Abstract
This technical article examines the patenting process for high carbon steel wire and explores steel hardenability principles. The discussion covers the patenting heat treatment process, which involves heating wire to approximately 970°C and subsequent controlled cooling to achieve optimal microstructure. The article also analyzes hardenability factors, including mass effect, quenching methods, and the influence of alloying elements. Special attention is given to testing methods, particularly the Jominy end quench test, and their practical applications in determining steel properties.
Introduction to Wire Patenting
Wire ropes for haulage applications typically utilize carbon steel containing 0.35-0.5% carbon. These materials undergo patenting, a specialized heat treatment process, before drawing. The process involves passing wire through furnace tubes at approximately 970°C, producing uniform austenite with relatively large grain size. Rapid cooling in air or molten lead results in fine pearlite formation without primary ferrite separation.
Patenting Process Characteristics
While the large crystal structure might suggest brittleness in the heat-treated condition, this effect diminishes after several drawing passes. The process enables area reductions up to 90%, superior to tempered martensite alternatives. This exceptional drawing capability stems from reduced ferrite cells and aligned cementite fibers.
Hardenability Principles and Mass Effect
Fundamental Concepts
Hardenability measures steel's depth-hardening capability during quenching. Maximum hardness primarily depends on carbon content, while hardenability is influenced by:
- Quenching medium and methodology
- Steel composition and manufacturing process
- Section size
Table 1: Effect of mass on the properties of carbon steel
Dia. of bar, mm |
Tensile Strength Rm, MPa |
Elongation, A, % |
Izod, J |
Water quenched from 870oC and not tempered |
17 |
1853 |
3 |
4 |
29 |
1035 |
8 |
18 |
76 |
803 |
15 |
32 |
Tempered at 600oC |
17 |
850 |
18 |
103 |
76 |
741 |
25 |
59 |
Mass Effect Analysis and Effects of Alloying
The mass effect phenomenon results from progressively slower cooling from surface to center, due to steel's low thermal conductivity. The ruling section concept defines thickness limits for achieving specified mechanical properties.
Alloying elements play crucial roles in achieving fully hardened structures in large sections. For example, adding 3% nickel and 1% chromium significantly retards austenite transformation.
Table 2: Effect of mass on the properties of alloy steel
Dia of bar, mm |
Tensile Strength Rm, MPa |
Elongation, A, % |
Izod, J |
Oil quenched from 820°C, tempered at 600°C |
17 |
958 |
24 |
85 |
76 |
927 |
22 |
82 |
Testing and Measurement
Jominy End Quench Test
The test (BS 4437) utilizes a standardized procedure involving:
- 25mm diameter bar, 100mm length
- Normal hardening temperature
- Controlled water jet quenching
- Systematic hardness measurements
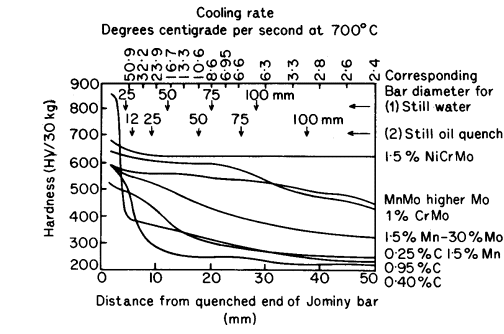
Figure 1: Hardness distance curves for end quench test samples
From Figure 1, the effectiveness of a given quench on various steels can be judged; for example, bars of 1.5% Ni Cr Mo steel up to 100 mm dia can be satisfactorily hardened in oil, whereas for the plain 0.95% carbon steel the maximum diameter of the fully hardened bar will be less than 12.5 mm for the same quench.
The Jominy end quench test is not only a very reproducible test, but is also an excellent laboratory test for classifying steels in order of merit as regards hardenability and it gives a very useful first approximation to the merits of a given steel. As to whether a steel with a particular hardenability will give the satisfactory mechanical properties in a particular section must be decided by trial.
Hardenability Specifications
Hardenability variations between different casts and within single ingots necessitate band-based specifications rather than simple curves.
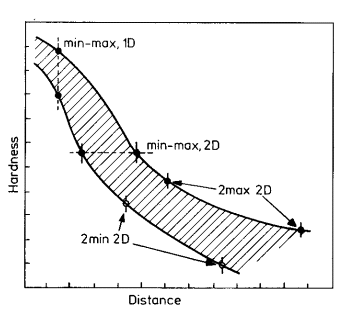
Figure 2: Hardenability limit designations
The hardenability of different casts of steel with the same chemical composition can vary significantly. Similarly, substantial variations in hardenability may also occur in samples taken from different parts of the same ingot. Consequently, Jominy results are represented as bands rather than simple curves.
To specify hardenability, BS 4437 uses two points, as illustrated in Figure 2 and described below:
- Desired hardness at two distances
- Minimum/maximum hardness at specific distance
- Two maximum hardness values at different distances
- Minimum hardness at two distances
- Any minimum and maximum hardness combination