Abstract
Nickel is a key material in modern technologies due to its application versatility, and specific but important properties such as low thermal and electrical conductivities, excellent strength and toughness at elevated temperatures and high resistance to corrosion and oxidation.
Ferro-nickel can be a main alloying agent in stainless steel production and among others a main process of granulation of FeNi is GRANSHOT developed by a group based at Uddeholm in Sweden.
Nickel plays an important role in modern infrastructure and technology. It is used in a wide range of products and various applications because of its superior properties such as low thermal and electrical conductivities, excellent strength and toughness at elevated temperatures and high resistance to corrosion and oxidation.
On the other hand, nickel is a very important metal that finds a place in a variety of applications including consumer products, building, automotive and electronics. There are two kinds of ores containing nickel, namely oxide and sulphide ores. Most nickel produced using oxide ores is from pyrometallurgical processes namely ferronickel smelting or matte smelting.
Ferro-alloys are mainly used as master alloys in the iron, foundry and steel industry, because it is the most economical way to introduce an alloying element into the steel melt.
Ferro-nickel (FeNi) as well as ferro-chrome is the major alloying agent in the production of stainless steel.
Within the steelmaking facilities at Uddeholm in Sweden, a group of engineers pioneered and developed in the early 1970s, the GRANSHOT metal granulation process. They needed to handle excess amounts of pig iron within the daily steel production. They set out to use rugged equipment and water as coolant, being readily available. The result was a process which showed to be a straightforward and a cost effective solution as to produce metal granules with favorable shape and properties for re-use in downstream metallurgical processing.
The news of the metal granulation technology was spread to the ferroalloy producers using the common procedure of sand bed casting (see Figure 1) and crushing, which has poor performance and is labor intensive.
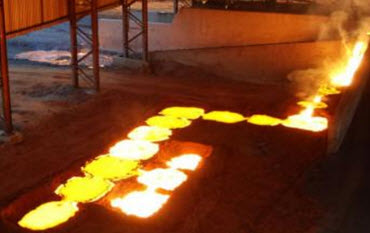
Figure 1: The commonly used casting and crushing process for ferroalloys End-customers were also looking for a better product as to enter into their steel making process. Together they strived for the following objectives:
- Increased productivity and avoiding tedious casting and crushing operations
- Minimize generation of fines and losses of the high cost ferroalloy product
- Create a homogenous and clean ferroalloy product to meet the demand for cleaner steels
- An alloy product easy to handle, transport and feed into metallurgical processes
- Define a repeatable, automated, secure and environmentally friendly process
- Minimize the implementation foot print as to retrofit existing ferroalloy plants
Typically, the casted ferroalloy would pick up impurities when casted. The casting also causes inhomogeneous material analysis and sometimes there would be a mix of material analysis’s during the casting as well as during the crushing and packaging. This could require the supplier or trader to provide a sample analysis of the batch to be delivered, which is both cost and time consuming. The high amount of fines included in the 0-10 mm crushed product, often with a dust-like material, is recycled back into the casting or melting process but the same fines are also produced during transport and handling.
To minimize the casted ferroalloy products, the ferroalloy industry and in particular the ferronickel producers, have adopted the GRANSHOT metal granulation process, from UHT, to produce their end-product to be delivered to customers within the metallurgical industry, Figure 2.
GRANSHOT is an industrial high capacity process, with production rate up to 250 t/hours and in as little as 30 seconds can produce ready-to-use granules that have a size and shape ideal for downstream metallurgical operations in EAF, AOD, foundries, etc.
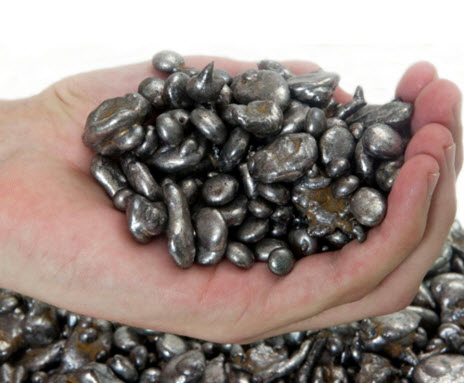
Figure 2: Ferronickel granulated by the GRANSHOT process