Abstract
Vacuum die casted materials have many applications in the automotive industry as well as a number of other commercial industrial sectors.
The main benefits of VDC as opposed to other more traditional methods of casting include a higher quality surface finish, improved mechanical properties and an overall better finished product stability.
Die casting is the process where molten metal is injected into the cavity of a metallic die, held for a period sufficient for adequate solidification and then released; has been used widely in various industries, most commonly the automotive and commercial industries. Because of the rapid cooling rates and fine grain sizes combined with the ability to precision machine the die cavity and exploit high injection pressures the die casting process has many advantages over other metal forming processes.
These process benefits include improved mechanical properties over conventional casting processes, good surface finish, short cycle times, high volume capacity, good repeatability and dimensional stability. The most commonly used alloys in this process are aluminum, zinc, magnesium and to a lesser extent copper.
There are several types of die casting processes. Various processes are now in use to achieve both economically and technologically viable castings production. The variety of methods results from the different ways in which gas can be eliminated from the cavity, how the injection system works or how much heat is lost during the process.
Through vacuum die casting, it is possible to produce high-quality thin-walled parts with expected and repeatable mechanical properties, with or without heat treatment or welding. Vacuum die casting was first used in Japan and it extended rapidly around the world. Vacuum die casting has some important advantages: the vacuum systems remove the air from the cavity reducing gas porosity. In addition, very thin sections can be casted easily; good surface finishing properties and appearance can be obtained with no need for further machining.
Using this technique, casting defects are low and the rejection of the component is reduced. The general principle is the same as in low-pressure die casting. Depending on the alloy used, the required properties can be achieved in vacuum die casting even without additional heat treatment; but whenever such treatment is required, it will produce superficial defects in the presence of even minor gas porosity, which are usually not tolerated on the final product.
Figure 1 shows a schematic of the Vacuum die casting VDC process. It is important to note the entire melting, pouring and injection process in conducted under stringent vacuum controls. The part is exposed to atmosphere only after complete solidification has occurred.
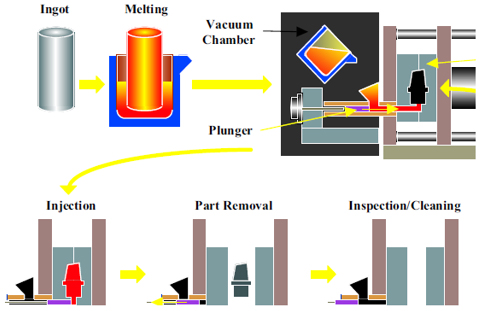
Figure 1: Schematic of Vacuum Die Casting System
The application of vacuum die casting to superalloy materials offers the potential to develop novel refined material microstructures for a broad range of alloy compositions. As would be expected due to the presence of a refined grain size, the mechanical properties of material traditionally produced via investment casting for turbine blade applications show improved tensile and reduced stress rupture capability. Wrought high volume fraction γ’ disk alloys exhibit reduced strength and significantly enhanced stress properties.
The highest temperature capability structural casting alloy (Inco 939) shows improved strength and reduced stress rupture life. The combination of mechanical property balance ability to fabricate complex shapes should offer the opportunity to exploit die cast superalloys in niche applications in the temperature range of 649°C to 816°C if reasonable rupture capability is required. To be successful, the process must offer an economic as well as technical advantage. Improvements to casting quality would be required to meet aerospace requirements and it is highly likely that this could be achieved with investment in the technology.