Abstract
Weight savings, good mechanical properties, corrosion resistance are key factors in making magnesium-zirconium alloys a preferred structural material choice in automotive and aerospace applications.
Zirconium is particularly useful for influencing grain size control for which magnesium alloys without this inclusion have a tendency to display characteristic grain growth.
Magnesium alloys are an important structural material in aerospace and car industries, as well as in some other areas. Their main characteristics are small specific weight, good mechanical properties, good processing and resistance to corrosion.
Generally, Mg alloys contain one or two primary alloying elements. The Mg alloys are mainly based on three binary systems: Mg-Al, Mg-Zn and Mg-Zr.
The magnesium alloys without zirconium show a strong tendency for grain growth. Non-alloy magnesium can undergo cold deformation up to 5-10%. Addition 0.5wt%Zr yields a grain size refinement, which makes a cold deformation up to 30% possible. Above 220°C, hot deformation is possible, with certain preference of extrusion above rolling. The compression of the cross-section during extrusion limits the risk of crack formation. The temperature of hot deformation is generally chosen below 400°C in order to limit oxidation and to prevent excessive grain growth of the alloys without zirconium.
Zirconium however, is one of the primary candidates of alloying element with Mg for the development of biodegradable Mg alloys. More importantly Zr is an effective alloying element to improve both the strength and the corrosion resistance of Mg alloys. Grain size control is very important for Mg alloys.
It is well known that Zr additions to pure magnesium or appropriate alloys reduces the grain size by an order of magnitude or more, compared to non-Zr containing alloys, with consequent beneficial effects on mechanical properties and casting characteristics. However, Mg alloys with Zr are more expensive than the alloys without Zr, which is why for consumer products mainly Zr free alloys are used.
Figure 1 presents the Mg-rich corner of the phase diagram Mg-Zr. The solubility of Zr in liquid Mg is very small. The binary Mg-Zr alloys do not have sufficient strength for engineering applications. An amount of only 0.5% Zr added to the melt is already sufficient for grain refinement. In the alloys with Zr, hydrogen, aluminum and manganese should be avoided in view of the development of undesired chemical compounds. The addition of rare earth elements and thorium in combination with Zr or Mn improves the high temperature strength.
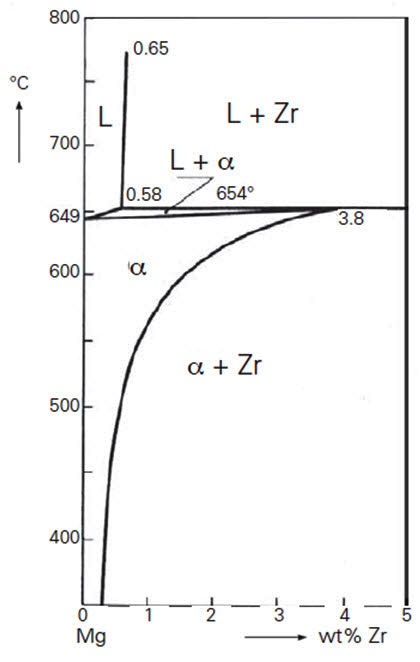
Figure 1: The binary phase diagram Mg-Zr