Abstract
The KIVCET (Oxygen Flash Cyclone Electro Thermal) Process represents an innovative lead smelting technology developed in Kazakhstan, with the first commercial implementation in 1985. This single-stage, autogenous smelting process eliminates the need for traditional sintering and is specifically engineered for complex ores with high zinc content. The process efficiently recovers lead while simultaneously enabling zinc recovery, produces concentrated sulfur dioxide gas suitable for sulfuric acid production, and meets modern environmental protection standards. Its design integrates flash smelting with electrothermal settling, making it particularly valuable for processing polymetallic ore concentrates in contemporary metallurgical operations.
Introduction and Historical Development
The KIVCET process, also called the Oxygen Flash Cyclone Electro Thermal Process, was developed by VNIITSVETMET Institute in Ust-Kamenogorsk, Kazakhstan, under the supervision of Professor A. Sychev. The first commercial KIVCET unit was installed and operated at the Ust-Kamenogorsk Lead-Zinc Combinate (now Kazzinc J.St.Co) in 1985. This technology has since become recognized for its efficiency in processing complex lead-zinc ores.
Process Chemistry and Operation
The KIVCET process consists of two primary stages. In the first stage, lead sulfide concentrate, zinc plant residues, recycled dust, silica, limestone, fine coal, and moderately coarse coke are injected at the top of the reaction shaft along with oxygen. The sulfides of lead, zinc, and other metals are converted to metal oxides while heating in a fine coal flame. The oxides, silica, and limestone form a semi-fused slag, while the gas reaches up to 15% sulfur dioxide concentration.
Key reactions in this stage include:
C(s) + O₂ = CO₂
C(s) + ½ O₂(g) = CO(g)
S + O₂(g) = SO₂
PbS + 3/2 O₂(g) = PbO + SO₂(g)
ZnS + 3/2 O₂(g) = ZnO + SO₂(g)
PbS + 2PbO = 3Pb + SO₂(g)
In the second stage, the bullion passes through the molten slag layer under the coke checker and enters the electrothermal settler together with the zinc-bearing slags. Here, heat from graphite electrodes maintains the bullion-slag bath in a molten state. The lighter slag floats to the surface while the heavier bullion sinks to the bottom of the settler, allowing them to be tapped separately from the furnace.
Product Processing and Recovery
The lead bullion produced in the KIVCET furnace undergoes further treatment to remove copper, arsenic, and antimony before it is ready for electro-refining.
Slag from the KIVCET furnace is treated in a slag fuming furnace where zinc in the slag vaporizes to form zinc oxide fume. This fume is further processed in an oxide leaching plant to recover zinc, indium, germanium, and cadmium.
The hot sulfur dioxide gas (approximately 1200°C) from the reaction shaft is cooled in waste heat boilers and then passes through electrostatic precipitators. The cleaned sulfur dioxide gas is directed to sulfuric acid plants, providing an additional valuable product stream.
Furnace Design and Operation
The KIVCET smelter consists of a smelting reaction shaft connected to an electric furnace. Sulfide concentrate is blown into the shaft through a burner with high-purity oxygen after appropriate slag-forming flux materials have been added. The material undergoes roasting and smelting primarily while in suspension.
The metal oxide-rich melt enters the adjoining electric furnace below a water-cooled partition wall immersed in the melt. This furnace reduces PbO and ZnO through the addition of coke. Process waste gas, rich in SO₂, is withdrawn through a waste-gas shaft positioned adjacent to the smelting shaft. Lead bullion and slag are tapped separately from the electric furnace. The zinc contained in the fume can either be recovered as metal in a condenser or oxidized to zinc oxide.
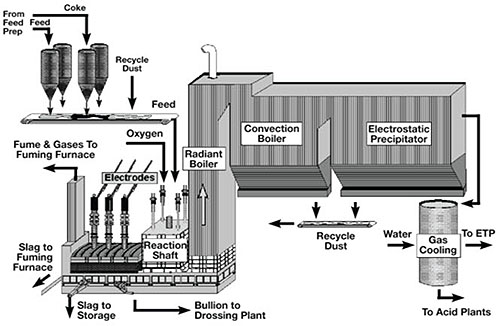
Figure 1: Schematic Diagram of the KIVCET furnace
Key Advantages of the KIVCET Process
The KIVCET process offers several significant advantages over conventional lead smelting technologies:
- Elimination of the sintering requirement, reducing process complexity
- Single-stage processing, improving operational efficiency
- Autogenous smelting when feed contains 18% or more sulfur, reducing energy costs
- Simultaneous recovery of zinc, enhancing resource utilization
- Production of small volumes of SO₂-rich waste gas, ideal for sulfuric acid production
- Compliance with industrial hygiene and environmental protection requirements
These advantages make the KIVCET process particularly suitable for processing complex polymetallic ores with high zinc content that would be challenging to process using conventional lead smelting technologies.