Abstract
Ring rolling is an advanced metal forming process used to manufacture seamless rings with precise dimensions and superior mechanical properties. This process can be performed at both high and ambient temperatures, making it highly versatile. The technique is particularly valuable in producing components for railway, automotive, and aerospace applications, offering advantages such as uniform quality, close tolerances, and improved grain structure. This article explores the fundamental principles, process steps, and industrial applications of ring rolling, highlighting its significance in modern manufacturing.
Introduction
Ring rolling is a continuous metal forming process that employs rotating rolls to reduce material thickness while increasing length, maintaining minimal width variation. The process involves applying high pressures to achieve plastic deformation, resulting in the desired cross-sectional shape. This versatile technique can be performed either as a hot or cold-forming process, depending on the application requirements.
Process Equipment and Mechanics
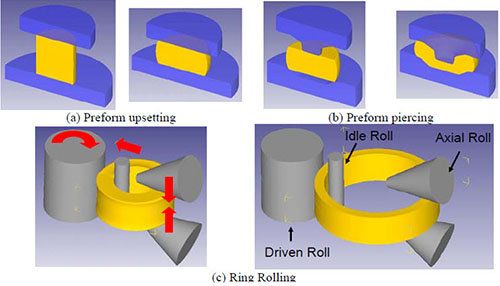
Figure 1: Main characteristic of ring rolling
The equipment used in ring rolling shares similarities with traditional rolling mills used in plate production. However, ring rolling distinctively employs rolls of different diameters and geometries. The process begins with a forged bar that undergoes upsetting and piercing operations to create a hollow circular preform. This preform is then processed between driven and idle rolls, while axial rolls apply pressure parallel to the ring axis.
Applications and Advantages
Ring rolling finds extensive applications in manufacturing:
- Railway wheel tyres
- Anti-friction bearing races
- Automotive components
- Aerospace parts
- Power generation equipment
- Large cylindrical vessels
The process offers several key advantages:
- Reduced production time
- Consistent product quality
- Precise dimensional tolerances
- Material cost savings
- Enhanced mechanical properties through optimized grain structure
Process Parameters and Control A significant advantage of ring-rolled components is their superior mechanical properties, particularly in the worked surface areas. The process creates an optimized grain size and orientation, resulting in enhanced structural integrity compared to alternative manufacturing methods.
The complexity of ring rolling necessitates careful control of multiple process parameters. The interaction between driven rolls, idle rolls, and axial rolls requires precise coordination to achieve desired outcomes. This complexity makes parameter selection a critical aspect of the manufacturing process.
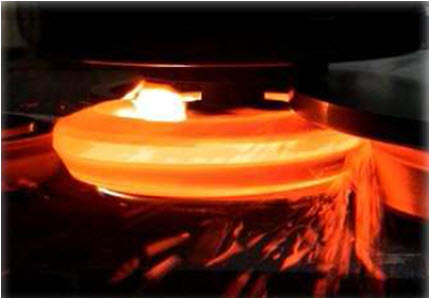
Figure 2: Ring rolling process