Abstract
Welding of titanium can be relatively complex since at high temperatures the material can be very reactive and depending on the inclusion of impurities, they can also have a negative effect on overall weld integrity.
Key advantages of PAW compared to TIG include, lower heat inputs, high welding speeds and high metallurgical quality levels.
For successful welding of titanium, some factors need to be considered. Titanium is extremely reactive in temperatures exceeding 500-650°C. It reacts with elements in impurities or air such as C, O, N, and H. These elements strengthen titanium but small amounts also impair ductility and toughness of titanium joints. The effects of the heating and cooling cycles involved in welding processes on the mechanical properties of the alloys and the specific alloy composition also need to be considered.
Titanium alloys are readily joined with several common fusion welding processes such as tungsten inert gas welding (TIG), plasma arc welding (PAW), electron beam welding (EBW), and laser beam welding (EBW). Fusion welding processes can be characterized generally by the heat-source intensity.
The most common welding techniques to joint titanium and its alloys are Gas Metal Arc Welding (GMAW), such as Metal Inert Gas (MIG); Plasma Arc Welding (PAW); Laser Beam Welding (LBW); and Electron Beam Welding (EBW). The first three methods fall in the arc welding category with high heat input and low power density of heat source, while the last two techniques belong to the high-energy beam group.
Plasma arc welding (PAW) is an arc welding process which uses a constricted arc between a non-consumable electrode and the workpiece (transferred arc mode) or between the electrode and the nozzle (non-transferred arc mode). Two separate gas flows are used in PAW; plasma gas which flows through the orifice and becomes ionized and shielding gas which flows through the outer nozzle. Usually these gases are the same. Helium, argon and their mixtures are used as shielding gases. Hydrogen and nitrogen may also be added in the mixture. PAW is essentially an extension of the TIG welding process and the differences between the processes are illustrated in Figure 1. TIG uses an open arc while in PAW, the electrode and arc are surrounded by a gas chamber. The plasma gas in the orifice gets heated and ionized which creates a narrow, constricted arc that provides excellent directional control and produces a very favorable depth-to width weld profile.
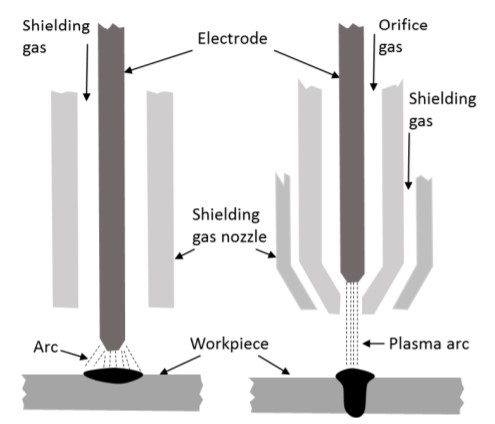
Figure 1: The plasma arc is confined in PAW which makes it straighter and more concentrated PAW can be used in two distinct operating modes, the melt-in mode and the keyhole mode. At lower arc currents, the process resembles TIG and produces a similar weld pool. This melt-in mode is used for material thicknesses below 3 mm. At higher arc currents and plasma gas flow rate, the plasma column can displace the molten metal and form a keyhole. Keyhole mode welding is used for single pass butt welds on material thicknesses from 2.4 mm to 8 mm. Compared to laser welding and electron beam welding, keyhole PAW is more cost effective and more tolerant of joint preparation, though its energy is less dense and its keyhole is wider.
The advantages of PAW compared to TIG include:
• High welding speed: up to 5 times higher than conventional TIG
• Reliable arc ignition and concentrated stable arc with little sensitivity to arc length variation
• Lower heat input leading to smaller heat affected zone and little distortion
• Ability to perform keyhole welding and melt-in-mode welding with the same equipment
• Possibility to weld very thin materials (0.1 mm) and thick materials (8 mm) with a single pass without filler material
• High metallurgical quality in comparison to conventional TIG.
PAW can be used to weld the same materials as TIG. Keyhole plasma welding is extensively used to weld stainless steel pipes and tanks. In aerospace industry, PAW is used for airframe components, fuel vessels and gas turbine components. The greater capital cost and complexity of PAW equipment are why PAW has not become more common.