Abstract
Vermicular graphite cast iron (VG iron), also known as compacted graphite iron, represents a unique material category bridging the properties of lamellar and spheroidal graphite cast irons. Characterized by its distinctive worm-like graphite structure, this material offers enhanced mechanical and physical properties compared to traditional gray iron while maintaining beneficial characteristics such as thermal conductivity and damping capacity. This article examines the microstructure, properties, and applications of vermicular graphite cast iron, highlighting its significance in components subjected to both thermal and mechanical stresses.
Historical Development
Cast irons, fundamentally iron-carbon alloys, have evolved significantly from traditional gray cast iron to more sophisticated variants. While gray cast iron, with its flake graphite structure, offers cost-effectiveness and excellent damping capacity, the discovery of spheroidal graphite cast iron (SG iron) in 1947 marked a significant advancement in cast iron technology.
Vermicular graphite cast iron emerged as an accidental discovery during SG iron production. Initially considered a defective form, research by Estes and Scheidewind in 1955 demonstrated its unique advantages, leading to intentional production methods and comprehensive property investigations by numerous researchers.
Microstructural Characteristics
The term "cast iron with vermicular-type graphite (GJV)" derives from the distinctive worm-like appearance of its graphite structure.
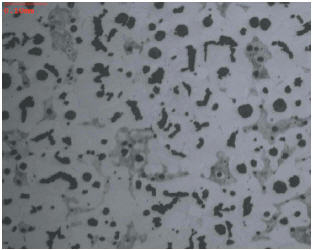
Figure 1: The microstructure of Vermicular graphite iron
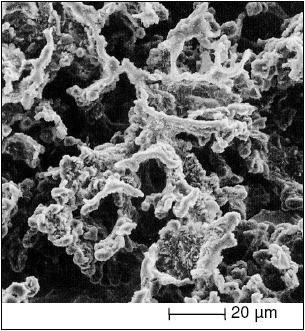
Figure 2: Vermicular graphite under scanning electron microscope
The three-dimensional structure becomes particularly evident under scanning electron microscopy after matrix etching. This graphite formation represents a transitional state between lamellar and spheroidal structures, occurring through controlled or interrupted treatment during the spheroidization process.
Properties and Advantages
Vermicular graphite cast iron, standardized under ISO 16112, exhibits properties intermediate between lamellar and spheroidal graphite cast irons.
Table 1. Material grades and their properties including tensile strength, yield strength, elongation, and thermal properties
Material Grade |
Temp. |
GJV-300 |
GJV-350 |
GJV-400 |
GJV-450 |
GJV-500 |
Tensile strength Rm (N/mm²) |
23°C |
300 - 375 |
350 - 425 |
400 - 475 |
450 - 525 |
500 - 575 |
0.2% yield strength Rp0.2 (N/mm²) |
23°C |
210 - 260 |
245 - 295 |
280 - 330 |
315 - 365 |
350 - 400 |
Elongation to fracture A (%) |
23°C |
2.0 - 5.0 |
1.5 - 4.0 |
1.0 - 3.5 |
1.0 - 3.0 |
1.0 - 2.5 |
Modulus of elasticity (kN/mm²) |
23°C |
130 - 145 |
135 - 150 |
140 - 155 |
145 - 160 |
145 - 160 |
Poisson's ratio |
23°C |
0.26 |
0.26 |
0.26 |
0.26 |
0.26 |
Thermal conductivity (W/m·K) |
23°C |
47 |
43 |
39 |
38 |
36 |
Coefficient of thermal expansion (mm/m·K) |
100°C |
11 |
11 |
11 |
11 |
11 |
Specific heat capacity (J/g·K) |
100°C |
0.475 |
0.475 |
0.475 |
0.475 |
0.475 |
Compared to lamellar graphite iron, VG iron offers:
- Enhanced strength and elongation characteristics
- Superior fracture toughness
- More consistent properties across varying wall thicknesses
Advantages over spheroidal graphite iron include:
- Better thermal properties
- Improved damping capacity
- Superior casting characteristics
Industrial Applications
The material excels in applications combining thermal and mechanical stress requirements. Common applications include:
- Cylinder heads
- Exhaust manifolds
- Brake components
- Automotive transmission components
- Engine units for vehicles