Abstract
This article examines the two primary methods of ferro-alloy production: carbon-based smelting and metallo-thermic reduction. Carbon-based smelting in submerged arc furnaces is typically used for bulk ferro-alloy production, while metallo-thermic reduction employs metals like aluminum or silicon for specialized, high-grade alloys with lower carbon content. The article details the submerged arc process, including raw material preparation, furnace operation, and the conversion of electrical energy to heat. It also explores the exothermic process used for high-grade alloys, explaining how silicon and aluminum reduction create various specialized ferro-alloys with distinct properties and applications in steel manufacturing and other industries.
Introduction to Ferro-alloy Classification
Ferro-alloys are classified into two main groups: bulk ferro-alloys and special ferro-alloys. Bulk ferro-alloys are produced in large quantities using electric arc furnaces and are used exclusively in steel making and iron foundries. Special ferro-alloys, while produced in smaller quantities, have growing importance and more varied applications across industries.
Production Methods for Ferro-alloys
Ferro-alloys are primarily produced through two distinct methods. The first method involves carbon reduction with electric energy in a "Submerged Arc Furnace" through a smelting process. The second method utilizes metallo-thermic reduction with metals, typically aluminum or silicon. Each method serves different purposes in the ferro-alloy industry, with the former generally used for bulk production and the latter for specialized alloys with lower carbon content.
The Submerged Arc Furnace Process
The submerged arc process represents a sophisticated reduction smelting operation. The reactants include metallic ores (ferrous oxides, silicon oxides, manganese oxides, chrome oxides, etc.) and carbon-source reducing agents. These reducing agents typically take the form of coke, charcoal, high- and low-volatility coal, or wood chips. In some cases, limestone is added as a flux material to facilitate the smelting process.
Raw materials undergo thorough preparation before entering the furnace. This preparation includes crushing, sizing, and sometimes drying, after which they are conveyed to a mix house for precise weighing and blending. The processed materials are then transported to hoppers positioned above the furnace using conveyors, buckets, skip hoists, or specialized cars.
The material mix is gravity-fed through a feed chute into the furnace either continuously or intermittently as required by the production process. In the high-temperature reaction zone, the carbon source reacts with metal oxides to form carbon monoxide while simultaneously reducing the ores to base metal.
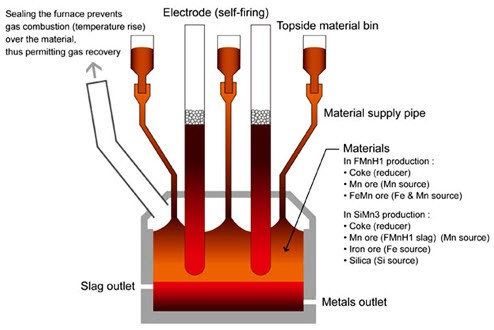
Figure 1: Electric furnace used in the submerged arc furnace process
Electric Arc Furnace Technology
Smelting in an electric arc furnace converts electrical energy into heat in a highly efficient manner. When alternating current is applied to the electrodes, it causes current to flow through the charge between the electrode tips. This creates a reaction zone capable of reaching temperatures up to 2000°C (3632°F). As the alternating current flows, the tip of each electrode continuously changes polarity. To maintain consistent electric load distribution, electrode depth is automatically adjusted using mechanical or hydraulic systems.
Exothermic (Metallothermic) Process
The exothermic process is primarily employed to produce high-grade ferro-alloys with low carbon content. The intermediate molten alloy used in this process may come directly from a submerged electric arc furnace or from another heating device. During the process, silicon or aluminum combines with oxygen in the molten alloy, resulting in a significant temperature increase and strong agitation of the molten bath.
Various specialized ferro-alloys are produced through different reduction methods. Low- and medium-carbon content ferrochromium (FeCr) and ferromanganese (FeMn) are produced using silicon reduction. Aluminum reduction is utilized to produce chromium metal, ferrotitanium, ferrovanadium, and ferrocolumbium. For producing ferromolybdenum and ferrotungsten, a mixed alumino/silico thermal processing approach is employed. Although aluminum is more expensive than carbon or silicon, it produces purer products.
Low-Carbon Ferrochromium Production
Low-carbon (LC) ferrochromium production follows a specific process. Initially, chromium ore and lime are fused in a furnace. A precisely measured amount is placed in a ladle (ladle No. 1), followed by the addition of a known amount of intermediate grade ferrochromesilicon. The resulting reaction is extremely exothermic and liberates chromium from its ore, producing LC ferrochromium and a calcium silicate slag.
This slag, which still contains recoverable chromium oxide, undergoes further processing in a second ladle (ladle No. 2). Here, it reacts with molten high-carbon ferrochromesilicon to produce intermediate-grade ferrochromesilicon. Exothermic processes typically take place in open vessels and may generate emissions similar to the submerged arc process for brief periods during the reduction process.