Abstract
Due to an excellent refining capacity and heat source flexibility, electron beam melting is most effectively used under high vacuum and for production of ultra-pure refractory and reactive materials.
The process works by the electron beam or beams, sweeping the surface of the metal ingot in a rotational movement to distribute kinetic energy as evenly as possible.
Electron beam melting is distinguished by its superior refining capacity and offers a high degree of flexibility relating to the heat source. Thus, it is ideal for the remelting and refining of metals and alloys under high vacuum in water-cooled copper molds. Today the process is mainly employed for the production of refractory and reactive metals (tantalum, niobium, molybdenum, tungsten, vanadium, hafnium, zirconium, titanium) and their alloys. It plays an important role in manufacturing of ultra-pure sputtering target materials and electronic alloys and the recycling of titanium scrap.
Two variants, employing one or more electron guns, are in use today:
- The discontinuous "Drip Melting" technique, in which a primary ingot is melted by the electron beam(s), the resulting metal droplets forming a secondary ingot which solidifies in a water-cooled copper crucible. Mostly, repeated remelting of the first melt ingots is required to achieve the final quality. For repeated remelting, vertical feeding is applied.
- The continuous "Electron Beam Cold Hearth Refining" process, involving a purification and inclusion separation stage in a cold hearth furnace before ingot formation (Figure 1).
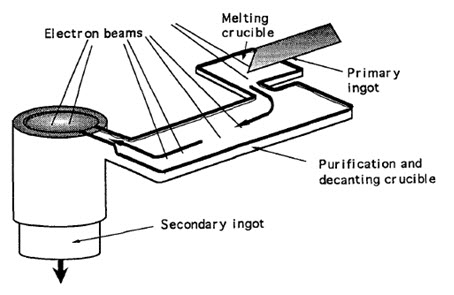
Figure 1: Schematic diagram showing the principle of the Electron Beam Cold Hearth Refining process
The physical phenomena specific to EB remelting are the following:
- At the point of impact of the beam, the kinetic energy of the electrons is converted to heat energy, but the backscattered electrons are responsible for high losses, whose value, which depends on the metal bombarded and the angle of incidence of the beam, represents between 30 and 50% of the incident energy in the case of titanium.
- The electron beam, which produces a spot of about one centimeter in diameter, sweeps the surface of the liquid metal, situated above the ingot, and moving in a rotational movement about the axis of symmetry with a radial movement perpendicular to the axis. Widely variable energy distributions can therefore be obtained at the surface of the metal. The high scanning frequency used with modern electron guns enables the energy distribution to be assumed to be quasi-stationary, to a first approximation.
- The temperature gradients in the vicinity of the pool surface, created by the impact of the electron beam, can be extremely high, and can lead to variations in surface tension which give rise to the Marangoni effect.
- Because of the high vacuum in the furnace chamber, volatilization phenomena can be important and cause difficulties in the control of alloy composition.
Advantages and Disadvantages
Electron Beam Welding has become a vital technology in many industries. Some of its benefits include:
- Ability to achieve a high energy level in a narrow beam.
- Vacuum melt quality can yield high strength properties of the material.
- Vacuum environment eliminates impurities such as oxides and nitrides.
- Permits welding in refractory metals and combinations of dissimilar metals.
Electron Beam Melting benefits from all of these factors in the same way. Compared with laser sintering/melting additional benefits include:
- Higher efficiency in generating the beam of energy resulting in lower power consumption as well as lower maintenance and installation costs
- High actual overall power resulting in high build speeds
- Deflection of the beam can achieved without moving parts resulting in high scanning speed and low maintenance.
Some apparent disadvantages of electron beam technology are:
- Requires vacuum which adds another system into the process which inevitably costs money and must be maintained [Added benefit: Vacuum eliminates impurities and provides a good thermal environment for freeform fabrication]
- Electron beam technology produces X-rays while in operation [Solution: The vacuum tank shields the rays perfectly if properly designed.]