Abstract
Ultra Cast Strip (UCS) produced by the CASTRIP process is categorized by irregular shaped grain boundary ferrite, some Widmanstätten ferrite and fine intra-granular acicular ferrite.
With microstructure control being directly related to the solidification process, the nucleation density during solidification can the number one contributor to austenite grain size and thus, subsequent ferritic microstructures.
The final microstructure of the recent Ultra Cast Strip UCS grades produced by the CASTRIP process consists of irregular shaped grain boundary ferrite, some Widmanstätten ferrite and fine intragranular acicular ferrite. This microstructure is considerably different from conventional hot rolled and cold rolled strip products. Accordingly the effects of the main processing variables such as the alloy design, hot rolling reduction and cooling conditions on the final microstructure and mechanical properties had to be established. In addition an assessment of the formability of this microstructure was required. In the paper of C. R. Killmore et al is presented an overview of recent experiences with the manufacture of current UCS products produced by the CASTRIP process and presents some results from the assessment of these UCS products in a range of formability tests.
Microstructure evolution in strip casting is fundamentally coupled to the solidification process. The nucleation density during solidification can profoundly influence the austenite grain size and thus, subsequent ferritic microstructures. Under normal cooling conditions, the microstructure of the as-cast material is a mixture of polygonal ferrite and low temperature transformation products such as acicular ferrite (see Figure 1).
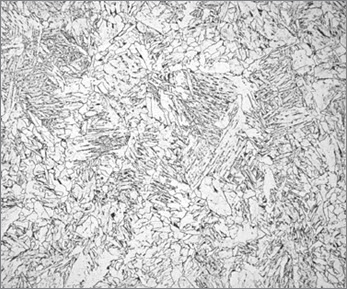
Figure 1: Typical as-cast UCS microstructure
Typical examples of the non-metallic inclusions present in UCS material now able to be produced by the CASTRIP process are given in Figure 2. The size range of the globular inclusions typically varied from about 10µm down to very fine particles in the order of only 5-30nm. A large proportion of the inclusions were in the 0.5µm to 5µm size range. The composition of the inclusions was found to vary with the inclusion size, with the proportion of Mn decreasing and the proportion of Si increasing, with decreasing inclusion size, which is consistent with the relative deoxidation potential of these elements.
Some of the inclusions were composed of a complex mixture of phases including MnS, TiO and CuS. In the case of the very fine (5-30nm) particles, Figure 2c, they have been identified as Fe-Si-O spinel precipitates using TEM techniques. The size range and compositions of the inclusions in the UCS steels produced by the CASTRIP process can now be optimally engineered by virtue of careful control of the dissolved oxygen levels at the start of solidification and other alloying additions. The Mn-Si deoxidised steel practice provides flexibility for setting appropriate dissolved oxygen levels that are not possible in conventional Al killed steels and enables the non-equilibrium conditions generated by the very high solidification rates involved with strip casting to be fully exploited in generating the desired inclusion/ particle populations.
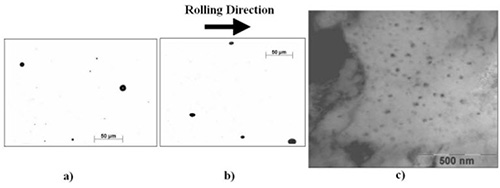
Figure 2: a) Typical worst case field showing globular inclusions found in as-cast UCS material, and b) elliptical inclusions found in hot rolled products c) thin foil TEM photomicrograph showing the dispersion of fine nano sized particles in UCS products.
The larger 0.5-5.0 µm size non-metallic inclusions have been found to play a very beneficial role in the development of the final microstructure by promoting the intragranular nucleation of acicular ferrite, without detriment to the formability of the strip. In addition the very fine particles (5-30nm) have been shown to influence the response of the steel to downstream processes, such as annealing, high temperature heat treatment and resistance to critical strain grain growth during fabrication.