s. The yield strength and tensile strength of the alloy were significantly increased by the above heat treatment and their maximum improvement rates reached about 25%. It was thought that this strengthening was caused by the formation of α’- martensite phase with quenching after the short-time solution treatment and the precipitation of fine α-phase in the retained β-phase during the short-time aging.
The starting material was mill-annealed Ti–6Al–4V rods of 14mm diameter. The specimens were solution-treated at 1203K for 60 s in air and water-quenched, and aged at 753–953K for 40 s–16.2 ks. After the heat treatments, the test sections were mechanically polished with emery papers (100–2000 mesh) and alumina powders (diameter: 0.03 mm).
Then, the specimens were heat-treated in air under the conditions shown in Figure 1. Hereafter, the solution treatment and quenching is designated ‘‘STQ treatment’’ and the duplex heat treatment consisting of the STQ treatment and aging are called ‘‘STA treatment’’. After the heat treating, the test sections were polished using the method described above.
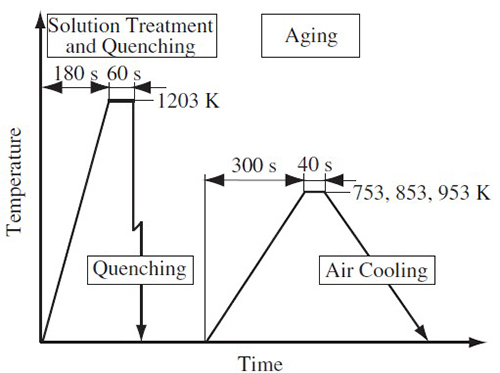
Figure 1: Conditions of heat treatments
Figure 2 shows the change in hardness with the STQ treatment and aging for a wide range of conditions. As shown in the figure, hardness was significantly increased only by the STQ treatment. It is thought that this increase of hardness was mainly due to the formation of α’-phase by quenching. With the subsequent aging for a short time (40 s), hardness was further increased more than the value at the STQ condition except for the aging at 953 K. The time needed to reach the maximum hardness was shortened by elevating the aging temperature and the reduction in hardness began earlier.
Especially, in case of the aging at 953 K, hardness continuously decreased from 40 s without any increase in hardness. Such acceleration of aging with the elevation of temperature probably resulted from the fast decomposition of the α’-phase.
In the above results, it is noteworthy that the hardness of the material aged at 853K for 40 s was about at that obtained by aging at 753 and 803K for a longer time. This result suggests that the aging at 853K can remarkably improve the strength of the alloy in a short time. Hereafter, we focused on the effect of aging for 40 s.
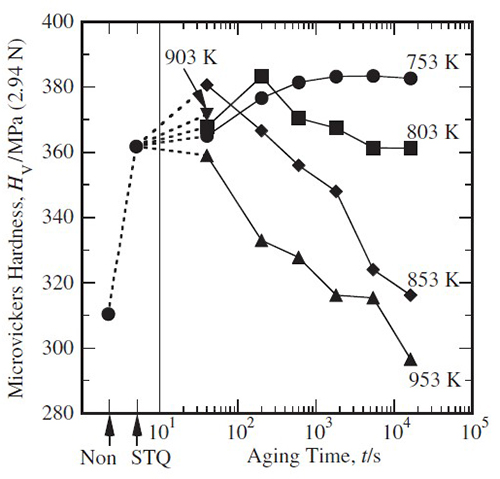
Figure 2: Aging curves