Abstract
Medium manganese steels represent a breakthrough third-generation advanced high-strength steel (AHSS) technology that addresses the limitations of previous generations while maintaining exceptional mechanical properties. These steels, containing 4-12 wt% manganese, exhibit transformation-induced plasticity (TRIP) or twinning-induced plasticity (TWIP) mechanisms depending on retained austenite stability. By utilizing intercritical annealing temperatures, engineers can control austenite phase stability and optimize deformation behavior. Medium-Mn steels offer superior strength-ductility combinations with reduced production costs compared to second-generation AHSS, making them ideal for automotive applications focused on carbon emission reduction. The microstructure typically consists of fine-grained austenite phases in a ferritic matrix, with average grain sizes around 0.45μm, providing excellent mechanical performance for lightweight automotive components.
Introduction to Medium Manganese Steel Technology
Medium manganese steels deserve recognition alongside other technologically advanced materials in the automotive industry, including advanced high-strength steels (AHSS), dual-phase (DP) steels, complex-phase (CP) steels, and second-generation steels. These innovative materials demonstrate exceptional potential for transformation-induced plasticity (TRIP) or twinning-induced plasticity (TWIP), with their behavior determined by the stability of retained austenite phases.
Evolution of Advanced High-Strength Steels
First-Generation AHSS Development
The development of first-generation advanced high-strength steels focused on creating and modifying additional strengthening phases within ferritic microstructures. This approach led to the successful development of dual-phase (DP) steels, complex-phase (CP) steels, conventional transformation-induced plasticity (TRIP) steels, and martensitic steels. While these materials achieved significant strength improvements, their ductility remained limited.
Second-Generation AHSS Challenges
Since the 2000s, intensive research has focused on second-generation AHSS, primarily high-manganese steels with austenitic single-phase microstructures. These materials utilize various deformation mechanisms including dislocation slipping (SLIP), transformation-induced plasticity (TRIP), twinning-induced plasticity (TWIP), and microband-induced plasticity (MBIP). Second-generation AHSS achieve remarkable ductility with total elongation up to 60% and ultimate tensile strength reaching 1100 MPa.
However, the high alloying content in second-generation AHSS has created significant production challenges and increased costs. These issues include Al₂O₃ formation during casting processes, severe macrosegregation and microsegregation due to high carbon and manganese content, and complications with hot-dip galvanization caused by Al₂O₃ and MnO surface layer formation during continuous annealing.
Medium Manganese Steels: Third-Generation Innovation
Automotive Industry Drivers
The automotive industry's commitment to reducing vehicle carbon emissions has driven the development of third-generation advanced high-strength steels, specifically "Medium-Mn" steels. These materials successfully bridge the gap between first and second-generation AHSS by offering exceptional mechanical properties while addressing production cost concerns.
Deformation Mechanisms in Medium-Mn Steels
Medium-Mn steels demonstrate remarkable versatility in their deformation behavior, capable of exhibiting either transformation-induced plasticity (TRIP) or twinning-induced plasticity (TWIP) depending on retained austenite stability. Engineers can control this behavior by varying the annealing temperature within the intercritical ferrite+austenite region, allowing precise tuning of austenite phase stability and its susceptibility to either TRIP or TWIP mechanisms.
Microstructural Simulation and Mechanical Property Prediction
While computational methods can effectively simulate the expected microstructure for specific compositions and thermal treatment schedules, accurately predicting mechanical properties remains challenging due to highly localized stresses and strains occurring during TRIP and TWIP processes. Understanding the kinetics of the TRIP phenomenon as a function of strain becomes crucial for proper mechanical behavior simulation and for correlating TRIP behavior to austenite stability through stacking fault energy (SFE) analysis.
Microstructural Characteristics
Grain Structure and Morphology
The microstructure of medium manganese steel annealed at low temperature reveals distinctive characteristics, as illustrated in Figure 1. The phase in relief represents austenite, with an average grain size of approximately 0.45μm. This fine-grained structure contributes significantly to the material's exceptional mechanical properties.
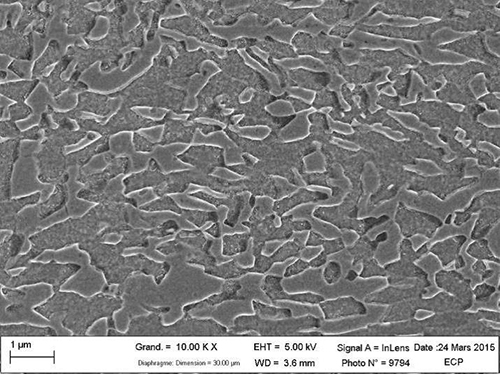
Figure 1: Microstructure of medium manganese steel annealed at low temperature after a 1% Nital etch
Phase Distribution Analysis
The microstructure consists of austenite phases distributed within a ferrite matrix. However, the exact morphology requires further investigation to determine whether the structure comprises austenite "islands" completely surrounded by ferrite or if the two phases are intertwined. Advanced characterization techniques, including progressive focused ion beam (FIB) erosions and electron backscatter diffraction (EBSD) analyses, will provide detailed information about phase distributions and crystallographic orientations.
Chemical Composition and Alloying Elements
Primary Alloying Elements
Medium-Mn steels contain four main alloying elements: manganese, carbon, aluminum, and silicon. Manganese and carbon function as strong austenite stabilizers, playing crucial roles in determining the material's final properties and behavior.
Carbon Content Considerations
The carbon content in medium-Mn steels typically ranges from 0.05 to 0.4 wt%. While carbon effectively stabilizes austenite, higher carbon contents can lead to cementite precipitation, potentially creating cementite networks that cause intergranular fracture along austenite boundaries. Additionally, elevated carbon content negatively affects steel weldability, as martensite formation may occur during cooling after welding operations.
Manganese: The Critical Alloying Element
Manganese serves as the most important alloying element in medium-Mn steels, effectively stabilizing the austenite phase. These steels typically contain 4-12 wt% manganese, providing several beneficial effects. Manganese addition lowers the A₁ temperature and increases the process window while enhancing hardenability and significantly reducing the critical cooling rate. However, manganese addition may also compromise steel weldability, and the manganese concentration critically controls the deformation mechanisms.
Manganese Content and Deformation Behavior
Research has demonstrated that medium-Mn steels with manganese content below 9 wt% exhibit deformation-induced α'-martensite phase transformation, classified as medium-Mn TRIP steels. Conversely, medium-Mn steels with higher manganese content demonstrate different deformation characteristics, as illustrated in the steel classification system.
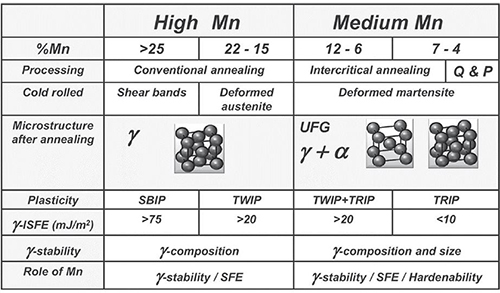
Figure 2: Classification of the types of steels with enhanced manganese content
Conclusion
Medium manganese steels represent a significant advancement in advanced high-strength steel technology, offering an optimal balance between mechanical properties, production feasibility, and cost-effectiveness. Their unique ability to exhibit controlled TRIP or TWIP behavior through precise thermal processing makes them ideal candidates for automotive applications requiring exceptional strength-ductility combinations while supporting carbon emission reduction goals.