Abstract
Explosive welding has a firm reputation for being an effective technique to join metals plates, often of dissimilar materials with resulting high bond strength.
Explosive welding techniques can differ and depending on the variables of the application can include parallel explosive welding, multi-layer explosive welding, or even a new area of research underwater explosive welding.
In recent years, with the fast maturity of explosive welding process, its application fields expand constantly. Explosive welding technique for materials that are hard to melt like rare metals, such as zirconium and titanium, and amorphous alloy has been improved. New processes came out constantly, such as explosive welding under water, thermal explosion, and explosive welding and rolling. All these enrich and develop explosive welding process greatly.
Parallel explosive welding process. Common parallel explosive welding equipment is shown in Figure 1, in which the base plate is placed on sand stone, and a certain gap is left between the two plates with a spacer supporting the flyer plate. The flyer plate and the base plate are parallel to each other. Explosive and detonator are set on the flyer plate.
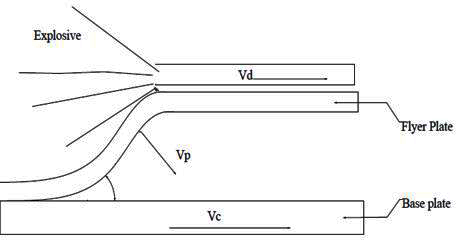
Figure 1:Explosive welding parameters
Multi-layer explosive welding process. The equipment in multi-layer explosive welding is similar to that of common parallel explosive welding. Their only difference is it has two flyer plates, not one. After the detonation of the explosive, the two flyer plates hit the base plate at the same time and the three plates then are cladded together. Usually, multi-layer explosive welding is used to weld rare metal materials, so it is widely used in high-tech field. Brittle intermediate compounds will be formed in the bonding interface of rare metal, which will affect the service performance. Brittle intermediate compounds will be reduced by using layered composite method or middle layer (tantalum), so an ideal rare metal composite plate will be got.
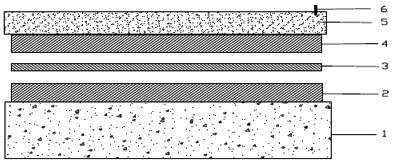
Figure 3:Schematic diagram of Multi-layer explosive welding set-up 1 basement, 2 steel plate, 3 titanium plate, 4 Zr-2 alloy plate, 5 explosive, 6 detonator
Underwater explosive welding process. Because of its special working environment and distinctive features, underwater explosive welding has become a new research field. In foreign countries, underwater explosive welding has been used successfully in the repair and connection of underwater pipelines. Japanese K.Hokamoto and co-workers[4] successfully welded Al/Zirconia ceramic, tungsten/Cu, amorphous alloy/steel and other composite materials, meeting the requirement for bonding strength and comprehensive properties by parameter optimization. In China, Ke-qiang Chen and co-workers have done a lot of research on underwater explosive welding and they have successfully made a underwater explosive welding of a steel pipe with the external diameter of 80 mm and the wall thickness of 8 mm. At present, there are three kinds of successful underwater explosive welding in research and practice at home and abroad: local drainage method, gapless method, and regulated underwater shockwave method, and their assemblies are shown in the Figure 4. Local drainage method can get the best effect and gapless method the worst. It is worth to point out that Hokamato and co-workers proved by numerical simulation and experiment study that even distribution of underwater impact load and interface wave can be got if using explosive of high strength and placing the explosive in a linearly increasing way in regulated underwater shockwave method.
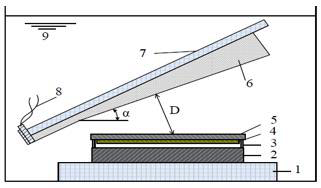
Figure 4:The method of regulated underwater shockwave 1 foundation, 2 base plate, 3 gap, 4 flyer plate, 5 cover plate, 6 explosive, 7 reflection thick plate, 8 detonation, 9 water
In the paper of Yong Yu, Honghao Ma, Kai Zhao, Zhaowu Shen, Yangfan Cheng study of underwater explosive welding of aluminum 1060 and carbon steel Q235 was carried out with different explosive loads. The impact pressures between the parent and flyer pipes were tried being got in different experiments. To study the bonding interfaces the micro-structural features of the interfaces were investigated. The following conclusions can be drawn:
a) All of the bimetallic pipes manufactured have a smooth inner surface, which means the new welding system can successfully eliminate the ablation phenomenon in aluminum pipes.
b) The impact pressure between the parent and flyer pipes increases along the detonation direction.
c) The explosive welding window of the Al-Steel combination is too narrow to obtain different bonding interfaces in the same experiment.
d) The backscattering electron images show the bimetallic pipe manufactured using Explosive Cord 2 has a poor bonding interface, whereas the one using Explosive Cord 3 has an irregular wavy interface, between a micro and small wavy interface, which is one of the best bonding forms with high bonding strength.
Explosive welding and rolling process. Composite plate production process of explosive welding and rolling can conquer shortage of explosive welding and produce ultrathin metal composite materials of large size and with low cost, meeting requite for a composite plate and avoiding adverse effect of placing explosive in a large scale, so it has a promotion effect on scale production of explosive welding in low harm condition. According to characteristics of material and processing requirement, rolling of explosive composite plate can be divided as: cold rolling, hot rolling, and hot rolling and cold rolling. Chang-gen Shi and co-workers studied on the explosive welding and rolling of 304/A36 and other materials. They got a stainless steel composite plate, 0.1mm ≤ δ ≥ 2mm in the complex layer thickness, 2m in width, 20m in length. Yuan-mou Zheng and co-workers found that a layer of white or black zonal material appeared on Ni/stainless steel interface, which components was solid solution that did not affect binding performance, and hard brittle intermetallic compound that affected interface quality appeared on the Ni/Ti composite plate.