Abstract
Although not technically green in color, green sand casting is a wet molding technique using quartz sand to cast iron castings, like ductile iron castings, gray iron castings.
In order for the process to work in an optimum way, a number of key parameters such as compression strength, permeability, pouring temperature all need to be controlled and applied accurately.
Green sand casting is a common sand casting process using green sand as the molding material. Green sand does not mean sand in green color, but is a kind of wet quartz sand in the sense that it is used in a wet environment.
Green sand casting is suitable for manufacturing various cast iron castings, like ductile iron castings, gray iron castings. It is also suitable for producing some simple aluminum castings. As steel castings require larger air permeability, so it is not workable for making steel castings.
The green sand casting remains one of the most versatile casting processes due to readily available and cheap raw materials; flexibility with respect to shape, size and composition; and the possibility of recycling the moulding sand. The sand casting process starts with preparation of mould, pouring molten metal into a sand mould, allowing the metal to solidify, and then breaking away the sand mould to remove a casting product. Out of the various steps involved in the casting process, moulding and melting processes (pouring of molten metal) are the most important stages. Improper control at these stages results in defective castings.
A number of researchers and foundry engineers have carried out research in the field of green sand-casting to improve the quality of castings by adjusting the process parameters.
In the study of S.K. Tiwari et al., an attempt has been made to obtain an optimal parameter setting of green sand casting process to enhance the quality of mild steel castings by reducing the percentage of casting defects. Taguchi method of parameter design is used to set the optimal process parameters All the data required for the research has been collected from the real castings plant condition. In this experiment, a number of factors affecting the green casting process are identified such as grain size, sand composition, fluidity, metal composition, pouring time, cooling time, humidity etc..
Experimental results indicate:
1) The optimum levels of the parameters at which defect level will be minimal are: green compression strength at level 2 (1,800 g/cm2), permeability at level 2 (130), pouring temperature at level 3 (1,450ºC), mould hardness at level 2 (90), and moisture content at level 1 (2.8%);
2) From ANOVA results, parameters green compression strength, permeability, and pouring temperature are significant and parameters mould hardness, and moisture content is insignificant.
3) Percentage contribution: permeability (61.53%) has the most dominant effect on total variation and it is followed by green compression strength (21.54%) and pouring temperature (5.52%).
4) With optimal parameters setting a decrease of 14.86% in defect level has been found against the initial process parameters setting.
Advantage of green sand casting
- Least expensive
- Less distortion than in dry sand casting because no baking is required
- Flasks are ready for reuse in minimum time
- Dimensional accuracy is good across the parting line
- Less danger of hot fearing of casting compare to other type
Disadvantages of green sand casting:
- Sand control is more critical than dry sand casting
- Erosion occurrence of the mould is common in the production of large castings
- Certain metals and some castings develop defects if poured into moulds containing moisture
- More intricate casting can’t be produced
- The surface finish can deteriorate and dimensional accuracy decreases as the weight of the casting increases
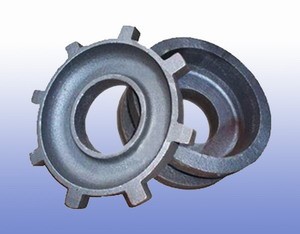
Figure 1: The Green Sand Casting products