Abstract
The twin strip roll process belongs to a new wave of near-net shape processes which allows thin strips of both ferrous and non-ferrous alloys directly from molten metal.
The principle relies on the combination of the casting and hot rolling process into a single step and functions by pouring the hot melt into the gap between two rotating water cooled copper rolls.
In the past decade, the technology of twin-roll casting has been widely investigated for producing thin strips of both ferrous and non-ferrous alloys. The twin-roll caster provides a method for manufacturing continuous thin metal strips directly from molten metal, thus bypassing hot rolling operations and saving considerable energy and capital investment.
The twin roll strip-casting process belongs to a new generation of casting processes, the so called near-net shape processes. The twin roll strip-casting process was first conceived by Henry Bessemer in the middle of the last century.
The "twin-roll" process (thin strips of 0.1±60 mm thickness) produces coilable strip directly from the melt by combining casting and hot rolling into a single step. The principle is based on pouring the melt into the gap between two rotating water-cooling cylindrical copper rolls. The metal solidifies just before reaching the bite of the rolls and is then rolled as it passes through the rolls [5±7]. Amongst other metallurgical aspects typical of this process, the high freezing rate provides an extremely refined solidification microstructure characterized by dendritic ramifications, improves segregation and increases the mechanical properties of metal.
A schematic diagram of the twin-roll process as well as the associated pool aspects is shown in Figure 1. As the "twin-roll" process produces very thin strips, it needs high speeds of production to be competitive with conventional continuous-casting methods. Although this process presents various advantages, it is necessary to develop efficient numerical tools to elucidate the complicated flow and the heat-transfer mechanism, which will be especially useful for designing the optimum "twin-roll" systems.
For the past decade or so, strip casting of steels has been an interesting technical curiosity for the steelmaking community. Many projects and collaborative efforts have been initiated, practically worldwide; however none has been run at a full commercial level for extended periods. With the construction of the Nucor CASTRIP facility at Crawfordsville, the direct casting of sheet products will become a commercial reality.
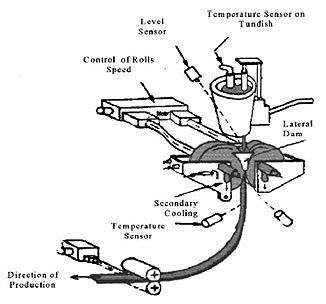
Figure 1: A schematic diagram of the "twin-roll" process, emphasizing pool aspects
Although the concept is extremely simple, its application at a commercially viable production level has proven to be extremely difficult. Several technical advancements have occurred in recent years that have made twin roll casting possible at a commercial level. These include:
- High speed computing and process control
- Advanced ceramics and materials (including copper alloys)
- Sensing technology
- Mathematical modeling of physical phenomena
Table 1 summarized details on the product attributes such as surface quality, dimensional control, mechanical properties and microstructure of typical CASTRIP products and conventional hot rolled product.
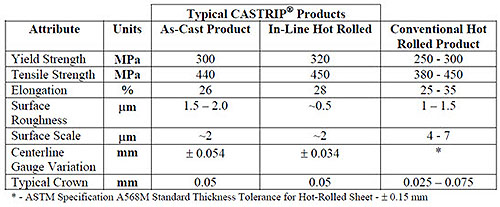
Table 1: Typical CASTRIP Ultra Cast Strip UCS product attributes as compared to conventional material