Abstract
Development of third generation, advanced high strength steels (AHSS) is well underway and is focused on advancements to provide even more superior strength-ductility ratios than in the currently available materials such as dual phase or TRIP steels.
One of the key features of carbide free bainitic steels is the numerous processing options such as drawing potential that are possible because of the increase in wear resistance and surface hardness that directly linked to the microstructural characteristics.
In terms of in-use properties, the CFB steel is expected to achieve extremely good stretch-flangeability due to its uniform fine lath structure. On the other hand, the heterogeneities of hardness due to the presence of martensite in this advanced bainitic microstructure will allow this steel to reach a good, deep drawability.
In the study of F. Garcia Caballero, S. Allain, J.-D. Puerta-Velásquez, C. Garcia-Mateo the possibility to achieve a CFB microstructure after a hot dip galvanizing (HDG) production line for galvanized or galvannealed products, was investigated. The thermal profile of this type of annealing line is certainly not the most suitable to produce CFB microstructures. The limitations come from the short holding to achieve the bainitic transformation and the fixed temperature of the zinc baths (about 460°C). The flexibility of this class of annealing line is thus less advantageous than continuous annealing line CAL. Nevertheless, this option is worth being investigated for economic (cost of the final coated product compared to EG material) and technical reasons (several TRIP steels are already manufactured with HDG industrial lines).
Performance of Earlier Approaches in CFB Steels after HDG Simulations
A first set of steels (CAL1 and CAL2), specifically designed to achieve a CFB microstructure after a CAL process in a former work, were used. Ingots were cast using a vacuum induction melting furnace. Their actual composition is listed in Table 1. The ingots were hot rolled to a thickness of 3 mm following the thermomechanical control process of commercial SiMn TRIP steels described elsewhere. A high coiling temperature of 550°C was selected to trigger the ferrite-pearlite transformation region, and thus, to achieve soft hot rolled strips and to enable the cold-rolling without limiting the accessible gauge thickness for the final product. The strips were subsequently cold-rolled to a total reduction rate of 50% in multiple passes, without any cracks.
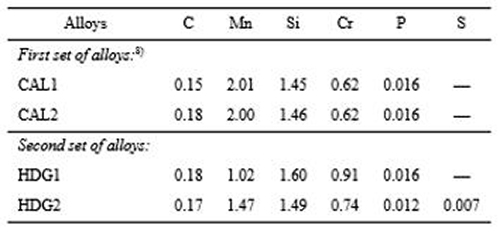
Table 1: Chemical composition of annealed cold rolled CFB steels (wt.%)
The main conclusions from their study concerning the design of CFB steels compatible with an HDG annealing are the following:
(1) Even with a devoted theoretical alloy design procedure, it seems difficult to identify a lean chemical concept suitable to fulfil the following conditions:
a. A low Ac3 temperature to achieve a fully austenitic soaking.
b. Enough hardenability to avoid proeutectoid ferrite formation upon cooling.
c. To reach a sufficient carbide-free bainitic transformation at 460°C using low Mn content.
d. To increase the bainitic transformation kinetic at 460°C to be compatible with short overageing duration.
(2) As a consequence, the tensile properties of all the studied alloys are disappointing and comparable to those of high-Si DP steels.
(3) Independently of the substrate metallurgical choice, the question of the coat-ability will be raised, especially in high-Mn and high-Si chemical concepts and will require dedicated study depending on annealing furnace technology. As concluding words, conventional HDG annealing cannot be recommended to produce fully CFB steels (i.e. without the presence of equiaxed ferrite in the microstructure), unless some improvements on soaking and cooling capabilities were explored. In this sense, Li et al. confirmed that a HDG annealing with a low end-cooling strategy, consisting of an overageing at temperatures lower than 460°C and followed by an induction heating, could be an option to achieve CFB microstructures with properties comparables to those obtained with CAL capabilities.
In the research of A.M. Gola, M. Ghadamgahi, and S.W. Ooi, two medium-carbon steel grades were tested in a wear tumbling machine to investigate microstructural changes under wet sliding abrasive wear conditions and to benchmark their performance against conventional tempered martensitic steels.
Wear resistance of carbide-free bainite
The ultimate performance of CFB steels in abrasive conditions is believed to be mainly dependent on work hardening and microstructure evolution. Transformation to martensite from retained austenite (RA) introduces compressive stresses which inhibit propagation of damage and have a grain refinement effect. The thickness of a hardened layer is related to overall pressure applied during wear and it thickens with increased number of stress cycles. Hardened layers can reach from 20 μm to 50 μm deep. This value is reliant to work-hardening capabilities of the microstructure and may be related to RA volume fraction. The clear correlation between RA fraction and wear resistance has not been found. It was reported that CFB specimens with the same hardness, but prepared using different heat treatment parameters showed better wear resistance with higher RA volume. The author concluded, that the positive result was due to higher plasticity and good toughness of carbide-free bainite.
This work contradicts the findings of Yang et al., where small amount of RA showed better wear resistance mainly due to higher hardness. In other cases where CFB steel outperformed pearlitic and martensitic structures, is was related to substantial decomposition of RA during wear, i.e. from 44 vol% to less than 20 vol%. The mechanism of damage taking place during abrasive wear in CFB steels was reported to be a combination of localized microcutting, micro-ploughing and some micro-fatigue, due to the random motion of particles in the contact, with relatively minor pitting also present. In contrast, the dominating mechanism in hard martensite is cutting. As a result, surface cracking, indentations, as well as accumulation of oxidized wear debris on the surface occur. In final stages of surface degradation, delamination of thin layers can be observed. Moreover, newly created oxides are embedded into surface as a debris, which contributes to a very high friction coefficient and strong adhesion. Created grooves are narrower than grooves visible in damaged benchmark martensitic steel, but can be significantly deeper. Overall, despite slightly lower hardness, carbide-free bainitic microstructure exhibits better wear resistance than quenched and tempered steels, including widely used boron containing steels. Additional surface treatment, i.e. laser hardfacing or laser cladding, which can increase surface hardness by almost 200 HV30, do not enhance wear resistance. Therefore, hardness should be adjusted by controlling bainitic ferrite lath thickness, carbon content and RA volume fraction, with the respect to steel cleanliness.
Two medium-carbon high-silicon steel grades were tested in a bespoke wear tumbling machine designed specially to simulate real-life wet-sliding abrasion conditions. Samples were heat treated to carbide-free bainitic and conventional tempered martensitic states of similar hardness to compare their wear resistance and to observe any microstructural changes in the subsurface. It has been shown, that for a given initial hardness carbide-free bainitic steel demonstrates superior wear resistance due to better surface hardening capabilities (increase in surface hardness of up to 18%), which is an effect to f retained austenite transforming under the stress to martensite. Furthermore, due to greater subsurface toughness then that of martensitic steel, brittle cracks, which result in flaking, are not created at the surface. The transition of retained austenite to martensite in subsurface of carbide-free bainitic samples was quantified by using special layer-by-layer X-ray diffraction methodology. It is shown that, at the surface, almost all retained austenite was transformed due to high strain level, at the same time proving that this transformation reach deeper in to subsurface than the thickness of plastically de- formed layer, which suggests stress-induced transformation.