Abstract
Isothermal forging is an advanced metal-forming technique where die and workpiece are maintained at identical temperatures throughout the forging cycle, enabling uniform material deformation. This process significantly enhances efficiency and quality in manufacturing complex components, particularly for titanium alloys used in aerospace and medical applications. By eliminating die chilling and allowing controlled deformation at slow strain rates, isothermal forging produces near-net shape components with optimal material utilization, consistent microstructure, and superior mechanical properties, despite higher tooling costs and longer processing times compared to conventional forging methods.
Introduction to Isothermal Forging
Isothermal forging belongs to a category of advanced forming processes that provide exceptional control over deformation behavior, microstructure evolution, and resultant material properties. This technique stands alongside other sophisticated processes such as near-isothermal (hot die) forging, multiaxial isothermal forging with pack rolling, superplastic forming, and diffusion bonding—all of which have revolutionized the production of titanium alloy components.
The defining characteristic of isothermal forging is the maintenance of equal temperatures between the die and workpiece throughout the entire forging cycle. This temperature uniformity eliminates die chilling, resulting in consistent material deformation across the component. The process represents a significant advancement in metal forming technology, particularly for materials that are difficult to process using conventional techniques.
Process Mechanics and Technical Advantages
In isothermal forging, both the die and workpiece are heated to the same elevated temperature and maintained at this temperature throughout the operation. This approach fundamentally differs from conventional forging, where dies are typically cooler than the workpiece, leading to rapid surface cooling during contact.
The process offers several technical advantages:
- Uniform deformation throughout the material due to elimination of die chilling
- Ability to forge at very slow strain rates, reducing the required processing load for strain-rate sensitive materials like titanium alloys
- Production of components with small corner and fillet radii, reduced draft angles, and smaller forge envelopes
- Achievement of net or near-net shape components with fewer processing steps
- High degree of consistency in microstructure and properties between forgings
The equipment may operate in vacuum conditions, depending on the specific application requirements. While the equipment costs are substantial, the benefits often justify the investment for critical applications.
Economic Considerations and Industrial Applications
Isothermal forging competes with classical closed-die forging technologies in industrial settings, offering significant advantages despite some economic constraints. For complex titanium alloy components, material cost savings can reach 40–45% compared to conventional methods. Additionally, machining costs can be reduced by up to 30%, depending on component complexity and final tolerance requirements.
However, several factors affect the economic viability of isothermal forging:
- Tooling costs for heat-resistant alloy dies are 2–3 times higher than conventional dies
- Precise process control is essential, particularly for die heating and lubrication
- Longer cycle times compared to conventional forging processes
Due to these considerations, isothermal forging has traditionally been reserved for safety-critical components in aerospace and jet engine applications. However, recent developments have expanded its application to the medical and orthopedic fields, demonstrating its versatility for high-value components requiring exceptional quality.
Key Characteristics of Isothermal Forging
Isothermal forging is characterized by:
- Form pressing with die temperatures nearly equal to workpiece temperature
- Low temperature gradient between tool and workpiece
- Production of high-quality parts in almost "ready-to-use" shape
- Elimination of flash removal steps
- Shorter overall production times for finished parts
However, challenges include the potential for melted pockets due to local overheating if forming rates are too high, requiring precise process control.
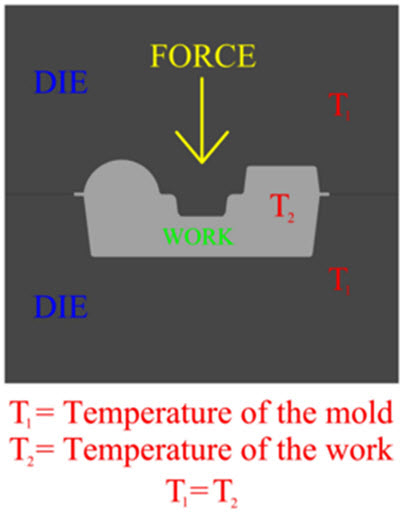
Figure 1: Isothermal forging process setup
Future Prospects and Emerging Applications
While isothermal forging has primarily been utilized in aerospace and defense sectors, its application is expanding to other industries requiring high-performance components. The medical device industry, particularly orthopedic implants, represents a growing application area where the material savings and enhanced mechanical properties justify the higher processing costs.
As manufacturing technologies continue to advance, opportunities to reduce the economic barriers to isothermal forging are emerging, potentially broadening its industrial adoption beyond traditional high-value applications.