Abstract
Vapor Phase Soldering (VPS) is an advanced thermal processing method for electronics manufacturing that utilizes saturated vapor for precise temperature control and uniform heating. This technique offers superior heat transmission, minimal oxidation, and excellent temperature control compared to traditional soldering methods. The process employs specialized inert liquids and provides particular advantages for complex board architectures and heat-sensitive components. This article explores the principles, advantages, disadvantages, and equipment configuration of VPS technology, comparing it with other soldering methods used in modern electronics manufacturing.
Introduction to Vapor Phase Soldering
Vapor phase soldering, also known as condensation heating, is a direct contact process that occurs in a zone of heated, saturated vapor. The process utilizes the latent heat of vaporization when hot, saturated vapor condenses on a surface. This technology has been successfully adapted for mass reflow soldering, paint and polymer coating, and polymer fusing applications, providing precise temperature control in a clean, non-oxidizing, and non-flammable environment.
Process Principles and Methodology
The VPS process involves heating a special inert liquid to create a saturated vapor atmosphere. When the product requiring soldering is immersed in this atmosphere, the vapor contacts the product and releases its latent heat of vaporization during condensation. This results in highly efficient and uniform soldering across the entire product surface.
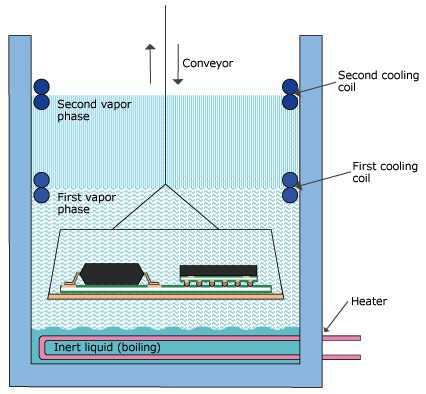
Figure 1: Vapor phase soldering method
Technical Advantages and Benefits
- Superior Heat Transfer
- Exceptionally high efficiency in heat transmission
- Uniform heating regardless of component geometry
- Independent of circuit assembly mass, color, or composition
- Temperature Control
- Precise temperature regulation through latent heat
- Component temperature never exceeds vapor temperature
- Lower processing temperatures compared to IR or hot air methods
- Environmental Protection
- Minimal oxidation of soldered sections
- Clean, non-oxidizing atmosphere
- Reduced contamination risk
- Process Efficiency
- Short processing times
- Minimal thermal stress on packages
- High reliability with reduced rework requirements
Limitations and Considerations
The primary disadvantage of VPS technology is:
- Higher operational costs compared to traditional methods
Comparison with Other Soldering Technologies
There are three types of commonly used production soldering stations:
- Wave solder systems
- Convection systems (Including three SMEMA classifications)
- Class 1 IR (radiant dominant)
- Class II IR (combination convection and IR)
- Class III (convection dominant)
- Vapor phase reflow (VPR) systems
While these systems share the basic function of heating boards above the solder's liquidous point, they differ in:
- Heating methodology
- Solder application timing and technique
- Temperature change rates
- Process control capabilities
Equipment Configuration
The standard VPS equipment configuration includes:
- Primary vapor phase chamber for batch reflow soldering
- Preheating system
- Cooling mechanism
- Secondary vapor phase for liquid containment