Abstract
Hot cracking represents a significant threat to weld integrity, manifesting as liquid films along grain boundaries during welding processes. This phenomenon can be categorized into hot cracking (including solidification cracking, liquation cracking, and weld metal liquation cracking), warm cracking (encompassing ductility-dip cracking, reheat cracking, strain age cracking, and lamellar cracking), and cold cracking caused by hydrogen-assisted mechanisms. The article examines quantification methods for hot cracking susceptibility in 304L and 316L austenitic stainless steels, emphasizing the critical role of phosphorus and sulfur content. Results demonstrate that hot cracking susceptibility increases markedly when P and S contents exceed 0.015%, with optimal sulfur ranges between 0.005-0.030% for acceptable penetration in both steel types.
Introduction to Hot Cracking in Welding
Hot cracking poses a serious threat to weld integrity and represents one of the most challenging defects encountered in welding operations. This phenomenon is characterized by the appearance of liquid films along grain boundaries or at other locations within the material structure. Understanding the mechanisms behind hot cracking is essential for developing effective prevention strategies and ensuring reliable welded joints.
While some weld metal hot cracking theories originated from casting processes, it is crucial to recognize that casting and welding processes have significant differences, particularly in terms of time and length ratios. The cracking during welding can be attributed to the effect of tensile stresses on an inadequately developed dendritic network in the weld metal and heat-affected zone (HAZ).
Classification of Cracking Types in Welding
Hot Cracking Mechanisms
Hot cracking is fundamentally related to the presence of liquid films along grain boundaries or at other structural locations. This type of cracking can be divided into three primary categories:
- Solidification cracking occurs in the weld metal when liquid films form along solidification grain boundaries during the cooling process. This type of cracking is considered the most deleterious and is more widely observed than other cracking types.
- Liquation cracking develops in the heat-affected zone where partial melting occurs along grain boundaries. This phenomenon results from the localized melting of low-melting-point constituents or segregated elements.
- Weld metal liquation cracking represents a combination of the previous two mechanisms, occurring when liquation takes place within the weld metal itself.
Warm Cracking Categories
Warm cracking encompasses several distinct mechanisms that can appear either during the welding process or after post-weld heat treatment. These include ductility-dip cracking, which occurs in the temperature range where the material exhibits reduced ductility; reheat cracking, which develops during subsequent heating cycles; strain age cracking, caused by the interaction of strain and aging processes; and lamellar cracking, which occurs in the through-thickness direction of rolled steel products.
Cold Cracking Characteristics
Cold cracking develops at room temperature due to the presence of hydrogen and hydrogen-assisted cracking mechanisms. This type of cracking typically occurs hours or days after welding completion and is influenced by factors such as hydrogen content, residual stresses, and material microstructure.
Solidification Cracking Mechanisms and Characteristics
Hot cracking specifically refers to cracking that occurs during welding, casting, or hot working at temperatures close to the material's melting point. The cracking phenomenon is known to occur both above the liquidus temperature, termed supersolidus cracking, and in the solid state, called subsolidus cracking.
The classification system developed by Hemsworth et al. (1969) categorizes the various types of hot cracks encountered in stainless steel weldments. Supersolidus cracking manifests as solidification cracking in the presence of a liquid phase in the fusion zone, or as liquation cracking in the heat-affected zone where grain-boundary melting occurs.
Solidification cracking results from the simultaneous presence of two critical factors: depressed solidification temperature liquid films along solidification sub-grain boundaries (SSGBs) or solidification grain boundaries (SGBs) in the fusion zone, and weld restraint resulting from both intrinsic and extrinsic sources.
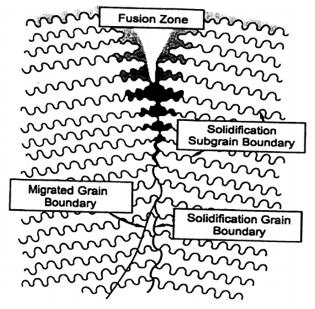
Figure 1: Schematic representation of interfaces that may exist in single-phase weld metal following solidification.
Figure 1 illustrates the boundary types that can exist in the fusion zone of fully austenitic materials during solidification as described by Lippold et al. SSGBs represent the boundaries between adjacent cells or dendrites with similar orientation, while SGBs are boundaries formed when packets of subgrains intersect. A solidification crack forms when liquid films along SSGBs and/or SGBs rupture during the solidification process.
