Abstract
Sandwich steel panels represent an advanced structural solution that balances enhanced performance with cost effectiveness for key sectors including automotive manufacturing. These innovative panels feature exceptional stiffness-to-weight ratios, superior energy absorption capabilities, and significant space-saving potential. This article examines the fundamental design principles of sandwich steel panels, explores their various core structures, and highlights their substantial advantages over conventional materials. For weight-conscious industries facing stringent performance requirements and cost constraints, sandwich steel panels offer a compelling alternative that can deliver up to 50% weight reduction while maintaining structural integrity and introducing additional benefits including thermal insulation and noise reduction.
Introduction to Sandwich Steel Panel Technology
The automotive industry faces persistent pressure to develop lightweight structural solutions that improve vehicle fuel efficiency without compromising structural performance. These design initiatives must operate within strict cost constraints, as innovations rarely succeed in the market without demonstrating both performance and economic advantages. Sandwich structures have emerged as a promising solution due to their exceptionally high bending stiffness-to-weight ratio. The fundamental design concept involves separating two flat sheets with a substantially thicker core layer of low density material (Figure 1 shows the basic sandwich structure configuration).
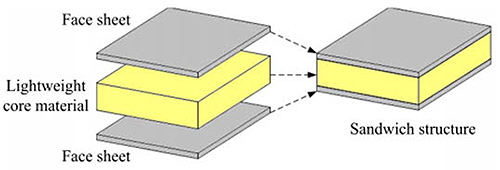
Figure 1: Basic diagram showing the layered composition of sandwich structures with face sheets and core material
For numerous applications, engineers require metal sheet properties that cannot be achieved with conventional single sheets. Sandwich structures offer diverse design possibilities that extend beyond weight reduction to include space savings, fire resistance, improved acoustic properties, and enhanced thermal performance.
Structural Composition and Mechanics
As illustrated in Figure 1, sandwich structures typically comprise two face sheets separated by a core material. In traditional sandwich design, this separation increases the panel's moment of inertia, resulting in superior bending stiffness-to-weight ratios compared to solid or monolithic plates. The face sheets primarily handle bending and in-plane loads, while the core material carries shear loads, preventing the face sheets from sliding against each other.
Types of Sandwich Panels
Sandwich panels can be broadly classified into two categories: composite sandwich and metallic sandwich panels. Composite sandwich panels incorporate non-metallic components such as fiber-reinforced polymers (FRP) and polyurethane foam. These are typically used as load-bearing structures in naval vessels and leisure yachts, and as non-load-bearing elements in merchant and cruise ships.
Metallic sandwich panels fall into two primary subcategories:
- Panels with metallic face plates and bonded cores (such as SPS panels)
- Panels with both metallic face plates and cores welded together
Steel Sandwich Panel Core Geometries
Steel sandwich panels can be differentiated based on their core structures:
- I-core with straight webs
- O-core with rectangular beams
- Vf/V-core with hat or corrugated sheets
- X-core with two hat profiles
Additional profiles such as C, U, or Z can also function as core materials. Figure 2 illustrates these various core geometries suited for steel sandwich structures.

Figure 2: Five different core geometries for steel sandwich structures including I-core, O-core, V-core, and X-core configurations
Research indicates that properly designed sandwich structures can be 30–50% lighter than conventional steel applications while maintaining required strength properties.
Advantages of Sandwich Steel Panels
Sandwich panels offer numerous benefits across applications:
- Superior stiffness and strength-to-weight ratios
- Improved surface finish that reduces aerodynamic resistance
- Excellent thermal and acoustic insulation properties
- High energy absorption capability through various fillers and core designs
- Increased interior space and simplified equipment installation
- Competitive total costs compared to other lightweight structural solutions
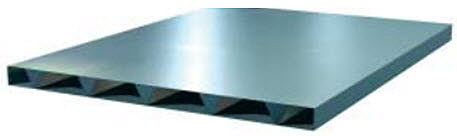
Figure 3: V-core stainless steel sandwich panel with hat sheets as a core