Abstract
Electromechanical testing instruments are widely used throughout the metals industry for evaluating important properties such as Tensile strength, Young’s modulus of elasticity, yield strength, Poisson’s ratio, elastic and plastic deformation, and strain hardening behavior.
The fatigue life will change for each specimen because it’s dependent on the magnitude of the fluctuating stress, the specimen geometry and testing conditions.
Steel, aluminum, iron, titanium, tin, copper and zinc and their alloys are metals that are mostly used for the production of appliances, devices, machinary and buildings. The wide spectrum of metal properties also determines the essential need for a wide range testing.
Tensile testing is the most commonly used test to determine mechanical properties of metals. Electromechanical testing instruments are widely used throughout the metals industry for evaluating important properties such as Tensile strength, Young’s modulus of elasticity, yield strength, Poisson’s ratio, elastic and plastic deformation, and strain hardening behavior.
Also many components such as springs, pipes, containers, etc. rely on compression tests that provide data on force versus deformation. The mechanical requirements for many metals are typically specified as “tensile strength”, “yield point” and “%elongation” in addition to other properties.
The strength of a material under tension has long been regarded as one of the most important characteristics required for design, production quality control and life prediction of industrial plants. The uni-axial tensile test is the primary method used for quality control and certification of virtually all metallic materials produced by casting, rolling and forging processes.
Fatigue Testing
Fatigue is the loss of strength and energy resulting from physical work. Fatigue testing is the applying of continuous loading to a test specimen in order to determine how it performs under repeated vibration or strain conditions. The fatigue life of the specimen is the number of cycles of fluctuating stress and strain that a specimen can withstand before failure occurs.
The fatigue life will change for each specimen because it’s dependent on the magnitude of the fluctuating stress, the specimen geometry and testing conditions. Fatigue behavior is classified into two domains, high cycle and low cycle fatigue. High cycle fatigue is associated with low strain conditions and a fatigue life greater than 104 to 105 cycles.
High cycle fatigue creates stress levels that are under the yield strength of a given material. It results from vibrations or strain from high cycles that can reach thousands of cycles per second, at frequencies that can be induced by many sources. Low cycle fatigue is associated with high vibration or strain conditions. Low cycle fatigue failure generally occurs in a relatively small number of fatigue cycles.
Endurance limit is the limit below which repeated stress does not induce failure, theoretically, for an infinite number of cycles of load.
Tensile or axial fatigue testing is a common method used to determine mechanical properties of metals, such as Young’s modulus, tensile strength, modulus of elasticity, and other tensile properties. Tensile loading is used to determine how a material will behave under axial stretch loading. In tensile fatigue testing a continuous small axial load is applied constantly so that the fatigue limit of a specimen can be determined.
As an illustration of tensile fatigue testing, tables 1 and 2 and figures 1-6 presents the fatigue endurance results of some non-ferrous materials.
The investigated materials consist of five alloys of alpha brass, three of which had been hardened with nickel silicide and one alloy each of nickel silver, phosphor bronze and Everdur.
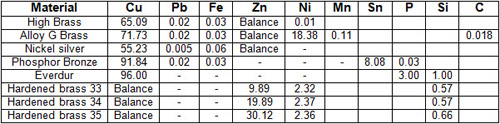
Table 1: Average chemical analysis of materials
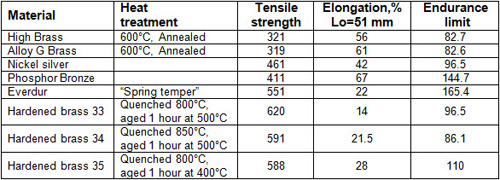
Table 2: Material properties
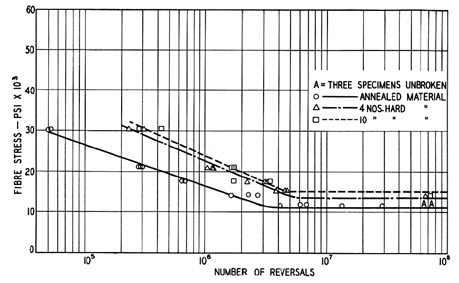
Figure 1: Relation of Fibre Stress to reversals, High Brass Sheet
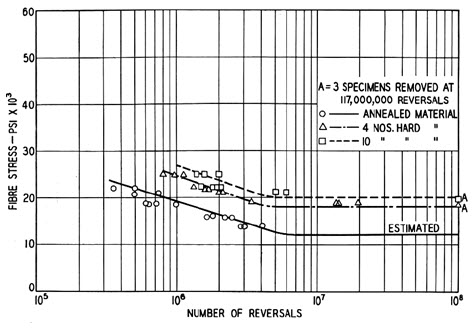
Figure 2: Relation of Fibre Stress to reversals, Alloy G Brass Sheet
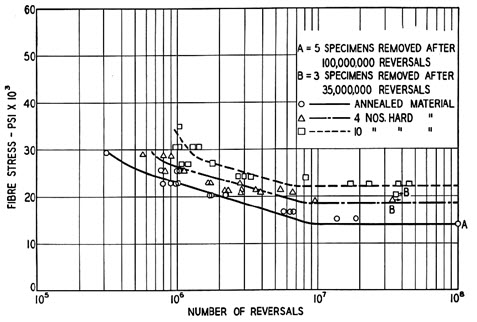
Figure 3: Relation of Fibre Stress to reversals, Alloy B Nickel Silver
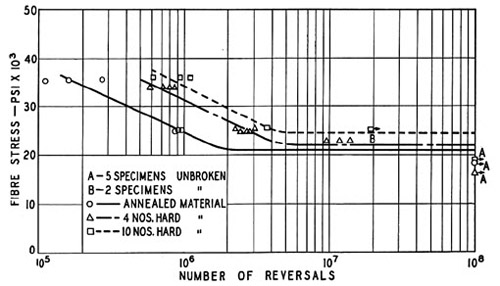
Figure 4: Relation of Fibre Stress to reversals, Alloy C phosphor Bronze
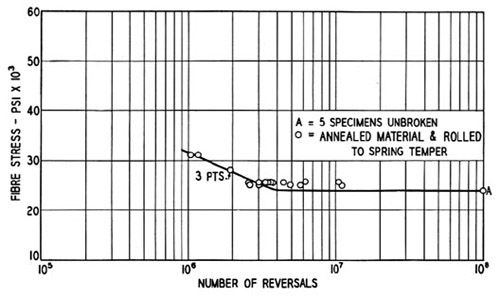
Figure 5: Relation of Fibre Stress to reversals, Everdur alloy spring temper
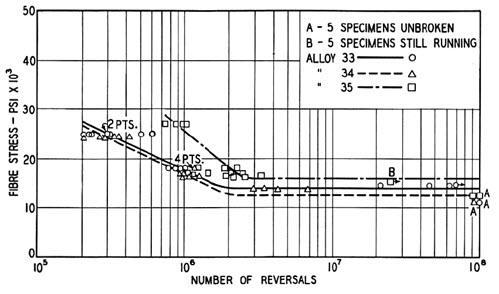
Figure 6: Relation of Fibre Stress to reversals, Dispersion Hardened Brasses, Alloys No 33, 34, and 35