Abstract
Maraging steels are a special class of low‐carbon ultra‐high‐strength steels which are produced by precisely controlling the amounts of nickel and manganese in the finished material.
Depending on the variation in these two important elements it is possible to make gains in various key characteristics of the finished product including superior hardness properties.
Maraging steels are a special class of low‐carbon ultra‐high‐strength steels. The word “maraging” steel derives from the underlying strengthening mechanisms, namely, (a) transformation of the face centered cubic high temperature austenite phase of such alloys into cubic martensite combined with (b) the subsequent age hardening of this as-quenched material, hence, mar(tensite)-aging.
A variety of maraging alloys were developed in the past, and the classical representatives of this steel family are the so‐called 18 wt.% Ni maraging steels. However, these steels contain high amounts of expensive alloying elements, cobalt in particular but also nickel, and much effort has been made to develop cheaper variations such as cobalt‐free grades. Mn is cheaper than Ni, and Fe–Mn alloys feature transformation characteristics which are similar to Fe–Ni alloys and result in the formation of lath martensite under most cooling conditions. Ternary Fe–Mn–Ni alloys also exhibit considerable age‐hardening, similar to that of 18 wt.% Ni maraging steels . Hence, to further reduce material costs it was attempted to replace Ni partially or fully with Mn.
In the study of V. M. Kardonskii, M. D. Perkas is shown investigation of the structure and properties of steel containing different amounts of nickel and manganese. Figure 1 shows the influence of Ni and Mn on the hardness of martensite after heating (tempering). The martensite in the Fe + 16% Ni steel loses some of its hardness during heating at 350-500°C. Partial replacement of the nickel with manganese (in a 2 : 1 ratio) increases the hardness of martensite; the degree of hardening increases with increasing concentrations of manganese. The largest increment of hardness (HV 190) occurs in steels containing 6% Ni and 5% Mn. Further replacement of nickel with manganese also decreases the hardness of the Fe + 8% Mn steel and there is no increase in hardness during heating (see Figure 1). Thus, the presence of nickel is necessary for an effective increase in hardness during aging.
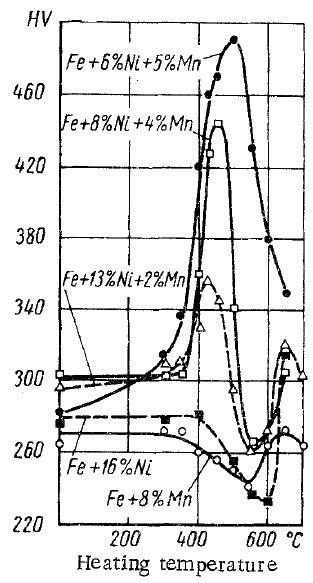
Figure 1: Dependence of hardness on the heating temperature for steels with different Mn concentrations
A more detailed investigation of the variation of the mechanical properties as the result of heating was made with steels containing 16% Ni and 2% Mn (Figure 2). The yield strength of the steel increases after heating at 350-450°C. Heating at higher temperatures decreases the yield strength, which reaches its minimum values (52 kg/mm2) after heating at 600°C. Such a sharp decrease of the yield strength is due to the reverse α→γ transformation occurring at 550-600°C. The newly formed γ-phase is highly stable with respect to the subsequent γ→α transformation.
After cooling, a considerable amount of the γ-phase remains in the structure and this leads to a considerable decrease of the effect of aging and to a decrease of the yield strength. At higher temperatures the degree of stability of the γ-phase decreases and the yield strength increases sharply. Unlike the yield strength, the ultimate strength increases somewhat instead of decreasing as the result of heating at 550-600°C because during testing the γ→α transformation occurs under the influence of plastic deformation. The resulting martensite contains a large number of structural defects, and this leads to additional hardening.
It should be noted that in this steel, because of the small concentration of Mn, the increase in strength as the result of aging is small. The ductility characteristics (δ, ψ) and the impact strength change little after aging. In steels with higher Mn concentrations the strengthening resulting from aging is much more significant and is accompanied by a considerable decrease of ductility and impact strength.
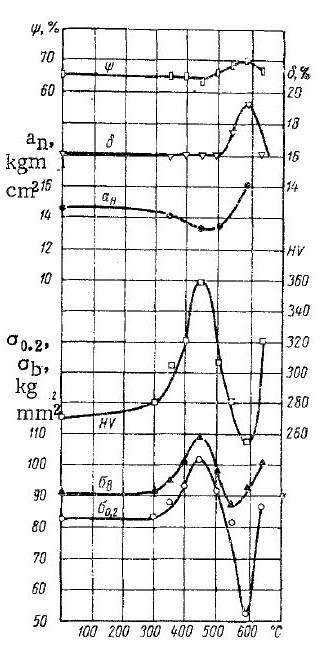
Figure 2: Dependence of the mechanical properties on the heating temperature of the steel with 16% Ni and 2% Mn. [σ0.2-Tensile stress, σB-Tensile stress, δ-elongation, ψ-reduction]