Abstract
TMCP (Thermo-Mechanical Control Process) technology, developed in Japan in the 1980s, revolutionized steel manufacturing. This process enables the production of steels with fine and uniform acicular ferrite microstructure, resulting in higher strength and superior toughness. Through improved control of hardenability and reduced susceptibility to cold cracking, TMCP steels demonstrate enhanced weldability and stability in mechanical properties, particularly suitable for high heat input welding applications.
What is TMCP?
In traditional steel manufacturing, hot rolling served merely to achieve nominal dimensions like thickness, width, and length. For exceptional quality requirements, manufacturers would implement additional off-line heat treatments such as normalizing or quenching and tempering. As quality demands increased, TMCP emerged as an innovative solution for plate rolling.
The TMCP process requires comprehensive control during three critical phases: slab reheating, plate rolling, and post-rolling cooling. According to IACS (International Association of Classification Societies), TMCP encompasses both TMR (Thermo-Mechanical Rolling) and AcC (Accelerated Cooling), though industry practitioners often associate TMCP primarily with AcC.
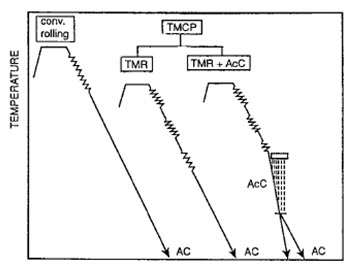
Figure 1: Definition diagram showing TMCP components
Aim of TMCP
TMCP's primary objective is to achieve fine and uniform acicular ferrite microstructure, replacing conventional steel's ferrite/pearlite banded structure. This refined microstructure results in enhanced strength and superior toughness. The relationship between tensile strength and Carbon Equivalent (Ceq) demonstrates that TMCP steels achieve higher strength levels at the same Ceq compared to conventional steels. Additionally, decreasing grain size correlates directly with improved toughness.
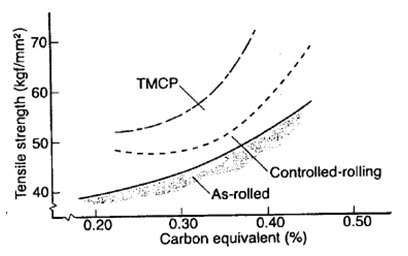
Figure 2: Graph showing Tensile Strength vs. Ceq relationship
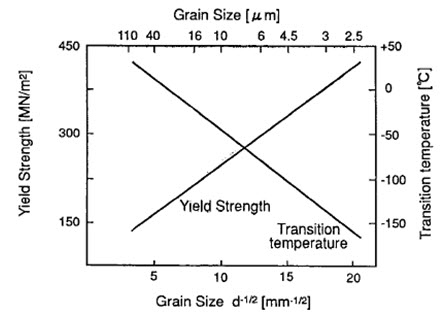
Figure 3: Graph illustrating Toughness vs. Grain Size correlation
Manufacturing Technology for High-Performance Steel based on TMCP
Steel plate performance initially improved through controlled-rolling methods. TMCP technology, combining controlled-rolling with controlled-cooling, has further enhanced steel plates' high-strength and high-performance characteristics.
Modern steel plate production relies predominantly on TMCP technology, incorporating micro-structural control suitable for higher strength and thickness, alongside advanced micro-alloying technology. The implementation of TMCP for bridge steel construction began around 1996 with the introduction of High-Performance Steel (HPS), and its usage continues to grow.
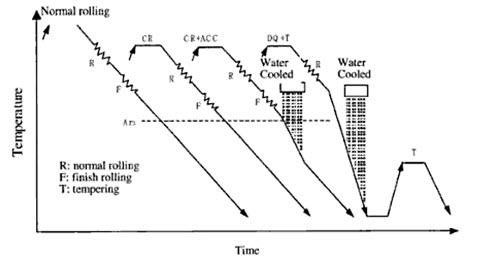
Figure 4: Illustration of modern rolling technologies
The metallurgical advantages of TMCP include grain refinement and formation of fine bainitic microstructure, achieved through controlled rolling and cooling processes. These microstructural improvements simultaneously enhance yield strength and toughness while reducing alloy requirements and Pcm values compared to conventional rolling processes.
TMCP steels demonstrate superior weldability compared to conventional steels, owing to reduced alloy content and lower Pcm values. These characteristics enable advantages such as heavy gaging and compatibility with high heat-input welding. Notable applications include the 780 MPa class steels with low Pcm used in the Akashi-Kaikyo Bridge construction.
Metallurgical Characteristics of TMCP
The microstructure control in TMCP begins at the slab reheating stage, where prior Austenite grain size is carefully regulated. During hot rolling, controlled rolling in the non-recrystallization region produces fine and worked Austenite grains. These grains subsequently transform into fine acicular ferrite or upper bainite during the accelerated cooling stage. Microscopic examination reveals that TMCP steel exhibits significantly finer and more uniform microstructure compared to conventional rolling processes.
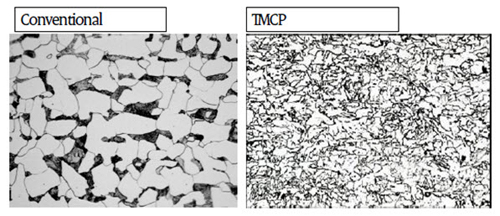
Figure 5: Comparative microstructure images of TMCP vs. conventional plates