Abstract
Martensitic (MART) steels are part of the important group of Advanced High-Strength Steels (AHSS) steels, which are specifically engineered to meet the challenges of today’s vehicles for stringent safety regulations, emissions reduction, solid performance, at affordable costs.
Due to the precise processing and quenching stages post forming, MART steels show the highest tensile strength level of all multiphase steels.
Advanced High-Strength Steels (AHSS) are complex, sophisticated materials, with carefully selected chemical compositions and multiphase microstructures resulting from precisely controlled heating and cooling processes. Various strengthening mechanisms are employed to achieve a range of strength, ductility, toughness, and fatigue properties. These steels aren’t the mild steels of yesterday; rather they are uniquely lightweight and engineered to meet the challenges of today’s vehicles for stringent safety regulations, emissions reduction, solid performance, at affordable costs.
The AHSS family includes Dual Phase (DP), Complex-Phase (CP), Ferritic-Bainitic (FB), Martensitic (MS or MART), Transformation-Induced Plasticity (TRIP), Hot-Formed (HF), and Twinning-Induced Plasticity (TWIP). These 1st and 2nd Generation AHSS grades are uniquely qualified to meet the functional performance demands of certain parts. For example, DP and TRIP steels are excellent in the crash zones of the car for their high energy absorption. For structural elements of the passenger compartment, extremely high-strength steels, such as Martensitic and boron-based Press Hardened Steels (PHS) result in improved safety performance. Recently there has been increased funding and research for the development of the “3rd Generation” of AHSS. These are steels with improved strength-ductility combinations compared to present grades, with potential for more efficient joining capabilities, at lower costs. These grades will reflect unique alloys and microstructures to achieve the desired properties.
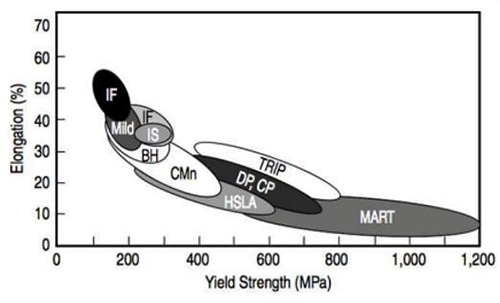
Figure 1: Comparison of tensile properties of different conventional and AHSS steel grades. Typical microstructures of AHSS are illustrated in Figure 2 and Table 1. However, the volume fractions of different microstructural constituents in industrially produced AHSS might slightly differ from these typical values.
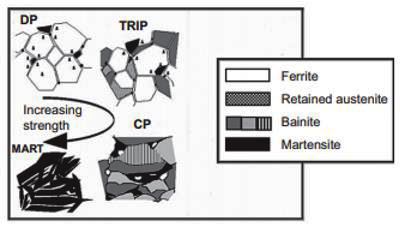
Figure 2: Illustration of typical microstructures of various AHSS. (DP: dual phase steel; TRIP: TRIP aided steel; CP: complex phase steel; MART: martensitic steel).
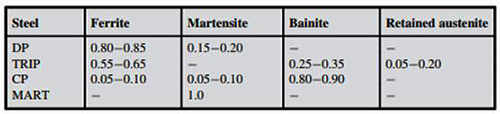
Table 1: Typical proportions of different phases in AHSS (phase contents are in volume fraction).
Martensitic (MART/MS) Steel
To create MART steels, the austenite that exists during hot-rolling or annealing is transformed almost entirely to martensite during quenching on the run-out table or in the cooling section of the continuous annealing line. The MART steels are characterized by a martensitic matrix containing small amounts of ferrite and/or bainite as observed in Figure 3.
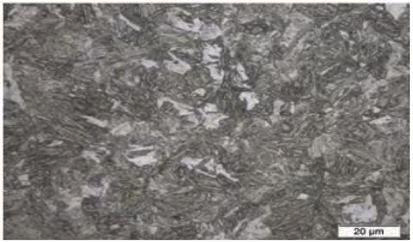
Figure 3: Microstructure for MS 950/1200. Within the group of multiphase steels, MART steels show the highest tensile strength level. This structure also can be developed with post-forming heat treatment. MART steels provide the highest strengths, up to 1700 MPa ultimate tensile strength. MART steels are often subjected to post-quench tempering to improve ductility, and can provide adequate formability even at extremely high strengths. Engineering stress-strain curves for MART steel grades are located in Figure 4. There are various types of MS grades currently used for automotive applications. Examples are MS 950/1200 used in the production of Cross-members, side intrusion beams, bumper beams, bumper Reinforcements while MS 1150/1400 used for the production of Rocker outer, side intrusion beams, bumper beams, bumper reinforcements.
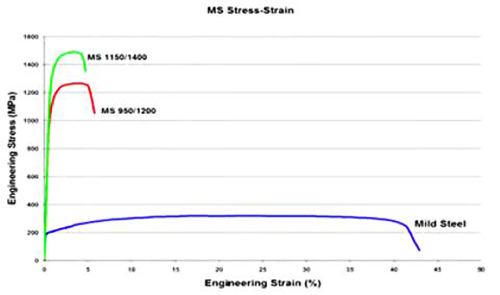
Figure 4: Engineering stress/ strain curves for various type of MS steel grades.