Abstract
Amorphous metal, aka metallic glass, has the potential to revolutionize the use of metals. But what makes metallic glass alloys so desirable?
Most metals have a crystalline structure, but metallic glasses are fundamentally different, giving them almost unbelievable properties, and making them desirable materials for all sorts of industries and applications.
Conventional Metals
In an ordinary alloy the atoms of the metal arrange themselves into a repeating pattern of crystals or grains with different sizes and shapes upon cooling from the liquid state. Because metals typically do not solidify into single crystals, they have inherent weaknesses.
It’s the boundaries between the grains that are the weak spots, and under high enough stress or temperature the grains will slide past each other, resulting in deformation. In addition, extra atoms are often present within the grains, causing planes of distortion called dislocations. Dislocations easily move through metal that is under stress, again causing deformation. Grain boundaries and dislocations greatly lower a metal’s strength compared to its theoretical maximum.
Casting of conventional metals also requires more manufacturing steps than bulk metallic glass. Conventional metals shrink significantly as they cool in the mold from liquid to solid form and often develop surface roughness. Secondary steps are usually required to get at the final product, such as grinding and polishing.
As mentioned earlier, Bulk Metallic Glasses (BMG) have an amorphous structure and possess desirable mechanical, magnetic and corrosion properties, such as high yield stress, low magnetic losses and high corrosion resistance. A glass-forming alloy has the potential to become amorphous provided the solidification rate is rapid enough to avoid crystallization.
However, traditional manufacturing techniques, such as casting, limit the cooling rates and sizes of components due to the relatively slow heat conduction in the bulk material. With Additive Manufacturing (AM) on the other hand, it is possible to produce BMGs, as the melt pool is very small and solidification can be achieved very rapidly, bypassing crystallization. Yet, crystals may form by devitrification (crystal formation caused by heating of the amorphous phase) because of thermal cycling as new layers are added over previous layers. Simulation of the process will improve the understanding of glass formation during AM and aid the development of process parameters to control the level of devitrification.
Metallic glasses
The structure of metallic glass is very different from that of conventional metals. As mentioned, metallic glasses are non-crystalline solid materials with an amorphous structure that differs from traditional crystalline solids. The atoms are not ordered in periodic lattice structures and appear to be randomly distributed, as illustrated in Figure 1. Because of the lack of orientation, metallic glasses have no grains or grain boundaries. Grain boundaries are what make a crystalline material susceptible to corrosion and wear. Thus, metallic glasses possess significantly higher yield strength, and better resistance to corrosion and wear compared to their crystalline counterparts. The areas of application are many, but medical equipment and implants are two important areas. For example, a surgical blade made of metallic glass can be extremely sharp and long lasting. Microscopic geared engines for advanced medical equipment and micro-factories can also be made very small and incredibly wear resistant.
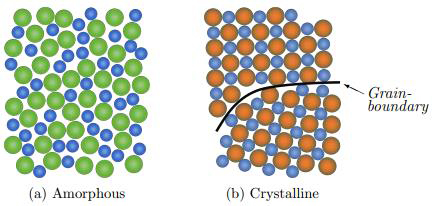
Figure 1: Illustration of the atomic structure of a binary alloy in the crystalline (b) and amorphous (a) state
The first amorphous metal was synthesized back in 1960 by Duwes et al. by rapidly solidifying a gold-silicon alloy by shooting small droplets of molten metal on a cold copper plate, using the gun technique. The cooling rate was estimated to be ∼106 K/s and the thickness of the splatter was only around 50 µm. The first iron-based metallic glass, made of 80% iron and 20% boron, was synthesized in thin ribbons in 1976 by Davis. During this early time of amorphous metals, at least one dimension of a sample was limited to a very small size due to the extreme cooling rate required to avoid crystallization. The extraction of heat from the melt is limited by conduction within the material, so large components would suffer from an insufficient cooling rate. The driving force to synthesize thicker samples led to the formation of Bulk Metallic Glasses (BMG).
Why are metallic glasses important?
Unique properties:
- High hardness and wear resistance
- Excellent corrosion resistance
- High strength-to-weight ratio
- Superior elastic limit
- Superplasticity at high Temperatures
- Good soft magnetic properties
Applications
- Thermoplastic forming of metals, processed like polymers
- Sports equipment
- Sensors/actuators
- Electronic casings
- Industrial coatings
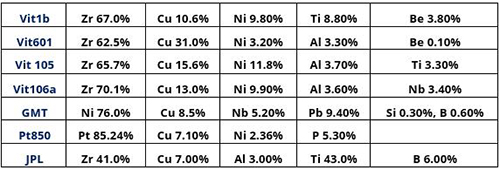
Table 1: Some BMG alloys
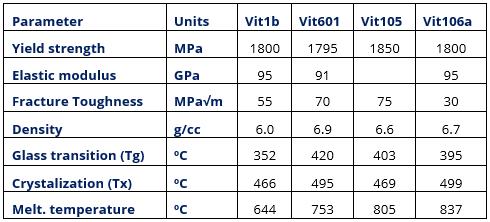
Table 2: Properties of some BMG alloys
Figure 2 shows several BMG parts sitting on a ~1 m2 plate of die-cast Vitreloy 1 (parts fabricated by Liquidmetal Technologies and Howmet). The parts shown include a golf club driver, an iron, a USB hard drive case, a camera body, an optical device, eight ingots of feedstock, and a 12 mm diameter rod, all from the alloy Vitreloy 1 (trade name LM1).
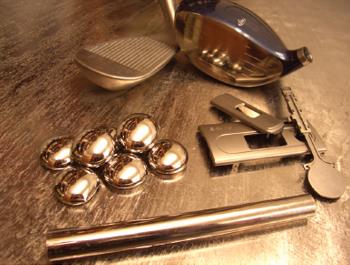
Figure 2: Examples of bulk metallic glass hardware, including golf clubs, electronic casings, optical hardware, ingots, 12 mm diameter rod, and large plate (under the samples).