Abstract
The Continuous Rheoconversion Process (CRP) is designed to be flexible allowing both thixocasting and rheocasting to be achieved by mixing two melts together at near liquidus temperatures to achieve smaller grain sizes and more globular structures.
Key advantages of the CRP include continuous conversion of liquid to slurry, can be used with different alloys, benefits in simplified re-cycling.
The Continuous Rheoconversion Process (CRP) is a novel, low-cost rheocasting process that was developed at MPI/WPI in 2002.
The process combined two separate techniques, liquid mixing and passive stirring, previously reported in the literature to produce globular slurries. The mixing of two melts of different composition (whether grain refined or not) near their respective liquidus temperatures and passive stirring of liquid metal in channels (instead of active stirring via mechanical or electromagnetic means) have been shown to promote smaller grain sizes and more globular structures.
It was thought that combining these two approaches would allow fully globular microstructures to be attained. Additionally, the CRP was designed to be flexible, allowing for thixocasting or rheocasting applications as well as batch or continuous casting.
The schematic diagram, Figure 1 illustrates the concept of a “tortuous path” to induce forced convection.
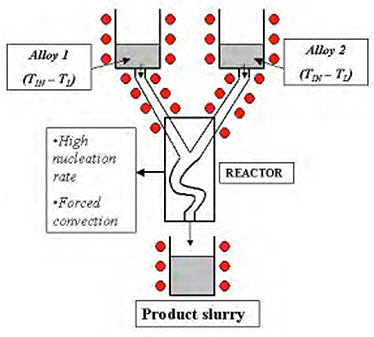
Figure 1: Schematic of the Continuous Rheoconversion Process (CRP) The major characteristics of the CRP apparatus include independent temperature control of each precursor alloy melt, a heated channel system to transport the melts without any heat loss, and a reactor to (a) provide copious nucleation and (b) induce forced convection in the melts as they flow through it. The reactor can be preheated to vary its level of heat extraction. The above diagram is intended to provide the reader with the basic variables inherent to the device.
These parameters include but are not limited to independent control over the heat content of the melts, the chemical composition of each melt, and the rate at which heat is extracted from the “product melt” within the reactor.
Recently the CRP has been scaled up for industrial applications. To retrofit most die casting facilities, the reactor has been optimized and simplified in such a way that only one melt is involved wherein both nucleation and mixing takes place simultaneously within the reactor. Moreover, to enhance the control of melt nucleation and to conveniently adjust slurry fraction solid, an optimized cooling system is incorporated into the reactor (as illustrated in Figure 2).
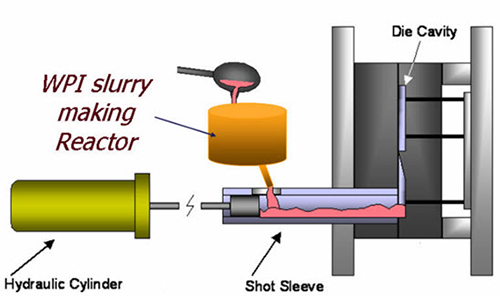
Figure 2: CRP concept implemented within a typical die casting setting The advantages of the CRP process include:
- Continuous conversion of liquid to slurry
- Flexible
- Thixocasting or slurry-ready
- Not alloy specific
- Allows for rapid adjustment of solid content
- Recycling of scrap easy to incorporate
- Can be used with one melt as well - design flexibility
- The CRP can accommodate significantly higher levels of superheat than existing slurry-on-demand processes
- Commercially viable - patent application submitted and in process