Abstract
The HISARNA process is an alternative hot metal production process that combines several different technologies which eliminates the need for sinter and coke production plants.
The result is a superb reduction in carbon footprint with CO2 emissions for crude steel production being reduced by 20%.
Ironmaking is the most labor, energy and investment- intensive step in the steel production chain. Although deemed very efficient (after centuries of empirical and fundamental improvements), today’s dominant ironmaking technology, the blast furnace (BF), is under increasing pressure from environmental, technical and economic perspectives.
The production of iron is the most energy intensive step in the steelmaking process. Currently, two fundamental routes can be used in steelmaking: an integrated steel plant or a mini-mill. In the integrated steel plant, iron ore is reduced in blast furnaces by coke. For economic and environmental reasons, coal and other fuels are increasingly injected directly into the blast furnace to replace coke.
In the mini-mill, recycled steel and scrap are melted in an Electric Arc Furnace (EAF) and further processed into final products without an iron production step. However, products derived from direct reduction of iron ore without melting (e.g. DRI, HBI (Hot Briquetted Iron)) or cast pig iron may be utilized as feed in addition to scrap steel. EAFs can also be fed with molten iron.
Therefore, the product of the smelting reduction process can be fed to mini-mills or integrated plants. The smelting reduction process usually produces hot metal from ore at molten-state without using a blast furnace. That’s why it is also called alternative iron-making process. Figure 1, shows these two routes and the use of the production of SR and DR clearly.
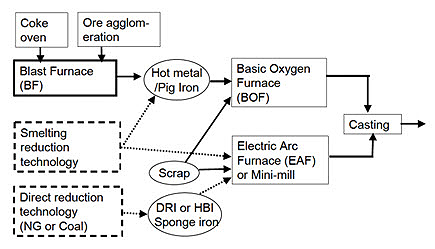
Figure 1: Two major routes for producing iron and steel: integrated and mini-mills Despite the apparent environmental advantages of the new ironmaking technologies, the blast furnace is still predicted to be the single largest process for ironmaking from iron ore until 2050. However, the proportion of blast furnace (BF) - basic oxygen furnace (BOF) steelmaking could drop to 40 % in 2050 from the current level of 60 % as the blast furnace ironmaking proportion falls from around 95 % to 60 % of the iron ore processed.
An alternative hot metal production process has been developed. This involves a class of smelting reduction technology called HISARNA (see Figure 2). This is a combination of three different technologies: 1) heated screw coal pyrolysis feeder 2) cyclone converter furnace (CCF) and 3) HiSmelt vessel.
This ironmaking process allows the direct use of fine ore and non-coking coal, therefore eliminating sinter (agglomerating) and coke production plants and reducing the number CO2 emissions point sources within the site.
HISARNA alone could reduce the CO2 footprint of crude steel produced by 20%. Together with CCS, it could achieve a reduction of ~80% compared to the CO2 footprint per tonne of crude steel produced from a conventional blast furnace. Furthermore, the use of biomass or other waste materials could replace part of the coal used in the operation of HISARNA.
Currently, a pilot plant at Tata Steel’s IJmuiden works produces 8 thm/d HM. This has recently completed its second experimental campaign phase and the indications are that objectives have been achieved, although these have not yet been publically reported. The third phase is scheduled for the spring/summer of 2013. It was assessed that the HISARNA technology, if demonstrated on a larger scale, could become commercially available after 2030. However, like any smelting technologies developed in the past decades, HISARNA would still face several technology development challenges.
HIsarna is a new technology that has the theoretical potential to reduce emissions from steelmaking by 20%, by enabling the direct input of coal and fine iron ore into the iron making furnace. The technology saves energy consumption by eliminating two of the key raw materials processing stages in blast furnace ironmaking - coking (the production of coke from coal) and sintering (the agglomeration of fine iron ore).
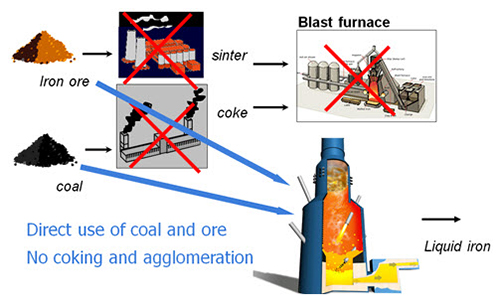
Figure 2: Comparison with the Blast Furnace route