Abstract
Hot tearing, also known as hot cracking or hot shortness, is a critical defect in metal casting that occurs during solidification. This comprehensive article examines the formation mechanisms, contributing factors, and prevention strategies for hot tearing. It explores how this irreversible failure develops in semisolid castings, analyzing both microscopic and macroscopic factors including thermal stresses, liquid film distribution, and solidification characteristics. The article also presents classification systems for casting defects and details various theoretical models explaining hot tear formation.
Classification of Casting Defects
The metal casting industry employs a systematic classification based on physical descriptions of defects. This system allows identification through direct observation or precise description, without requiring prior knowledge of causes. Seven main categories are designated by letters: Metallic Projections (A), Cavities (B), Discontinuities (C), Defective Surface (D), Incomplete Casting (E), Incorrect Dimensions or Shape (F), and Inclusions or Structural Anomalies (G).
Each category is subdivided into groups and subgroups, designated by numerals. A third numeral specifies particular defects within subgroups, resulting in a letter followed by three numerals for complete identification. While some defects might logically fit multiple categories, the system's focus on physical appearance rather than causation helps maintain clarity in identification.
Understanding Hot Tearing Formation
Hot tearing represents the formation of irreversible cracks in semisolid castings. This phenomenon occurs when the solid fraction reaches 85-95% and the solid phase forms a continuous network of grains. The defect typically develops when solidification shrinkage isn't adequately compensated, and thermal stresses are present.
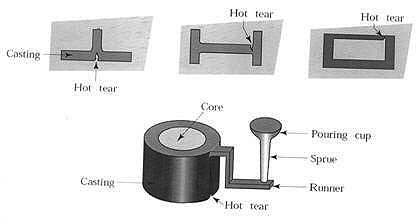
Figure 1: Common locations of hot-tearing defects
Hot tears initiate above the solidus temperature and propagate through interdendritic liquid films. During solidification, liquid flow through the mushy zone decreases until it becomes insufficient to compensate for shrinkage, leading to cavity formation. The resulting fracture surface exhibits a characteristic bumpy texture covered with a smooth layer, occasionally showing solid bridges between crack surfaces.
Process Factors and Mechanisms
During direct-chill (DC) casting, primary and secondary cooling creates strong macroscopic thermal gradients in the billet/ingot. These gradients cause uneven thermal contraction, potentially leading to distortion or triggering hot tearing in vulnerable sections. The term "mushy zone" refers to the transition region between liquidus and solidus, though this terminology can be misleading as the upper portion contains freely suspended grains in liquid slurry.
The deformation behavior of the mush critically affects hot tear formation. Alloy composition plays a significant role, with larger freezing ranges typically increasing susceptibility to hot tearing. This occurs because such alloys spend more time in a vulnerable state where thin liquid films exist between dendrites. Surface tension between liquid and solid phases determines liquid film distribution, with low surface tension potentially weakening the mush structure.
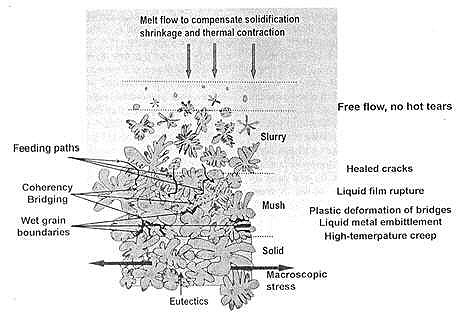
Figure 2: Illustration of different length scales in equiaxed dendritic solidification
Theoretical Understanding and Prevention
Modern research emphasizes the importance of mesoscopic strain rate in hot tearing. Semisolid material can accommodate rearrangement and filling of gaps during solidification, but these processes require time. A maximum sustainable strain rate exists beyond which fracture occurs. Recent models, such as those proposed by Rappaz, incorporate this strain-rate-based approach.
Prevention strategies focus on maintaining fine grain structure and controlling casting conditions to minimize temperature and stress gradients. Understanding the interaction between microscopic phenomena (crack nucleation, stress concentration) and macro-scale factors (feeding, strain rates) remains crucial for effective control of hot tearing.
Conclusion
Hot tearing represents a complex interplay of multiple physical mechanisms operating at different scales. Successful prevention requires careful control of process parameters and understanding of material behavior during solidification. Ongoing research continues to refine our understanding of this critical casting defect.