Abstract
Zn–Mg alloys present a number of options to help solve issues of finding suitable biocompatible materials that can be safely and effectively used in the medical industry.
This article covers a deeper look into Mg-Zn alloys with high mechanical strength, and corrosion resistance for implant applications.
Zn–Mg alloys have attracted extensive attention over the past few decades as the anticorrosion coatings for steels and a biodegradable material that are used in the human body. Zn–Mg alloy belongs to light metal system. Over the last decade, Zn–Mg coatings with Mg contents lower than 10 wt.% were found to have much improved corrosion properties compared with pure Zn coating and may be developed and applied for the next generation of galvanized steels.
Having superior mechanical properties as compared to polymers, metals could provide a more ideal platform as interim implants if their biocompatibility is close to or better than biodegradable polymers.
The objective of L. F. Guleryuz, R. Ipek, I. Arıtman, S. Karaoglu study was to develop Mg-Zn alloys with high mechanical strength, and corrosion resistance for implant applications. Zn Mg alloy has been processed by Mechanical Alloying method. Hot sintering was conducted at 410°C under argon atmosphere.
For preparation of the Zn-Mg alloy samples atomised Mg and Zn powders with avarage grain sizes of about 63 μm and purity 99% were utilized in this study. A mixture of Zn and Mg powder was prepared with 20 wt % magnesium content and with 80 wt % zinc content respectively, with the help of a V-blender by mixing it for 1 h On the other hand for compare the same persantage Zn-Mg alloy were mechanically alloyed The powders were planetary ball milled using 10 mm-diameter stainless steel balls with weight ratio of 10:1 and rotate speed of 250 r/min for 8 h during mechanical milling. Then, high-strenght graphite die with 10 mm in inner diameter and 60 mm in height was using for samples sintering process. The ball milled powders were put into graphite die and hot press sintered under pressure of 30 MPa in argon atmosphere. It consists in heating the sample up to 410°C at a rate of 50°C/min and holding at this temperature for 30 minutes. The purpose of this first step is to homogenize the material.
Result of microstructures densities by EDS (Energy dispersive Spectrograph) and hardness test behaviors of the Zn-based alloys are presented in Figures 1 -2.
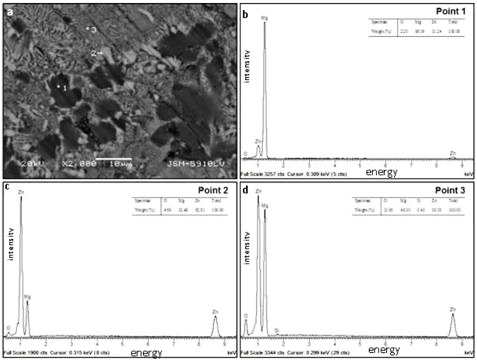
Figure 1: Sample energy dispersive spectrograph Figure 1b presents the EDS results of point one. The peak was identified magnesium. Figure 1c presents the EDS results of point two. The peak was identified magnesium zinc and oxygen. Figure 1d presents point 3. This point occurred due to the chemical activity of matrix and reinforcement compound occurred during sintering process.
Hardness measurements were carried out on polished samples using a Rockwell hardness tester machine, Matsuzawa mark DXT model hardness tester with a load 15 kg applied for 15 second.
Each hardness value was the average of five measurements is shown in Figure 2.
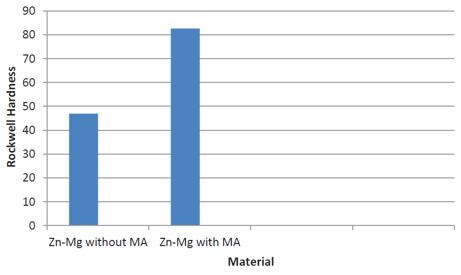
Figure 2: Rockwell hardness values after hot sintering process The aim of C. Yao, Z. Wang, S. Leng Tay, T. Zhu, W. Gao study was to investigate the effect of Mg addition on the microstructure and electrochemical properties of Zn–Mg alloys, and explore the mechanism of improving corrosion resistance of Zn–Mg alloy.
Zn–Mg alloys with different Mg contents (~250 g cast block for each composition) were prepared by casting method. Zn metal (purity > 99.90%) was melt in an MgO crucible using molten salt furnace at 560°C, and then MgZn2 intermetallic was added into the molten Zn with the shielding argon gas to inhibit the oxidation of Mg. No flux was used. The melt was homogenized by intense mechanical stirring, and then poured into a permanent mold and cooled down under Ar atmosphere protection. The obtained Zn–Mg alloys were cut into 20 mm x 20 mm x 2 mm samples. The tested chemical compositions of these samples by EDS are given in Table 1. The measured compositions are different from nominal ones, which are likely due to the oxidation of Mg or metal residuals sticking on mechanical mixer or crucible.
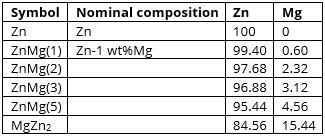
Table 1: Chemical composition of the investigated alloys The microstructures of Zn–Mg alloys were observed using optical microscope (Olympus BX60 M) and environmental scanning electron microscopy (ESEM, Philips XL-30S) equipped with energy dispersive spectroscopy (EDS, SUTW-Sapphire). The metallurgical specimen were ground and polished to 1 lm following standard procedure and etched using 5 wt.% Nital for 20 s to reveal the microstructure. XRD (Philips PW 1710, U = 40 kV, I = 40 mA) phase analysis was conducted with Cu Ka irradiation (k = 0.15406 nm). The microhardness was measured using a tester (Leco M400) with Vickers diamond indenter. The applied load was 100 g with a holding time of 15 s. At least 4 measurements under the same condition were conducted on each specimen, and the average value was used as the microhardness (HV). The electrochemical properties of Zn–Mg alloys in 3.5 wt.% NaCl solution were investigated using an electrochemical workstation (CHI604D) at 20°C. A flat cell was used as the standard set-up of electrochemical testing. The Zn–Mg alloy to be investigated was used as the working electrode, a platinum sheet was used as the counter electrode, and Ag/AgCl/ in saturated KCl electrode was used as the reference electrode. Specimens were ground and polished to 1 μm and cleaned in ethanol before electrochemical testing. A surface area of 1 cm2 was exposed to the saline solution during electrochemical test. Specimens were first immersed into the solution to reach a stable open circuit potential (OCP), and then electrochemical impedance spectroscopes (EIS) and potential dynamic polarization curve were tested and recorded.
As conclusions they drawn that:
- The microhardness of specimens increased with increasing Mg content: from 43.40 HV for pure Zn to 345.75 HV for MgZn2. ZnMg(3) alloy possessed a nano-structure and the best corrosion resistance.
- Potentio-dynamic polarization curves indicated that the Ecorr of ZnMg(3) alloy is more positive than that of Zn, with a low icorr of ~34% of Zn. Further increasing Mg content resulted in decreased corrosion resistance.
- EIS tests were conducted and a fitting equivalent circuit was obtained to simulate the corrosion process of ZnMg(3). The impedance of ZnMg(3) alloy was much higher than that of Zn when the frequency changing from 1 to 100,000 Hz; and ZnMg(3) alloy exhibited a wave crest close to 53°.
- The nano-structured ZnM(3) alloy is tended to form a uniform protective layer of Mg containing corrosion products on the surface which contributes to a general precipitation of Mg-modified simonkolleite and retards localized corrosion.