Abstract
Nitrocarburizing is a thermochemical surface treatment process applied to ferrous materials to enhance surface properties through nitrogen and carbon enrichment. This process creates a compound layer that significantly improves wear resistance, corrosion resistance, and fatigue strength of steel components. The treatment involves controlled atmospheric conditions with specific gas compositions including ammonia, carbon dioxide, nitrogen, and hydrogen. Conducted at temperatures between 560-580°C, nitrocarburizing extends component service life while maintaining minimal distortion. This surface hardening technique is widely utilized in manufacturing machine components and tools, making it invaluable for industrial applications requiring enhanced surface performance.
Introduction to Nitrocarburizing Technology
Nitrocarburizing represents a sophisticated thermochemical treatment process specifically designed for ferrous materials. This surface enhancement technique produces controlled enrichment of nitrogen and carbon at the material surface, resulting in the formation of a protective compound layer. The fundamental principle behind nitrocarburizing lies in the diffusion of these elements into the steel substrate, creating a hardened surface zone that dramatically improves component performance.
The success of any nitrocarburizing operation depends critically on precise control of the furnace atmosphere composition and function. This atmospheric control directly influences the quality and characteristics of the final treated surface, making it essential for achieving optimal hardening and thermochemical treatment results.
Process Objectives and Surface Enhancement Benefits
The primary purpose of nitrocarburizing centers on improving three critical material properties: wear resistance, corrosion resistance, and fatigue resistance of constructional steel parts. These significant improvements become apparent when examining the surface microstructure and hardness profiles achieved after treatment.
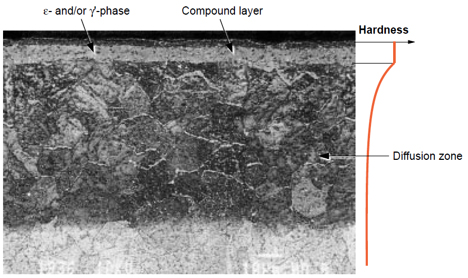
Figure 1: Micrograph demonstrating both the compound layer and the underlying diffusion zone (darker region) in a nitrocarburized 5% Cr tool steel (2h/580°C)
In the figure above, the compound layer consists of only ε-phase with a thin, outer, porous zone. The enhanced surface properties result from the formation of distinct metallurgical zones. The compound layer provides exceptional wear resistance and corrosion protection, while the underlying diffusion zone contributes to improved fatigue strength and load-bearing capacity
Nitrocarburizing Process Steps and Temperature Control
The nitrocarburizing process comprises three fundamental steps: initial heating, diffusion at the nitrocarburizing temperature, and controlled cooling. Additional optional steps include pre-heating to accelerate the nitrocarburizing kinetics and post-oxidation treatment to further enhance corrosion resistance properties.
Ferritic nitrocarburizing in gaseous atmospheres typically operates within a temperature range of 560 to 580°C. This temperature window provides optimal conditions for nitrogen and carbon diffusion while maintaining dimensional stability and minimizing component distortion.
Atmospheric Composition and Gas Control Systems
The atmospheric composition represents the most critical parameter in gaseous nitrocarburizing operations and requires precise monitoring and control throughout the process cycle. The treatment atmosphere consists of four primary gases: nitrogen (N₂), ammonia (NH₃), carbon dioxide (CO₂), and hydrogen (H₂).
Ammonia serves as the primary nitrogen source, decomposing at treatment temperature to release active nitrogen for surface diffusion. Carbon dioxide decomposes into carbon monoxide, which works in conjunction with hydrogen to facilitate carbon transfer to the steel surface. In some applications, carbon monoxide may be introduced directly instead of carbon dioxide to achieve more precise carbon potential control.
Hydrogen production occurs naturally through ammonia decomposition, though additional hydrogen may be introduced when required. Nitrogen serves multiple functions: controlling the percentage of reactive gases, diluting the atmosphere for safety, and purging the furnace system before and after treatment to prevent explosive ammonia-oxygen mixtures.
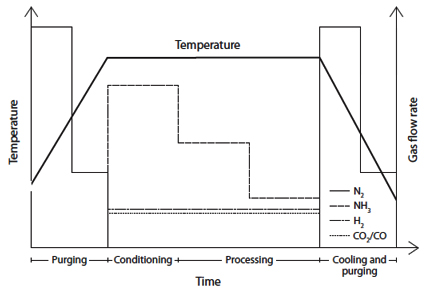
Figure 2: Gas ratio per process step - showing the flow rate variations of different gases throughout each phase of the nitrocarburizing cycle
The precise control of gas flow rates and ratios throughout different process steps ensures consistent treatment results and optimal surface layer formation.
Industrial Applications and Manufacturing Benefits
Nitrocarburizing finds extensive application in the manufacturing of machine components and precision tools. This widespread adoption stems from the process's ability to achieve improved surface hardness, enhanced fatigue strength, and superior corrosion resistance at elevated temperatures while maintaining exceptional dimensional stability with minimal distortion.
The treatment significantly extends component service life by creating a durable surface layer that resists wear, corrosion, and fatigue failure. Even corrosion non-resistant steel grades benefit substantially from nitrocarburizing, gaining enhanced corrosion resistance through the formation of the protective compound zone.
The combination of improved mechanical properties and minimal dimensional changes makes nitrocarburizing particularly valuable for precision components where tight tolerances must be maintained. This characteristic eliminates the need for extensive post-treatment machining, reducing manufacturing costs and production time.