Abstract
Magnesium alloys offer a huge amount of promise for the 21st century in helping to solve challenges in specific applications by taking advantage of its excellent weight to strength ratios when compared to aluminums and steels.
In this article, we take a look at how Twin Roll Casting can widen the potential of Mg alloys by allowing strips of 1 to 2mm to be produced with excellent mechanical properties.
TRC (Twin-Roll Casting) is known to be efficient and economical for production of sheets or thin strips of aluminum alloys, magnesium alloys and stainless steels, and also for cladding layers of metal sheets without developing oxide films at interfaces between layers. However, the phenomenon occurring in TRC is so complicated that a proper setting of process parameters is not a feasible task.
As the one of the lightest commercial structural alloys, magnesium alloys are considered to be one of the most promising materials for the 21st century. Magnesium is 36% lighter per unit volume than aluminum and 78% lighter than iron. When alloyed, magnesium has the best strength to weight ratio of all structural metals. The Mg alloys have excellent specific strength and stiffness, and good machinability castability and damping capacity, which are superior to other metals such as aluminum alloys and steel. Moreover, Mg alloys have outstanding shielding capability against electromagnetic interference.
Conventional strip production usually requires several process steps to reach the final strip thickness. Strip casting can reduce some of the process steps and make strip processing simpler and easier, especially for alloys with poor deformability. The twin-roll casting process can directly obtain strips with thickness less than one or two millimeters.
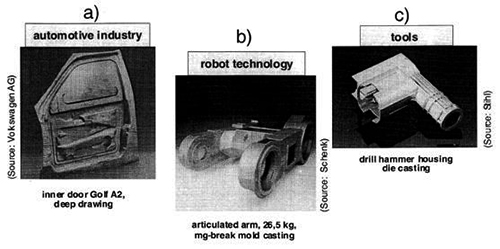
Figure 1: Examples of some magnesium products Owing to its good recyclability, Mg alloys have attracted global attention from the standpoint of environmental conservation. The process of the roll casting can be accomplished both by physical transformation such as pouring, solidifying, rolling, running out and by cooling in a very short time. In order to understand the conditions and coupling thermal-stress fields intuitively and accurately in the molten pool during rolling, the numerical simulation with finite element model is employed in the research work.
The twin-roll casting process can directly obtain strips with thickness less than one or two millimeters. In this paper, the metallurgical characteristics of the twin-roll strip casting process were analyzed and discussed. A laboratory scale vertical twin roll caster in prepared AZ31 magnesium alloy strips, with 1.0 to 2.0 mm thick and 150mm wide. Process stability in the thin strip casting process of the alloy has been studied, the casting temperature (superheat) was proven to be a key factor influencing process stability and casting strip quality. The as-cast microstructure of the alloy was analyzed and evaluated by optical microscopy, which showed that the as-cast microstructure was composed of developed dendrites when the superheat was high, and of a rosebush-like structure when the superheat was low. When the casting temperature was close to the liquid phase temperature, the as-cast microstructure became global or grainy, and the grain size of the cast strip was very small. This remarkably improved the deformability of the as-cast strip.
In the study of C. Yang et al, VTRC (Vertical Twin-Roll Casting) was analyzed by the rigid-visco plastic finite-element method for Mg-AZ31. The objective of this study was to find out differences between these materials in various aspects of manufacturing, such as melt flow, temperature distribution, solidification, roll-separating force and roll torque. A commercial code DEFORM was utilized for the purpose. Across sectional view of a vertical twin-roll casting is illustrated in Figure 2. As the melt flows through the gap between two identical rolls rotating in opposite directions, it cools, solidifies and is finally rolled to a sheet or strip with a specific thickness. As shown in Figure 3, the principle of this technology is to extract heat from the melt through the contact surface with the rolls and also to impose plastic deformation into the solidified sheet. Assuming no variations of flow and temperature in the direction of the roll axis, two-dimensional analyses of the cross section were performed.
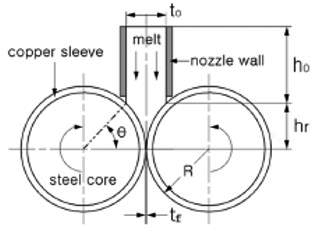
Figure 2: Cross sectional view of VTRC
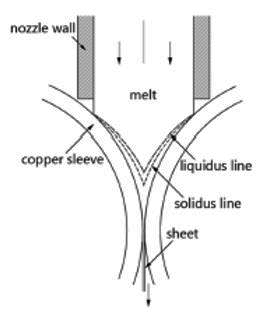
Figure 3: Liquidus and solidus temperature contours in the melt Thermal and physical properties of AZ material is shown in Table 1.

Table 1: Physical and thermal properties of materials Flow stresses of AZ31 material in literature are presented as curves in Figure 4. Since those in the mushy state were unavailable, they were derived by proportional divisions from those of the solid state to those of the liquid state. IHTC (Interface Heat-Transfer Coefficient) at the interface between a roll and a melt was assumed as a function of pressure and temperature, as shown in Figure 5. The IHTC changes drastically in magnitude at the interface where the melt gradually solidifies as it flows toward the roll exit.
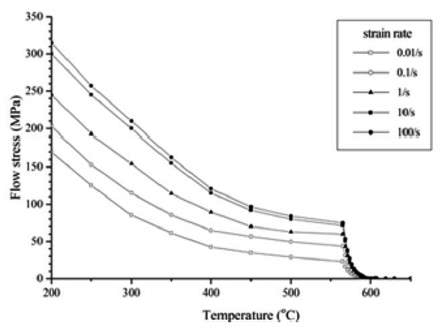
Figure 4: Flow stress of Mg-AZ31
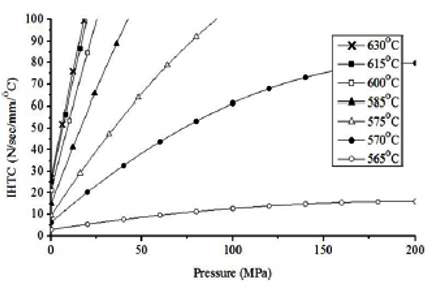
Figure 5: IHTC at the roll/Mg-AZ31 interface From these analyses, the roll speed was found out to be lower than 0.6 rad/s for Mg-AZ31 in order for the surface of the sheet to be solidified at least to avoid rupture during the process. However, if the sheet is required to be rolled to some extent during the process, the speed should be lower than 0.5 rad/s for Mg-AZ31. As the roll speed is further lowered, more plastic deformation is accumulated into the sheet. The roll-separating force and the roll torque decreased drastically as the roll speed increased due to a decrease in kinetic energy of vortexes and the viscosity, respectively.