Abstract
Twist extrusion processes are well used to produce severe plastic deformation and improve grain refinement and control overall material form and subsequent performance aspects.
Non-linear twist extrusion is a relatively new adaptation of the traditional process, which uses varying die geometries to produce even higher and more homogeneous plastic strain evolution in the billet.
Twist extrusion (TE) is a severe plastic deformation (SPD) process. SPD processes use extensive hydrostatic pressure to impose very high strain on bulk solids, producing exceptional grain refinement without introducing any significant change in the overall dimensions of the sample.
The classical TE processes, which is referred to as the linear twist extrusion (LTE) is based on pressing out a prism specimen through a die with a profile consisting of two prismatic regions separated by a twist part. The original cross-section is maintained while it undergoes SPD and the process can be applied repeatedly, which changes in the microstructure and properties of the specimen. High backpressure is applied when it exits the die. A disadvantage of LTE is strain localization at the inlet and outlet of the twisting part. Very high strain is imposed to the billet at both parts while the billet is subjected to rigid body rotation inside the twisting part. This local strain causes high punching force and possibly inhomogeneous strain distribution.
Nonlinear Twist Extrusion (NLTE) is a new severe plastic developed (SPD) method for producing grain refinement by extruding and twisting bulk materials through the channel designed for more effective straining compared with the so-called twist extrusion (TE).
The T. Yalçinkaya, Ü. Şimşek, H. Miyamoto, and M. Yuasa study proposes a new SPD technique called Nonlinear Twist Extrusion (NLTE) to overcome the disadvantages of LTE process. In this work the initial numerical analysis is presented in comparison to classical TE processes, focusing on the advantages which will lead to effective grain refinement. NLTE technique is devised based on TE, but in here an effective die geometry is designed resulting in higher and more homogeneous plastic strain evolution. The shear strain is imposed throughout the whole channel without rigid body rotation. The purpose is to spread the high plastic deformation to the larger regions of the cross-section.
The currently designed channel of NLTE consists of three parts as shown in Figure 1. In part I, the cross-section of the channel changes gradually from a circular of the radius r to elliptical shape with the major and minor axes of a and b, respectively. Since ab = r2, the cross sectional area of the channel is constant through this part. In part II, the bar is twisted according to the parabolic relation q = Cx2. In part III, the twisting continues with a constant rotation angle, but the cross-section changes from elliptical to circular shape again. Note that the change of twisting rate at the sections between the part I and II is smooth so that a rapid increase of shear strain and resulting stress concentration are avoided. Similarly, the billet is extruded out of the die keeping the rotation so that the strain reversal is avoided. In LTE, the shear strain is localized and strain reversal are imposed to the billet, which retard the grain fragmentation. FEM simulations illustrate that a backpressure is necessary for a proper extrusion process resulting in the original cross-section.
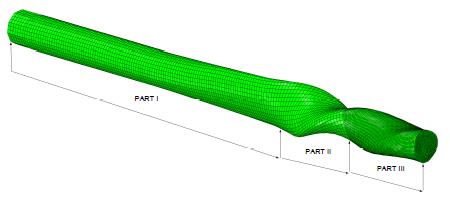
Figure 1: Schematic extrusion of the nonlinear twisting workpiece. Wrought AZ31 alloys were first subjected to a new twist extrusion technique called nonlinear twist extrusion (NLTE) at different conditions. Deformation was achieved at a low temperature of as low as 373 K without fractures on specimen at relatively moderate strain rates. This is due to the die geometry of NTE which is tactically designed to impose plastic strain more effectively and uniformly by minimizing rigid body rotation, localized strain and inhibit strain reversal which retards dislocation accumulation and grain refinement. These aims to overcome the limitations of the conventional twist extrusion (TE). The microstructure and mechanical properties were examined before and after NLTE. In the paper of N. Mupe et al the mechanical properties were investigated by Vickers’s hardness test and tensile test. A survey of the entire literature on SPD of AZ31 reveals that highest hardening is achieved by grain refinement and dislocation accumulation after 1 pass NTE with improved homogenous structure, which results in improved mechanical properties.
The following main observations are made from this study: [1] [4]
• AZ31 was successfully deformed through NLTE for 1 pass at temperatures as low as 373 K without the formation of cracks on specimen surface. Back pressure was not applied. This low temperature deformation is accomplished by uniform deformation of NLTE with less strain localization and rigid body rotation which is seen in the conventional TE.
• Grain refinement improved as the temperatures increased to 373 K, 473 K and 523 K. NLTE was more effective in refining grains compared to the other SPD processes with significant high result of 3.1 μm attained at 523 K. This could be a result of less strain reversal, but more detailed examination is required in the future.
• The higher hardness is a result of grain refinement, twinning and strain hardening which occur at lower deformation temperature. The hardness was significantly increased to 104 HV at 473 K.
• NLTE was confirmed to be a promising technique for processing AZ31 alloys resulting to significant improvement of materials mechanical properties.