Abstract
Aluminum dross, a significant byproduct of aluminum melting processes, consists of aluminum, aluminum oxides, and various compounds of alloying elements. This comprehensive review examines dross formation mechanisms, composition variations, and processing parameters that influence its properties. The article explores modern processing techniques, including rapid quenching and mechanical beneficiation, highlighting the industrial applications of processed dross in steel manufacturing and other sectors. Understanding dross processing is crucial for optimizing aluminum production efficiency and promoting sustainable materials management in metallurgical industries.
Introduction
Aluminum dross emerges as an inevitable byproduct during aluminum melting processes. Its composition and properties vary significantly depending on multiple factors, including scrap type, alloy treatment, and melting equipment specifications. The material primarily consists of aluminum, aluminum oxide, and oxides of alloying elements, with occasional presence of halogenide, carbide, or nitride compounds.
Dross Formation and Characteristics
A notable characteristic of dross is its substantial metallic aluminum content, which becomes mechanically fixed within an aluminum oxide cellular structure. This structure exhibits remarkable tension strength, capable of bonding aluminum at twenty times its weight. The presence of finely dispersed gas bubbles creates a foam-like structure, facilitating natural separation from the aluminum melt due to density differences.
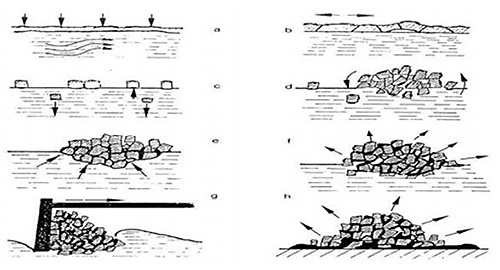
Figure 1: Formation of Dross - Detailed illustration showing the eight-step process of dross formation from surface oxidation to cooling, with the following meaning for each step:
- Surface oxidation of melt
- Crushing of oxidic skin by bath movement
- Sinking and floating of oxidic particles
- Conglomeration of oxidic particles
- Interspace filling up by metallic aluminum
- Inside oxidation of dispersed aluminum
- Skimming of dross from melt bath surface
- Metallic aluminum drip off and follow-up oxidation of solids during dross cooling
Table 1: Composition of dross
Composition of dross |
Type of Dross |
Metallic Al, [%] |
Residual compounds |
Untreated Dross |
< 80% |
Al₂O₃, Al₂O₃*MgO |
Flatcake & Crumbs |
90 – 70% |
Al₂O₃*SiO₂, Al₂O₃*FeO, etc. |
Concentrate |
70 – 50% |
Al₂O₃, AlCl₃, NaCl, KCl |
Coarse Residue |
50 – 20% |
CaF₂, NaF, AlF₃, etc. |
Fine Residue |
20 – 5% |
Al₂O₃, AlN, Al₄C₃, Al₂S₃, AlP, etc. |
Critical Process Parameters
Several key factors influence dross formation and properties:
- Surface-to-volume ratio of the scrap material
- Nature and quantity of impurities (organic and inorganic)
- Melting conditions and equipment specifications
- Melt composition, particularly regarding Mg, Na, Li, and Ca content
- Refining procedures
- Dross removal techniques and temperature conditions
- Cooling parameters post-removal
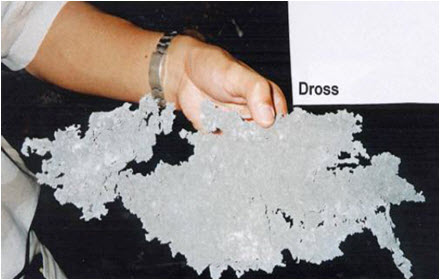
Figure 2: Visual representation of processed aluminum dross