Abstract
Magnesium alloys are well known for light weighting specifically in transportation and mobile electronics but have production restrictions relating to formability and therefore are primarily die casted.
Magnesium alloy strip casting combines casting and hot rolling into a single step process meaning good results can be gained whilst saving on equipment, running and energy costs.
Magnesium alloys are light-weight structural metals with high specific strengths, which have been used in transportation and mobile electronics for weight-saving. However, due to their poor formability, die casting has been the most popular process for making the parts until now. But in the future, the die casting process may not meet a new demand for lighter, thinner, stronger, and more complex shape applications.
On the other hand, the demand to reduce energy consumption increased the use of light-weight alloys in the automobile industry. As the lightest structural metal with a high specific strength and Young-module, magnesium and its alloys have been widely applied in this industrial area.
Most magnesium alloy components have been produced by various die casting processes for its good casting behavior. Despite the fact that wrought flat products are more convenient to use, less than one percent of magnesium alloys are provided as sheets because wrought magnesium sheets are now still quite expensive and difficult to produce.
Therefore, the development of new forming processes for magnesium sheets is expected in order to lower the production cost and extend the application fields.
The strip casting process combines casting and hot rolling into a single step, with advantages of low equipment cost, low running cost, energy saving and space saving. The flow chart of continuous casting strip technology is shown in Figure 1.
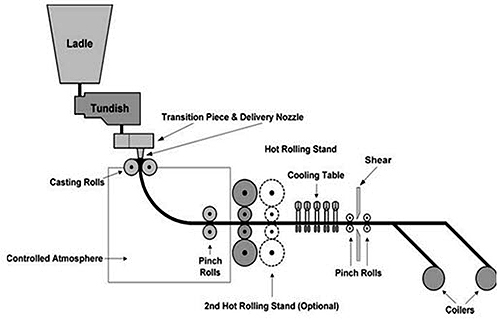
Figure 1: The continuous casting strip technology plant flow chart In the process, the tundish feeds a transition piece, which is situated just above the delivery nozzle, and the molten metal is solidified starting at the point of first metal-roll connection and ending at the end point of solidification. This near-net-shape process can produce thin strip in one step. Upon exit from the casting roll, the solidified strip is directed to a pinch roll then through a hot rolling stand. In the transition, the atmosphere is controlled to limit oxidation of the strip and the formation of scale.
Referring to the automotive sector, magnesium sheets offer new opportunities for lightweight constructions, primarily in the car body, but also in chassis, interior, and motor components. Table 1 shows a list of possible components for an automotive application which can reasonably be made using magnesium sheets. Figure 2 represents some prototypes made out of magnesium alloy AZ31.
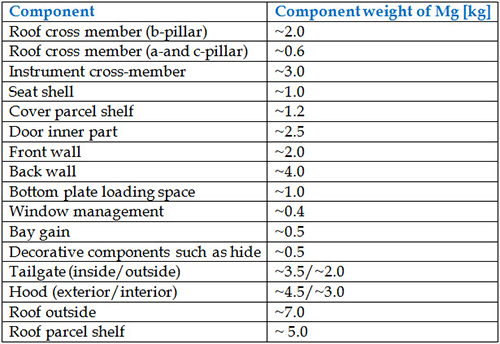
Table 1: List of possible Mg components for automotive application
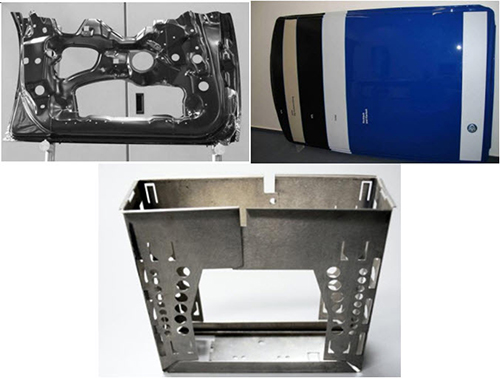
Figure 2: Inner door, car roof and radio housing