Abstract
Selective laser sintering (SLS) was one of the first additive manufacturing techniques, developed in the mid-1980s and was adapted over time to be applicable for practically all structural materials such as plastics, metals, glass, ceramics, and composites.
In this article we explore the SLS process and highlight some of the key advantages this technique can provide on the geometries and mechanical properties of the finish component.
Additive manufacturing, or 3D printing, is the process of turning digital designs into three-dimensional objects. It is a convenient and affordable way to make prototypes as well as finished products, making it popular with businesses, hobbyists and inventors. One of the technologies used by today's 3D printers is called selective laser sintering (SLS).
Selective Laser Sintering (SLS) is an Additive Manufacturing process that belongs to the Powder Bed Fusion family. In SLS, a laser selectively sinters the particles of a polymer powder, fusing them together and building a part layer-by-layer. The materials used in SLS are thermoplastic polymers that come in a granular form.
The History of SLS 3D Printing
Selective laser sintering (SLS) was one of the first additive manufacturing techniques, developed in the mid-1980s by Dr. Carl Deckard and Dr. Joe Beaman at the University of Texas at Austin. Their method has since been adapted to work with a range of materials, including plastics, metals, glass, ceramics, and various composite material powders. Today, these technologies are collectively categorized as powder bed fusion—additive manufacturing processes by which thermal energy selectively fuses regions of a powder bed.
How SLS 3D Printing Works
SLS 3D printers use a high power laser to fuse small particles of polymer powder.
1. Powder is dispersed in a thin layer on top of a platform inside of the build chamber.
2. The printer preheats the powder to a temperature just below the melting point of the raw material. This makes it easier for the laser beam to raise the temperature of specific regions of the powder bed as it traces the model to solidify a part.
3. The laser scans a cross-section of the 3D model, heating the powder to just below or right at the melting point of the material. This fuses the particles together mechanically to create one solid part. The unfused powder supports the part during printing and eliminates the need for dedicated support structures.
4. The build platform lowers by one layer into the build chamber, typically between 50 to 200 microns, and a recoater applies a new layer of powder material on top. The laser then scans the next cross-section of the build.
5. This process repeats for each layer until parts are complete, and the finished parts are left to cool down gradually inside the printer.
6. Once parts have cooled, the operator removes the build chamber from the printer and transfers it to a cleaning station, separating the printed parts and cleaning of the excess powder. [4] [3]
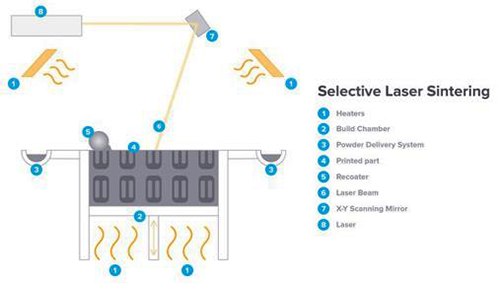
Figure 1: This schematic shows the selective laser sintering system. SLS uses a laser to sinter powdered plastic material into a solid structure based on a 3D model.
A key advantage of SLS is that it needs no support structures. The unsintered powder provides the part with all the necessary support. For this reason, SLS can be used to create freeform geometries that are impossible to manufacture with any other method.
In SLS, the bond strength between the layers is excellent. This means that SLS printed parts have almost isotropic mechanical properties.
SLS parts have excellent tensile strength and modulus, comparable to the bulk material, but are more brittle (their elongation at break is much lower). This is due to the internal porosity of the final part.