Abstract
Pyrometallurgy is the oldest technique for metal extraction from the ore and mainly involves volatilization of non-ferrous metals like zinc, lead and cadmium out of an oxidised solid mixture by means of reduction by coke or coal.
Regarding the treatment of steel mill residues, there are some key processes covered including Waelz Technology, Rotary Hearth, and PRIMUS.
Extracting metals from ores requires a number of operations: some mechanical, physical, and physicochemical known as mineral beneficiation and some chemical known as extractive metallurgy. The chemical processes can be divided for convenience as pyro-, hydro-, and electrometallurgy.
Pyrometallurgy is the most ancient technology, while hydrometallurgy is about four centuries old. On the other hand electrometallurgy is the most recent and came into existence only after the invention of the large-scale electrical generators in the mid nineteenth century. It is not surprising then that, in some cases, these new technologies are displacing the older ones gradually, either because of improved efficiency and better economics or to comply with environmental regulations.
Pyro-metallurgical processes like Waelz Kiln, Rotary Hearth or Shaft Furnace are the most often applied technology for the recycling of dusty steel mill residues world-wide, especially for EAF dust. A pyro-metallurgical process is characterized by the volatilization of non-ferrous metals like zinc, lead and cadmium out of an oxidised solid mixture by means of reduction by coke or coal. In parallel ferrous oxides are also reduced. The target of the recycling process is to make the metals, which are contained in the residues, available for further re-use.
Dr. Juergen Ruetten gives in his paper a general overview of all known recycling techniques for steel mill dust. The commercially applied pyro-metallurgical processes are also compared in detail according to their technical, economic and environmental aspects.
The following briefly reviewed processes represent the most common processes for the treatment of steel mill residues, especially in dust form.
- Waelz Technology: Volatilization of non-ferrous metals like Zn, Pb, Cd etc. out of an oxidized solid mixture by means of reduction by coke breeze in a rotary kiln without generating a liquid slag
- Rotary Hearth: Volatilization of non-ferrous metals like Zn, Pb, Cd and reduction of ferrous metals like Fe, Ni, Cr, Mo out of an oxidized solid mixture by means of reduction by coke or coal on a rotating hearth without generating a liquid slag
- PRIMUS: Combination of rotary hearth to a multiple layer unit with an electric arc furnace for generation of pig iron and liquid slag by means of melting
- Shaft Furnace (OxiCup): Reduction of ferrous metals like Fe and non-ferrous metals like Zn, Pb, Cd by lump coke, volatilization of non-ferrous metals and melting of pig iron and slag by partial combustion of coke
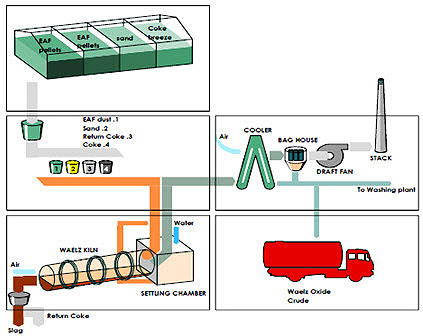
Figure 1: Waelz Plant As a conclusion Dr. Ruetten mentioned that the Waelz process and the Rotary Hearth process are representative for more than 80 % of installed capacity for dusty residues of the steel industry. The Waelz process has its main application for Zn-rich carbon EAF dusts while the Rotary Hearth is focussing on the Fe oxide rich residues from integrated steel works.
The OxiCup is also a process for the residues of integrated steel works with additional advantages in case of existence of metallic iron residues like sculls. All processes will find their application also in the future but due to the simplicity and the wide spread knowledge the Waelz process for carbon EAF dust and the Rotary Hearth for dusty residues from integrated steel works will remain the most common techniques.