Abstract
Tandem welding is a more recent breed of welding technologies which fit with a consistent drive to improve quality, efficiencies and cost in the process.
The main advantages of using Tandem welding are that it is highly efficient, requires minimum heat input, provides superior quality results to name but a few.
The welding process is one of the most important techniques for production of electronic components, small products, and heavy structures through all industry sectors. The process and application of welding techniques is completely wide spread, from all types of industry, through job shop outfits to highly-automated computer-controlled factories.
Therefore, the welding process has progressed remarkably in the past 30 years as a result of technological innovation aimed at increasing productivity, stabilization of weld quality and labor saving. Recently, automatization and robotization are beginning to be adopted as key technologies to secure improved productivity and consistent quality. Some novel welding processes such as twins, tandem and laser-MIG hybrid welding are developed for a higher productivity.
One of the advanced welding processes which is called the Tandem welding process involves two independent electrodes (early electrode and delayed electrode) which are arranged parallel to weld line and works by controlling them individually under separate welding conditions (current and voltage) while keeping the distance between the early and delayed electrodes at a constant (Figure 1).
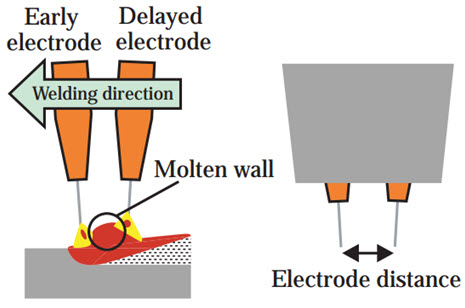
Figure 1: Tandem Welding Condition and Electrode Distance The major advantages of the Tandem Weld process are extremely high efficiency, minimum heat input, excellent weld seam quality and extraordinarily high deposition rate.
Applications
Automated welding
Thin to thick materials
Advantages
Extremely high weld speed
Very high deposition rates
Excellent weld quality, minimum risk of pore formation
Low heat input
Optimum arc control
Material
Steel
High-strength steel
Aluminium
Chrome-nickel materials
Coated plate
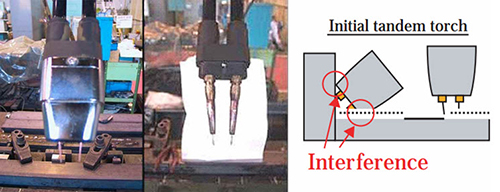
Figure 2: Initial Tandem Torch and Welding Motion
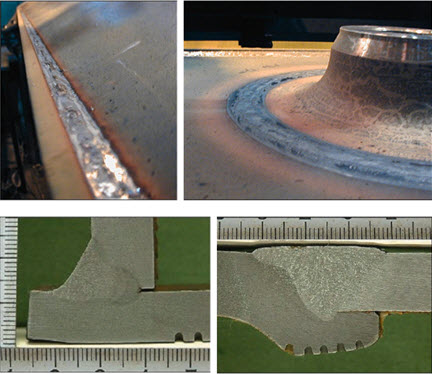
Figure 3: Quality of Tandem Welding