Abstract
Cold extrusion represents a critical manufacturing process in modern industry, involving the deformation of metal materials through a die at room temperature to produce components with consistent cross-sectional profiles. This article examines the three principal extrusion methods—forward extrusion, backward extrusion, and upsetting—highlighting their distinct metal flow characteristics. Cold extrusion offers significant advantages including improved mechanical properties, precision tolerances, and absence of oxidation. The process is particularly valuable for producing a wide range of components from various metals, including challenging materials like steel and titanium.
Introduction to Cold Extrusion
Extrusion, while one of today's most significant manufacturing processes, remains a relatively recent development in metalworking history. The cold extrusion process involves forcing a billet of material through a die at room or slightly elevated temperatures, producing a continuous product with constant cross-section. This versatile technique accommodates numerous metals including lead, tin, aluminum alloys, copper, titanium, molybdenum, vanadium, and steel.
Applications and Benefits
Cold extrusion enables the production of diverse components such as collapsible tubes, aluminum cans, cylinders, and gear blanks. Parts produced through cold extrusion remain free from oxidation and typically exhibit enhanced mechanical properties due to severe cold working, provided the billet temperature stays below the material's recrystallization point.
Cold Extrusion Technology
Cold extrusion technology allows manufacturers to form parts to precise dimensions by manipulating metal at room temperature into specially designed dies. The process requires sufficient force to exceed the yield strength of materials like stainless steel, ensuring plastic deformation occurs and enabling the metal to completely fill die cavities with extremely tight tolerances.
Primary Cold Extrusion Methods
Although numerous variations exist in cold extrusion operations, all are fundamentally based on three principal approaches:
Forward Extrusion
Forward extrusion forces metal to flow in the same direction as the descending punch and through an opening in the die to create the required shape and dimensions. This method proves especially valuable for manufacturing bolts, screws, stepped shafts, and cylindrical components.
Backward Extrusion
In backward extrusion, metal is forced to flow upwards, surrounding the descending punch. This method typically requires higher extrusion pressures, and proper slug preparation becomes more critical to successful outcomes.
Upsetting
Upsetting involves gathering metal in specific sections along the length of a bar, rod, or wire. During this process, metal flows perpendicular to the motion of the tooling. Manufacturers frequently perform upsetting in conjunction with backward or forward extrusion techniques to achieve complex geometries.
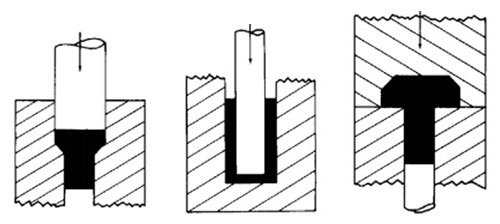
Figure 1: a) Forward extrusion b) Backward extrusion c) Upsetting
Design Considerations
Successful cold extrusion implementation requires careful attention to component design principles that accommodate material flow characteristics and tooling constraints.
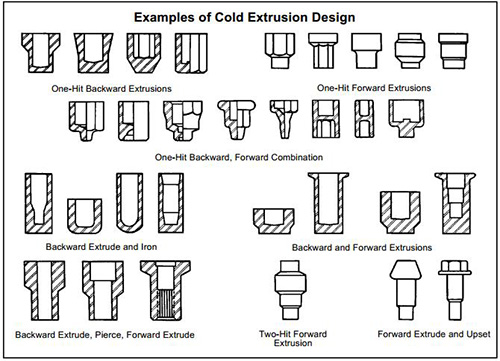
Figure 2: Multiple examples of cold extrusion design possibilities showing various component configurations