Abstract
Boriding (boronizing) is a thermochemical surface hardening process that significantly enhances material properties by diffusing boron into the substrate surface. This process, conducted at temperatures between 700-1000°C for 1-12 hours, can be applied using solid powders, pastes, liquids, or gaseous mediums. The treatment produces extremely hard surfaces (1450-5000 HV) with excellent wear resistance and reduced friction coefficients. While offering superior hardness retention at elevated temperatures and enhanced corrosion resistance compared to other surface treatments, boriding does present challenges including labor-intensive application and dimensional changes that require precise engineering consideration.
Introduction to Boriding Technology
Boriding, also known as boronizing, is an advanced thermochemical surface hardening process applicable to a wide range of materials including ferrous, nonferrous, and cermet substrates. The process involves heating thoroughly cleaned materials to temperatures between 700 and 1000°C for periods typically ranging from 1 to 12 hours. During treatment, materials are exposed to boronaceous media that may be in solid powder form (boronizing compound), paste, liquid, or gaseous state. Recent technological developments have expanded processing options to include specialized techniques such as plasma boriding, fluidized bed boriding, and multicomponent boriding approaches.
Compatible Materials and Limitations
Most ferrous materials are suitable candidates for industrial boriding processes, including:
- Structural steels
- Case hardened steels
- Tempered and tool steels
- Stainless steels
- Cast steels
- Commercially pure iron (Armco iron)
- Gray and ductile cast irons
- Sintered iron and steel products
However, certain materials are not recommended for boriding treatment. Aluminum and silicon-bearing steels typically yield unsatisfactory results. Water-hardening steel grades are generally avoided due to the boride layer's susceptibility to thermal shock. Similarly, resulfurized and leaded steels present risks of case spalling and cracking, making them unsuitable for this treatment.
Since boriding occurs in the austenitic temperature range, air-hardening steels can undergo simultaneous hardening and boriding, offering processing efficiency advantages.
Boriding Process Mechanisms and Kinetics
The boriding process progresses through two distinct reaction phases. Initially, interaction between the boron-yielding substance and the component surface creates nucleation sites, with the rate dependent on both time and temperature. This initial reaction forms a thin, compact boride layer. Subsequently, a diffusion-controlled reaction occurs, determining the ultimate layer thickness.
The total thickness of the boride layer growth at a specific temperature can be calculated using the formula:
d = k t
Where:
- d represents the boride layer thickness in centimeters
- k is a temperature-dependent constant
- t is the time in seconds at the given temperature
The diffusivity of boron at 950°C is 1.82x10–8 cm²/s within the boride layer and 1.53x10–7 cm²/s in the diffusion zone. Consequently, the boron-containing diffusion zone extends more than seven times deeper than the visible boride layer thickness into the substrate. This diffusion is driven by concentration gradients within the material.
Typical diffusion case thicknesses for ferrous alloys range up to approximately 0.13 mm, varying with alloy composition and part configuration. High-carbon and high-alloy tool steels generally require thinner case depths, while low or medium-carbon steels may benefit from deeper case formation. When case depth reaches approximately 320 to 350 µm, subsequent heat treatment is typically unnecessary.
Research on Boriding Kinetics
Research by A. Milinović et al. investigated the kinetics of boride layer formation on C15 and C70W2 carbon steels. Their study examined pack boronizing conducted at temperatures from 870°C to 970°C with durations of 4 to 8 hours. Results showed average boride layer thicknesses ranging from 69.9 to 239.2 μm for C15 steel and from 60.6 to 181.2 μm for C70W2 steel.
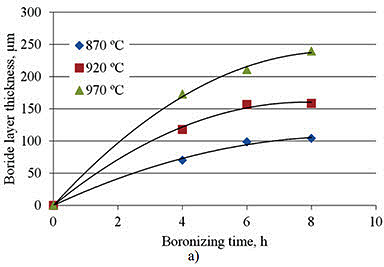
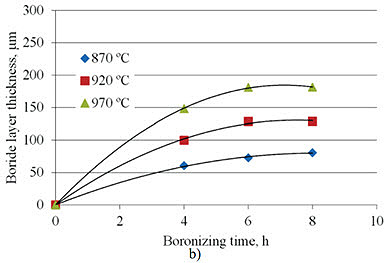
Figure 1: Boride layer thicknesses as a function of boronizing time a) C15 steel, b) C70W2 steel
Advantages of Boriding Treatment
Boriding offers numerous technical advantages that make it an attractive surface treatment option for specific applications:
The boride layers produced exhibit extremely high hardness values, ranging from 1450 to 5000 HV, coupled with high melting points of the constituent phases. This hardness significantly exceeds that achievable through conventional surface hardening treatments applied to carbon steels.
The combination of exceptional surface hardness and reduced friction coefficient provides outstanding resistance against major wear mechanisms including adhesion, tribooxidation, abrasion, and surface fatigue. This property allows manufacturers to substitute easier-to-machine base steels while still achieving superior wear resistance and anti-galling properties.
Unlike some other treatments, the hardness of boride layers can be maintained at elevated temperatures, outperforming nitrided cases in high-temperature applications.
Boriding significantly enhances corrosion-erosion resistance of ferrous materials when exposed to non-oxidizing dilute acids and alkali media, expanding its industrial applications.
Treated surfaces demonstrate moderate oxidation resistance (up to 850°C) and substantial resistance to attack by molten metals.
Components with borided surfaces typically experience increased fatigue life and improved service performance when operating in oxidizing and corrosive environments.
Limitations and Considerations
Despite its advantages, boriding presents several challenges that must be considered:
The process tends to be relatively inflexible and labor-intensive compared to other thermochemical surface hardening treatments such as gas carburizing and plasma nitriding. These factors can make boriding less cost-effective, particularly in regions with high labor costs. Therefore, boriding is best suited for engineering components requiring exceptional hardness and wear/corrosion resistance, or in manufacturing environments with competitive labor costs.
Dimensional changes must be carefully considered when boriding precision components. The process typically produces growth (volume increase) of 5 to 25% of the layer thickness. For example, a 25 μm layer would result in dimensional growth of 1.25 to 6.25 μm. While this growth is predictable for specific material and treatment combinations, precision parts requiring minimal stock removal must account for approximately 20-25% dimensional increase relative to the final boride layer thickness.
Tolerance refinement presents challenges, as partial removal of the boride layer can only be accomplished through diamond lapping. Conventional grinding processes typically cause fracturing of the layer. Consequently, precise boriding applications are generally limited to components with substantial cross-sectional areas.
The effect on fatigue properties must be considered. Boriding most steels provides minimal improvement in bending fatigue endurance limits, though some enhancement in corrosion-fatigue strength has been observed. The rolling contact fatigue properties of borided alloy steel components generally underperform compared to carburized and nitrided steels when subjected to high contact loads (2000 N). This limitation restricts boriding applications for gears primarily to screw designs where transverse loading of gear teeth is minimized.
Post-boriding heat treatment requirements can add complexity to the manufacturing process. Tools often require hardening and tempering after boriding, necessitating vacuum or inert atmosphere processing to maintain the boride layer's integrity.