Abstract
The Submerged Arc Furnace (SAF) is an advanced electrical heating system specifically designed for ferro-alloy production. This technology utilizes electrical power to facilitate pyrometallurgical smelting processes, offering superior temperature control and reduction potential adjustment capabilities. SAFs are distinguished by their high process efficiency, safe maintenance features, and ability to produce various ferro-alloys including Fe-Mn, Si-Mn, Fe-Si, and Mg-Si. The system's energy-intensive nature significantly impacts production costs, making efficiency optimization crucial for operational success.
Introduction to Submerged Arc Furnace Technology
Submerged Arc Furnaces represent a cornerstone technology in modern metallurgical processing. These specialized heating systems employ electrical power to produce a wide range of ferro-alloys, offering distinct advantages in process control and operational efficiency.
Types and Classification of Arc Furnaces
Arc furnaces are categorized based on their heating methods:
- Direct arc furnaces: Electric arcs burn between electrodes and the heated material
- Indirect arc furnaces: Arcs burn between electrodes above the heated materials
- Power supply classification: AC or DC furnaces
Energy Efficiency and Production Costs
The SAF smelting process is notably energy-intensive, with energy consumption representing a significant portion of total production costs. However, the system's efficiency in temperature control and reduction potential adjustment makes it the preferred choice for ferro-alloy production. Over time, an independent ferro-alloy industry has established itself to meet the steel industry's continuously increasing demands.
Production Capabilities
SAFs excel in producing various ferro-alloys, including Fe-Mn (Ferro-manganese), Si-Mn (Silico-manganese), Fe-Si (Ferro-silicon), and Mg-Si (Magnesium-silicon). The production of high-purity ferro-alloys involves a combination of Submerged Arc Furnaces, Electric Arc Furnaces, and Refining Furnaces, ensuring optimal process efficiency.
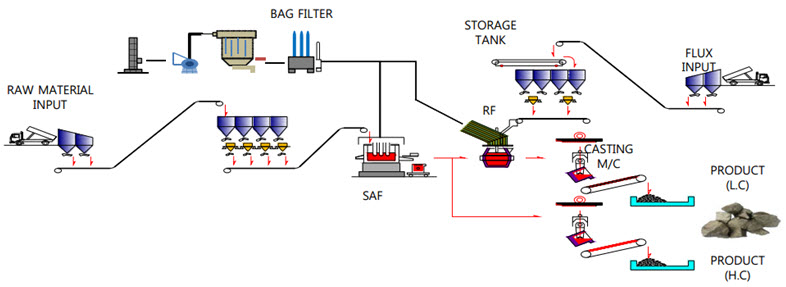
Figure 1: Basic process diagram of ferro-alloy plant
Technical Features
Key technical elements include:
- Hydraulically controlled electrode column system
- Automated tapping and mud-gun machine systems
- Optimized material charging mechanism
- Water-cooled shell cover
- Flexible electrical compositions for single-phase and three-phase operations
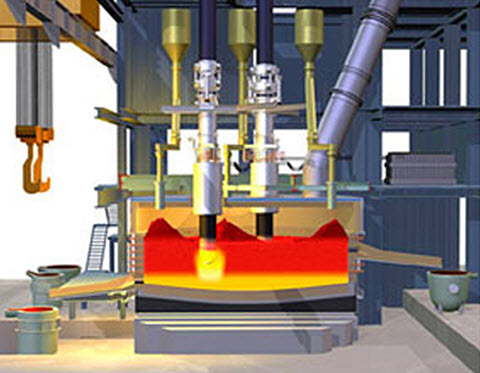
Figure 2: Schematic illustration of SAF operation
System Advantages
The SAF system provides several significant benefits:
- Client-focused furnace engineering
- Guaranteed equipment quality
- Simple and safe maintenance procedures
- High process efficiency at low energy consumption
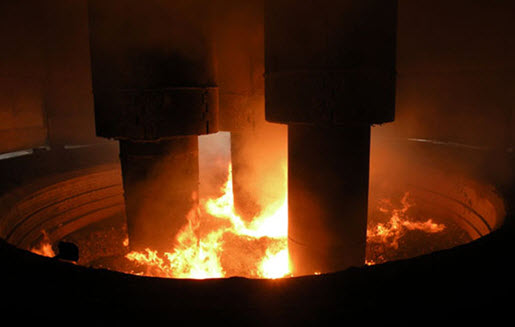
Figure 3: Submerged Arc Furnace