Quantification of Hot Cracking Susceptibility in Austenitic Stainless Steels
Hot Crack Sensitivity Formula and Parameters
The quantification of hot cracking susceptibility (HCS) for various specifications of types 304L and 316L stainless steels can be accomplished using the following formula:
Hot Cracking Susceptibility (HCS) = (S + P + Si/25 + Ni/100) × 10³ / (3Mn + Cr + Mo + V)
Where:
- S = Sulfur content (%)
- P = Phosphorus content (%)
- Si = Silicon content (%)
- Ni = Nickel content (%)
- Mn = Manganese content (%)
- Cr = Chromium content (%)
- Mo = Molybdenum content (%)
- V = Vanadium content (%)
For optimal results, it is advisable to maintain chemical composition within the following parameters: sulfur content below 0.035%, nickel content below 1.0%, manganese content above 0.8%, carbon content below 0.15%, and a manganese-to-sulfur ratio greater than 35.
This hot crack sensitivity formula considers the complex interactions between various alloying elements and their influence on the material's susceptibility to hot cracking. The formula demonstrates that elements in the numerator (S, P, Si, Ni) increase hot cracking susceptibility, while elements in the denominator (Mn, Cr, Mo, V) improve hot cracking resistance. This quantitative approach enables engineers to predict and compare the relative hot cracking susceptibility of different steel specifications.
Analysis of Hot Cracking Susceptibility Results
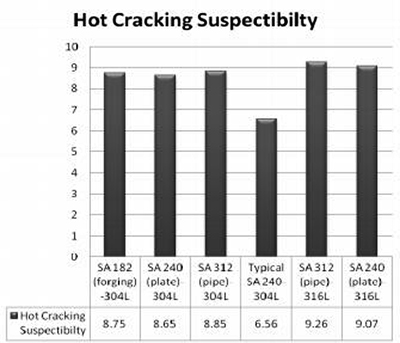
Figure 2: Calculated HCS values for various specifications of types 304L and 316L using composition extremes
The calculated values of hot crack sensitivity for given specifications reveal significant variations between different steel grades. Results demonstrate that HCS for typical SA240-304L is found to be the lowest, while SA 312 (pipe) 316L exhibits the maximum hot cracking susceptibility.
Hot cracking susceptibility increases markedly when phosphorus and sulfur contents exceed 0.015%. The lowest HCS value of 0.053 is observed for compositions with minimal phosphorus and sulfur contents, directly illustrating the significant effect of P+S on hot crack sensitivity. As the combined phosphorus and sulfur content increases, the hot cracking susceptibility correspondingly increases.
Optimal Composition Guidelines
The sulfur range should be maintained between 0.005 to 0.030% for acceptable penetration in both 304L and 316L steel types. Increasing the nitrogen content improves the resistance to hot cracking in those types of 304L and 316L steels that contain no niobium, as nitrogen-containing steels generally exhibit enhanced hot cracking resistance.
The relationship between chemical composition and hot cracking susceptibility emphasizes the importance of careful alloy design and composition control during steel production. Understanding these relationships enables welding engineers to select appropriate materials and develop welding procedures that minimize the risk of hot cracking.
Prevention Strategies and Best Practices
Effective hot cracking prevention requires a comprehensive approach that addresses both material selection and welding process parameters. Control of chemical composition represents the primary strategy for minimizing hot cracking susceptibility. Maintaining low levels of phosphorus and sulfur while optimizing the manganese-to-sulfur ratio significantly reduces the risk of hot cracking.
Welding procedure development should consider factors such as heat input, welding speed, and cooling rates to minimize the formation of liquid films along grain boundaries. Proper joint design and fit-up procedures help reduce restraint-induced stresses that contribute to hot cracking formation.
Conclusion
Hot cracking sensitivity in welding represents a complex phenomenon influenced by multiple factors including chemical composition, thermal cycles, and mechanical restraint. The quantification methods presented for 304L and 316L austenitic stainless steels provide valuable tools for predicting and preventing hot cracking in welded structures. Understanding the relationships between alloying elements and hot cracking susceptibility enables engineers to make informed decisions regarding material selection and welding procedure development, ultimately ensuring the production of high-quality welded joints with enhanced structural integrity.